If you have a lot riding on your next 3D printing project, and require a powerful printer for ensuring success, historically that means you should turn to Stratasys. Time and time again, you can bet this is who is behind some very serious—and unique—builds, from rocket components to haute couture—and the likes of which you have not seen before.
Submarines though? Indeed, this may be something new to us all, but the Godiva 2 will be ‘the most 3D printed vessel on the grid.’ Whether you are a naval enthusiast or just the average layperson who enjoys the latest innovations in technology, we’ll all agree this sounds impressive from the outset. Now, the question is: will it win? Six students in the UK expect that answer to be yes.
The Godiva 2 will indeed be racing at the European International Submarine Races in Gosport, UK from July 6-15, and the team of engineering students who made the submarine will be cheering it on, hoping—and expecting—that their very modern and complex creation will make them proud. Hailing from the University of Warwick, the industrious engineering team constructed their sub with a range of 3D printed parts meant to offer a leg up in the race, such as fins and the feet where they sit, the propeller’s shroud and blades, and multiple other crucial items such as fixings, housings, and internal steering components.
This was indeed all made possible with Stratasys technology, in the form of the Fortus 3D printer. According to the Warwick Submarine team project leader, Josh Dobson, that particular machine allowed them to build the submarine to their specifications, and on time. More importantly, they were able to build it affordably, and in line with the tight budget constraints imposed on them by the university—an issue common in most educational systems, as there is only so much funding to go around. Employing all the benefits of 3D printing helped the team get around economics—and with the addition of highly durable, quality parts, it may also help them get around their competitors in the water.
“Our extensive use of 3D printing remains one of our strengths,” says Dobson. “Our Stratasys Fortus 3D Printer is very much at the heart of our design and manufacturing process, providing significant benefits that simply could not be achieved via traditional methods.”
“Using this technology, we were able to 3D print final parts for the submarine 90% faster than using conventional manufacturing and also saved £2,000-£3,000 in manufacturing costs. These are parts that can perform in the harshest waters, which is incredible given the speed and cost at which they can be produced.”
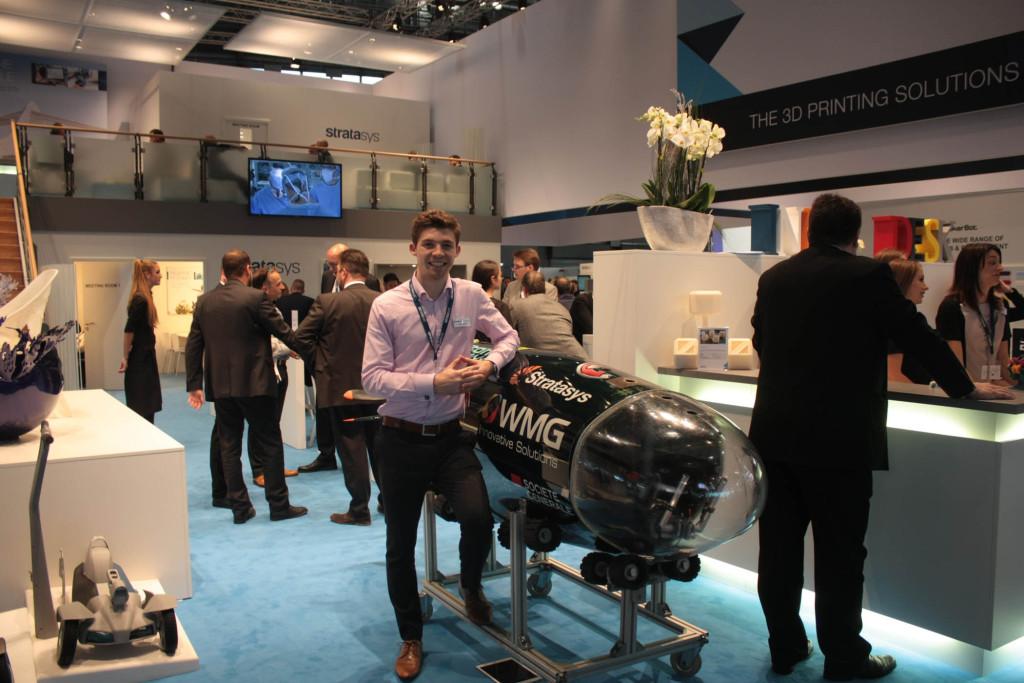
Josh Dobson, Project leader of the 2016 Warwick Submarine, with the Godiva 2 vessel. [Photo: Business Wire]
The students also see that recent material development by Stratasys has truly helped them in their endeavors, allowing them to progress from just using 3D printing as a prototyping tool to actually employing the components within the real construction of their submarine. The ABS-M30 was used for everything except the propeller blades, which were 3D printed by Stratasys.
This is the fourth year the university has competed in the race, again with the challenge for final year Masters engineering students to not only race but also completely build their own submarines for the famed competition requiring a human powered design.
Students were supervised by WMG’s Dr. Ian Tuersley as they worked to create the Godiva 2. The WarwickSub team of six all come from a range of academic backgrounds at the university, with definite strength in mechanical and manufacturing engineering.“Having access to this technology gives us the flexibility to produce extremely complex and multi-functional parts cost-effectively and on-demand,” said Dobson.
“For example, our fixing feet are an incredibly complex piece of geometry and have been 3D printed to perfectly fit the hull at virtually no additional cost, yet remain as functional and strong as a traditionally manufactured part. In addition, by creating the part using 3D printing, we’ve reduced material wastage by about 75% compared to machining the part traditionally from a solid piece of metal, which bodes well for a future of more sustainable manufacturing,” he adds.
It’s exciting not only to see the evolution of Stratasys hardware and materials making a difference, but also how students have been able to benefit from 3D printing so much in terms of customization, self-sustainability in creating and manufacturing, and the ability to work with a budget; in fact, with the Stratasys technology and materials, they were able to produce the 3D printed parts 90 percent faster than they would have traditionally, and they saved substantially in cost as well, up to £2,000-£3,000.
“The Warwick Submarine team is a credit to their university which exemplifies the exciting future of British engineering,” concludes Sig Behrens, General Manager, Global Education at Stratasys. “We are seeing rapid growth in the number of applications that disrupt traditional manufacturing processes to increase speed and reduce costs leveraging our Fortus line for final part production. It’s an exciting future – and for the engineers of tomorrow – it is critical that they learn this technology now as much as possible, as the demand for 3D printing design skills becoming increasingly common.”
While construction of this sub is obviously a central project in their last year, these students also put forth great effort in inspiring other students to engage in STEM-related work. And in order to gain valuable world perspective, the engineering students also collaborate with international industry partners to accentuate their engineering education. As for the race, we’ll all be rooting for Team WarwickSub in July! Do you think 3D printed parts will give this sub an advantage? Discuss in the 3D Printed Sub forum over at 3DPB.com.
Subscribe to Our Email Newsletter
Stay up-to-date on all the latest news from the 3D printing industry and receive information and offers from third party vendors.
Print Services
Upload your 3D Models and get them printed quickly and efficiently.
You May Also Like
Reinventing Reindustrialization: Why NAVWAR Project Manager Spencer Koroly Invented a Made-in-America 3D Printer
It has become virtually impossible to regularly follow additive manufacturing (AM) industry news and not stumble across the term “defense industrial base” (DIB), a concept encompassing all the many diverse...
Inside The Barnes Global Advisors’ Vision for a Stronger AM Ecosystem
As additive manufacturing (AM) continues to revolutionize the industrial landscape, Pittsburgh-based consultancy The Barnes Global Advisors (TBGA) is helping shape what that future looks like. As the largest independent AM...
Ruggedized: How USMC Innovation Officer Matt Pine Navigates 3D Printing in the Military
Disclaimer: Matt Pine’s views are not the views of the Department of Defense nor the U.S. Marine Corps Throughout this decade thus far, the military’s adoption of additive manufacturing (AM)...
U.S. Congress Calls Out 3D Printing in Proposal for Commercial Reserve Manufacturing Network
Last week, the U.S. House of Representatives’ Appropriations Committee moved the FY 2026 defense bill forward to the House floor. Included in the legislation is a $131 million proposal for...