Despite the fact that most people seem to have only a limited understanding of the importance of knowing about the past, human beings seem to be consistently interested in knowing about the future. From fortune cookies to palm readings and horoscopes to futurists, people have been trying to peek around the curtain and understand what the future holds for as long as they have lived in anything other than the moment.
Recently, 3D printing has created a replica of one of the world’s oldest efforts to see through the mists of time. The object printed was a copy of a 3,000-year-old oracle bone that contains some of the oldest known Chinese writing. These ancient examples of people’s desire to understand what was to come have provided valuable insight into a variety of aspects of life during the Shang Dynasty and, in fact, have confirmed the lineage of the dynasty itself, whose existence was once held in doubt by a number of scholars.These bones were used as part of the practice of pyromancy, or divination using fire. Questions about the future were inscribed on the bones, generally either the scapulae of an ox or the plastrons of a turtle, and then subjected to heat in a fire. The forms of the cracks created through the heating would then be interpreted by a diviner as a response to the question posed.
The bones were regularly turned up in the soil tilled by Chinese farmers and, unfortunately, often sold as dragon bones to be ground into medicines. Their existence as part of the material record of China’s history was only recognized at the end of the 19th century when Wang Yirong recognized the markings as inscriptions. Since then a large collection of these inscriptions has been amassed and is dispersed among a variety of museums and academic institutions around the world.
One of the difficulties associated with the study of these important artifacts of China’s history is the limited access to them that is a requisite of preserving their integrity. Now, due to high quality, detailed scanning and reproduction options made possible through 3D technologies, the bones can be shared anywhere in the world, anytime, for as long as necessary without damaging the original pieces.
The first of these scanned and printed pieces is oracle bone CUL52 which contains inscriptions detailing the sacrifice of an ox to an ancestor. The scan itself was created by Professor Dominic Powlesland of Cambridge University and pooled approximately 1.3 million aspect points and is able, therefore, to provide a seamless view in 3D of the oracle bone from inscription to divination.
After the scan was created, Powlesland workd with Addenbrooke Hospital’s Media Studio to produce the print of the bone. This partnership was particularly appropriate given the hospital’s possession of a printer primarily used to produce objects for orthopedic and maxillofacial surgery. The final print contains 350 layers and was made of plaster hardened with superglue. Discuss your thoughts on these techniques in the 3D Printed Oracle Bones forum over at 3DPB.com.
[Source: Tech Times]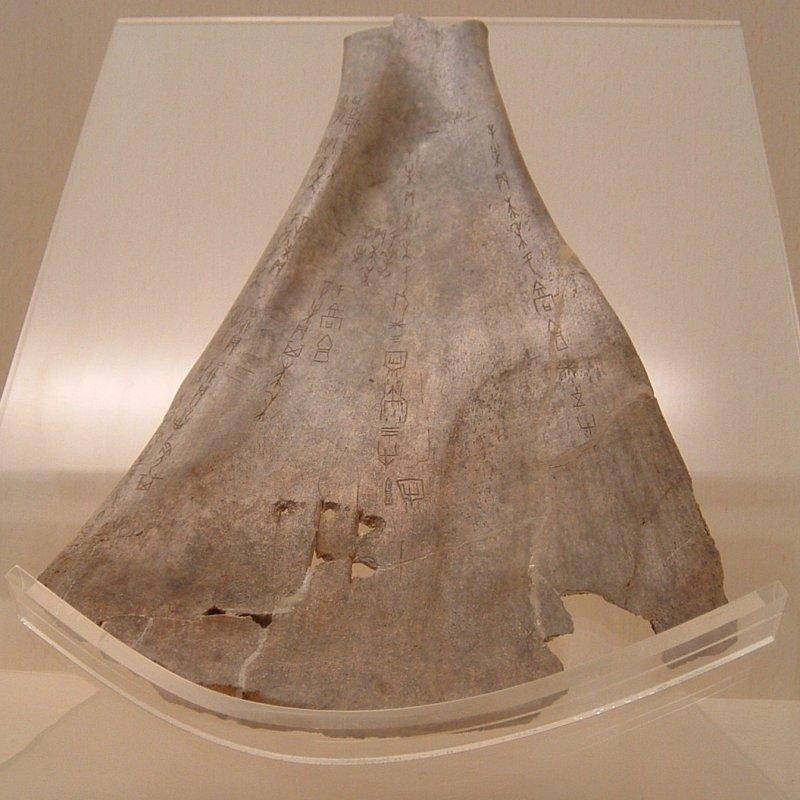
Subscribe to Our Email Newsletter
Stay up-to-date on all the latest news from the 3D printing industry and receive information and offers from third party vendors.
Print Services
Upload your 3D Models and get them printed quickly and efficiently.
You May Also Like
Making 3D Printing Personal: How Faraz Faruqi Is Rethinking Digital Design at MIT CSAIL
What if your 3D printer could think more like an intelligent assistant, able to reason through a design idea, ask questions, and deliver something that works exactly the way the...
Reinventing Reindustrialization: Why NAVWAR Project Manager Spencer Koroly Invented a Made-in-America 3D Printer
It has become virtually impossible to regularly follow additive manufacturing (AM) industry news and not stumble across the term “defense industrial base” (DIB), a concept encompassing all the many diverse...
Heating Up: 3D Systems’ Scott Green Discusses 3D Printing’s Potential in the Data Center Industry
The relentless rise of NVIDIA, the steadily increasing pledges of major private and public investments in national infrastructure projects around the world, and the general cultural obsession with AI have...
Formlabs Teams Up with DMG MORI in Japan
In late June, Nick Graham, Chief Revenue Officer at Formlabs, announced on LinkedIn that the company had partnered with DMG MORI, one of the world’s leading machine tool companies, to...