One of the top goals that material science strives to achieve, is that of the biodegradability of commonly used materials. The planet can only hold so much waste before ecosystems, water supplies, and its atmosphere begins to see horrific damage. For those of you who have a 3D printer, you know how much plastic waste you end up creating. While some of this waste is infact biodegradable, if you use Polylactic acid (PLA) for printing, other materials used are not.
Polylactic acid is derived from renewable resources such as tapioca, sugarcane and corn starch. While it is biodegradable, many recycling plants also recyle it by breaking it down to monomer through processes known as thermal depolymerization or hydrolysis. This monomer can then be used to create new PLA, with properties that are identical to the original. Unfortunately though, PLA isn’t the only material used when producing plastics. Even within the consumer level 3D printing space, many people prefer ABS over PLA due to its strength, flexibility and high temperature resistance.
So what happens in a decade from now, when 3D printers become more prevalent, and the technology is used to create more parts with a greater selection of plastic materials to choose from? Will the world’s plastic waste problem only get worse? Without a doubt, this will be the case unless someone, somewhere, can come up with a method for creating a greater diversity of biodegradable materials.
There may be a solution! Researchers at the Italian Institute of Technology, Ilker S. Bayer, Susana Guzman-Puyol, José Alejandro Heredia-Guerrero, Luca Ceseracciu, Francesca Pignatelli, Roberta Ruffilli, Roberto Cingolani, and Athanassia Athanassiou have come up with a way of transforming edible vegetable waste into bioplastic. Their findings, which appear in the ACS journal, Macromolecules, provide details on the process of creating bioplastics by using waste from vegetables such as spinach, rice, parsley, and cocoa, rather than the traditional methods of using petroleum, which can be very harmful to the environment.
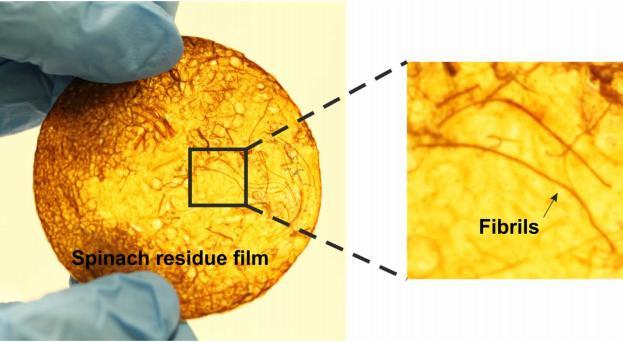
Film from non-dissolvable portion of plant waste solutions (spinach) after 10 days. (Credit: A. Abrusci – Istituto Italiano di Tecnologia )
In 2012 alone, plastic production reached 288 millions tons worldwide; the majority of which are toxic to the environment, and take centuries, or even thousands of years to completely break down.
By using an organic, naturally occurring acid (TFA), the researchers were able to process cellulose, which is the main building block of plants. They mixed this TFA acid with vegetables such as spinach, rice, etc., and then poured this mixture into pretri dishes. They discovered that after some time, films had formed, which featured a varying amount of physical traits. Some were brittle and rigid, while others were soft and stretchable. Most interesting though, was that they were very similar to commercially available plastics.
Waste husks from rice (in the small vial) can be transformed into bioplastic.
(Credit: A. Abrusci – Istituto Italiano di Tecnologia)“This opens up possibilities for replacing some of the non-degrading polymers with the present bioplastics obtained from agro-waste,” the researchers wrote.
With the increasing use of 3D printing, both on a consumer level and industrial level, the potential for more product waste will only grow larger. Even though 3D printing reduces waste that is seen in typical manufacturing, these products that are created with the technology ultimately will end up in a landfill. If researchers can find a way to derive plastics from renewable resources such as vegetables, and then implement them into 3D printing processes such as selective laser sintering or fused deposition modeling, the future may not be all doom and gloom after all.
What do you think? Will we one day have a greater variety of 3D printing materials to choose from which are completely biodegradable? Discuss in the Vegetable derived plastic forum thread on 3DPB.com.
[Source: ACS Publications]Subscribe to Our Email Newsletter
Stay up-to-date on all the latest news from the 3D printing industry and receive information and offers from third party vendors.
Print Services
Upload your 3D Models and get them printed quickly and efficiently.
You May Also Like
Havaianas Collaborates with Zellerfeld to Launch 3D Printed Flip-Flops
The shoe of the summer is undoubtedly the flip-flop. Easy on, easy off, your feet won’t get sweaty because there’s not much material, and they’re available in a veritable rainbow...
UCLA Researchers Develop 3D Printed Pen that May Help Detect Parkinson’s Disease
Diagnosing Parkinson’s disease is difficult. Often, early symptoms of the progressive neurological condition may be overlooked, or mistaken for signs of aging. Early diagnosis can help save lives and improve...
Printing Money Episode 30: Q1 2025 Public 3D Printing Earnings Review with Troy Jensen, Cantor Fitzgerald
Printing Money is back with Episode 30, and it’s that quarterly time, so we are happy and thankful to welcome back Troy Jensen (Managing Director, Cantor Fitzgerald) to review the...
Heating Up: 3D Systems’ Scott Green Discusses 3D Printing’s Potential in the Data Center Industry
The relentless rise of NVIDIA, the steadily increasing pledges of major private and public investments in national infrastructure projects around the world, and the general cultural obsession with AI have...