Latest on the my-invention-is-smaller-than-yours catwalk is a compact turbine that despite weighing only 150 pounds can generate sufficient electricity to power 10,000 homes. To give you an idea of what that means in terms of reduction in size, current steam turbines with similar output capabilities are ten times larger. Not only is the newer turbine significantly smaller, it also operates with a 10% increase in efficiency at turning heat into electricity. A further benefit is the system’s ability to quickly power up to quickly generate electricity during peak demand, needing only a couple of minutes to come online in comparison to the half an hour necessary for steam-powered turbines.
This diminutive dynamo, developed at GE Global Research, works using the power of carbon dioxide that is heated to such a high temperature, in this case up to 700°C, it becomes what is known as a supercritical fluid. Rather than using steam to give it spin, this supercritical fluid operates in the realm where the difference between gas and liquid virtually disappears allowing it to generate power in an extremely efficient manner. After passing through the turbine, the supercritical material is cooled, repressurized, and sent through again in a endless repeated cycle that keeps the turbine moving.
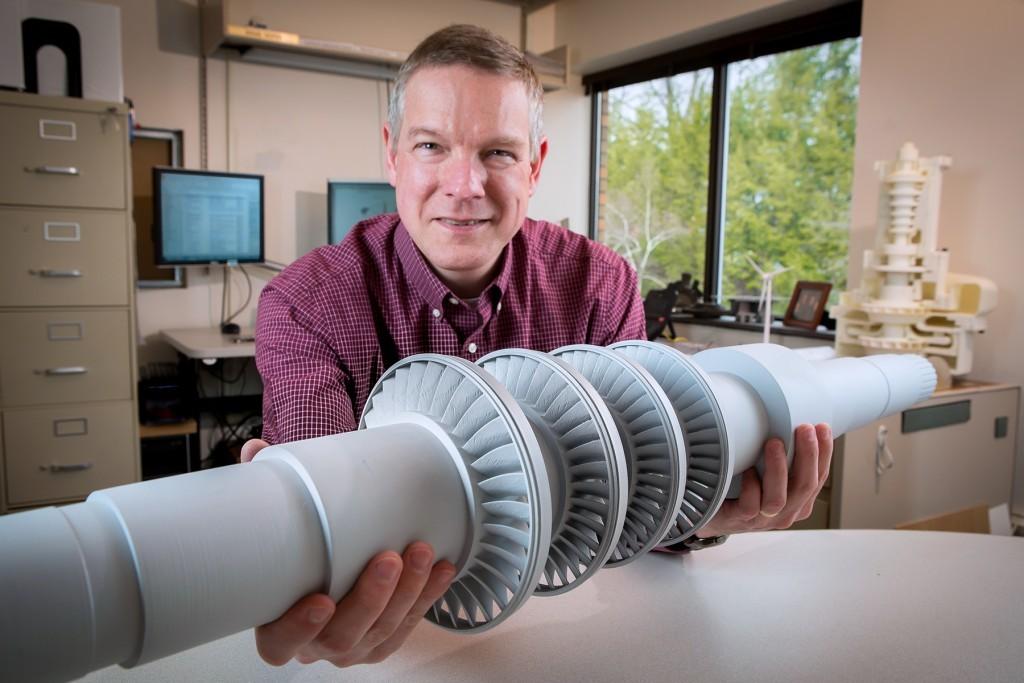
Doug Hofer of GE Global Research holds a 3D printed prototype of the turbine [Image: GE Global Research]
The research is, as of yet, in its early stages, but 3D printing has been a vital tool for study and iteration in the development process. While the final ‘minirotor’ would be high-strength metal, it would have been nearly impossible to advance as quickly without the capabilities of 3D printing to provide rapid prototyping and process oriented models.
The next step in the development of this technology is to determine the possibilities for scaling it up to the 500 megawatt range, the capacity necessary to power a large city. In addition to the cleaner use of CO2 to produce power, the reduction in the footprint of these generators adds up to thousands of acres of landscape that need not be dedicated to simply holding generators. As Doug Hofer, developer of the minirotor explained:
“This compact machine will allow us to do amazing things. The world is seeking cleaner and more efficient ways to generate power. The concepts we are exploring with this machine are helping us address both. With energy demand expected to rise by 50 percent over the next two decades, we can’t afford to wait for new, cleaner energy solutions to power the planet. We have to innovate now and make energy generation as efficient as possible. Programs like those we are working on with the US Department of Energy are helping us get there.”
What do you think of this new technology? Discuss in the GE 3D Printed Turbine forum over at 3DPB.com.
Subscribe to Our Email Newsletter
Stay up-to-date on all the latest news from the 3D printing industry and receive information and offers from third party vendors.
Print Services
Upload your 3D Models and get them printed quickly and efficiently.
You May Also Like
Havaianas Collaborates with Zellerfeld to Launch 3D Printed Flip-Flops
The shoe of the summer is undoubtedly the flip-flop. Easy on, easy off, your feet won’t get sweaty because there’s not much material, and they’re available in a veritable rainbow...
UCLA Researchers Develop 3D Printed Pen that May Help Detect Parkinson’s Disease
Diagnosing Parkinson’s disease is difficult. Often, early symptoms of the progressive neurological condition may be overlooked, or mistaken for signs of aging. Early diagnosis can help save lives and improve...
Printing Money Episode 30: Q1 2025 Public 3D Printing Earnings Review with Troy Jensen, Cantor Fitzgerald
Printing Money is back with Episode 30, and it’s that quarterly time, so we are happy and thankful to welcome back Troy Jensen (Managing Director, Cantor Fitzgerald) to review the...
Heating Up: 3D Systems’ Scott Green Discusses 3D Printing’s Potential in the Data Center Industry
The relentless rise of NVIDIA, the steadily increasing pledges of major private and public investments in national infrastructure projects around the world, and the general cultural obsession with AI have...