Colibrium Additive, formerly known as GE Additive, has officially announced the full commercial availability of its Series 3 metal binder jet system. After a measured and meticulous development process, the company is poised to make significant strides in the additive manufacturing (AM) industry with what is among the largest metal binder jet systems on the market. Alongside this, Colibrium Additive is also making notable advancements in electron beam powder bed fusion (EB-PBF) technology, reinforcing its position as a leader in metal 3D printing. To learn more, we spoke to the team at the 2024 International Manufacturing Technology Show.
A Strategic Rebranding and Renewed Focus
The rebranding from GE Additive to Colibrium Additive aligns with the broader restructuring of General Electric into three distinct entities: GE Aerospace, GE HealthCare, and GE Vernova. According to Brian Birkmeyer, Product Line Leader for Binder Jet at Colibrium Additive, the name change is a branding alignment rather than an indication of any organizational upheaval.
“Some people try to read into it, but the reality is it’s just a branding alignment with the split of the different GE businesses,” Birkmeyer explained. He emphasized that Colibrium remains a wholly owned subsidiary of GE Aerospace, continuing its legacy of innovation in additive manufacturing.
This rebranding is part of a strategic move to align with GE Aerospace’s branding while focusing on Colibrium Additive’s specialized expertise in AM technologies.
Series 3: From Redesign to Readiness
The Series 3 metal binder jet system represents a significant leap forward from its predecessor, the Series 2. While the Series 2 was more manual and suited for low-rate production and research and development, the Series 3 is designed for high-throughput, automated production environments.
Birkmeyer acknowledged that the development of the Series 3 was not without its challenges. The company chose to take a step back and re-engineer certain subsystems to meet their stringent performance standards.
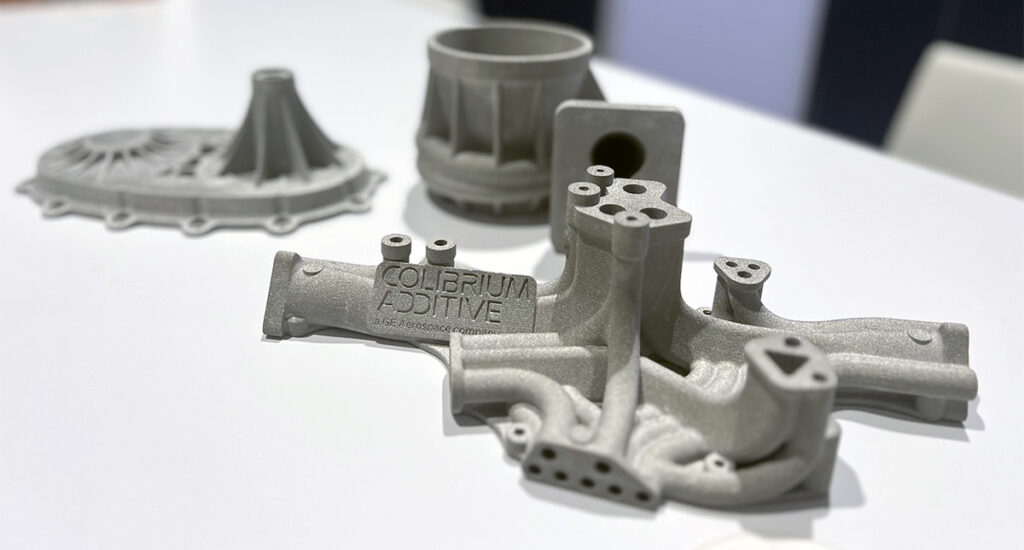
Sizable binder jet parts made with the Series 3 3D printer from Colbrium Additive.
“We took it back to the drawing board a little bit in the second half of last year,” he said. “We re-engineered some things, went back through validation, and now we feel very good about where the product is.”
This deliberate approach resulted in a slower roll-out, but Birkmeyer believes it was essential to ensure the system’s reliability and performance.
“We really just kind of green-lit again at the end of June, early July,” he noted. “So far, reception’s been good. We have to kind of rebuild the pipeline from the beginning to some degree.”
The Series 3 system addresses key industry needs by offering:
- High Throughput: Designed for scalable production, the Series 3 can handle larger volumes with increased efficiency.
- Automated Processes: Reduced need for manual intervention allows for smoother integration into existing manufacturing workflows.
- Strong Green Parts: The system produces robust green-state parts with high density, enabling easier handling and de-powdering without compromising structural integrity.
Birkmeyer highlighted the importance of the system’s ability to produce strong green parts, noting that it enables the production of larger components without the risk of breakage during processing.
“That green strength is what really sets us apart,” he emphasized. “We don’t have to treat the green parts like they’re very fragile. We can be much more aggressive with them through those different steps.”
He demonstrated this by showcasing green parts at the show, inviting select audiences to handle and even attempt to break them, illustrating their robustness.
Ongoing Collaborations with Industry Leaders
Colibrium Additive continues to work closely with established customers. These partnerships have been instrumental in refining the Series 3 system and demonstrating its capabilities in real-world applications.
“We’re still working with prior customers from the Series 2 as well,” Birkmeyer noted. “People are still using those machines, and they’ve got good application spaces.”

Tungsten-carbide parts made with Colibrium Additive’s binder jetting technology and Kennametal’s materials.
He explained that the transition to the Series 3 offers these customers enhanced capabilities with less need for direct support from Colibrium Additive.
“The Series 3 machine is oriented to be more of the ‘here’s the system, go run it’ type,” he said. “Not nearly as much handholding required.”
Birkmeyer highlighted the company’s readiness to support customers in adopting the technology: “We’re here to help. The whole point is to make sure that we can help customers through that process and reduce that learning curve for them once they do put the equipment on their floor.”
Advancements in Electron Beam Powder Bed Fusion (EB-PBF) Technology
In addition to the progress with the Series 3, Colibrium Additive is making significant strides with its EB-PBF machines. Dave Bartosik, Senior Engineer for Emerging Technologies at Colibrium Additive, provided insights into the latest developments, including the Spectra M and EBMControl 6.4.
Colibrium Additive announced the Spectra M EB-PBF printer, addressing the demand for smaller build volumes while maintaining the benefits of electron beam technology, such as high productivity and design freedom.
Bartosik explained the advancements: “Compared to traditional hatch melting with EB-PBF, we can move the beam orders of magnitude faster than laser because we’re using electromagnets instead of mirrors that have to accelerate and decelerate.”
The new EBMControl 6.4 software includes innovations like Point Melt technology, which enhances temperature control and reduces gradients, leading to improved material properties and surface quality.
“We’ve taken that multi-beam technology and applied it to the bulk infill as well,” Bartosik said. “You basically pixelate that layer worth of parts, melting with a lower heat input that spreads more evenly across the part.”
Eliminating the Need for Supports
One of the significant advantages of these advancements is the reduction or elimination of the need for support structures during the build process.
“We don’t need heat sink supports anymore,” Bartosik noted. “It’s basically support-free printing. Our mechanical properties go up to about 10% tighter window between traditional methods.”

On the left, a metal EB-PBF part made without Point Melt, thus necessitating supports. On the right, Point Melt eliminates the need for support structures.
This development not only reduces post-processing costs but also allows for tighter nesting of parts, increasing throughput.
“When you’re stacking everything in there, nesting as tight as you can, you can probably squeeze in an extra layer of parts and just get a little more throughput,” he added.
Impact on Medical and Aerospace Applications
The advancements in EB-PBF technology have significant implications for industries like medical implants and aerospace.
“Traditionally, you see a lot on the orthopedic side of implants,” Bartosik explained. “With the higher strength capabilities of printing, the femoral stems are coming back and being analyzed again.”
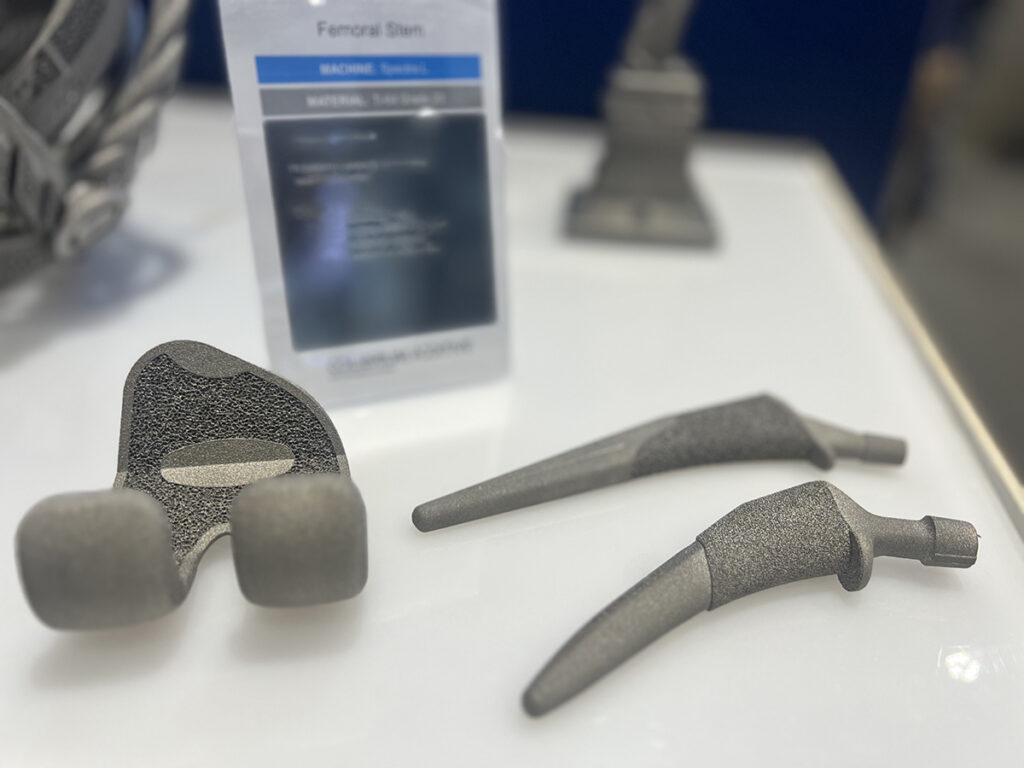
3D printed femoral stem implants made possible with Colbrium Additive’s advancements in EB-PBF.
These advancements have significant implications for the medical industry, particularly in the production of orthopedic implants. Bartosik highlighted that the improved EB-PBF technology now makes it feasible to produce femoral stems—the critical components of hip implants that fit into the femur and support the artificial joint.
“Traditionally, you see a lot on the orthopedic side of implants,”* Bartosik explained. *”The femoral stems are the most critical one. They’re very fatigue-sensitive, and there’s been a hesitancy in the industry to go with metal additive on those parts. The knees, the hip cups, everything else—lower requirements. Now that we’ve got these higher strength capabilities of printing, the stems are coming back and being analyzed again.”
By enhancing the mechanical properties and fatigue resistance through Point Melt technology, Colibrium Additive is enabling the medical industry to reconsider additive manufacturing for these critical, load-bearing components.
These advancements have significant implications for the aerospace sector, which has traditionally relied more on laser powder bed fusion due to its ability to produce fine features and high-precision parts. However, the enhanced mechanical properties and surface quality achieved through Colibrium Additive’s improved EB-PBF technology are making it a more attractive option for aerospace applications that demand high strength and durability.
“With these higher strength capabilities, we can address applications that were previously challenging for electron beam technology,” Bartosik explained. “Everybody likes stronger materials, so it’s good to have.”
By reducing the need for support structures and improving isotropic material properties, Colibrium Additive’s EB-PBF advancements enable the production of complex aerospace components that were once difficult to manufacture using the technology. This opens up new opportunities for the aerospace industry to leverage EB-PBF technology for parts that require superior mechanical properties and performance.
Embracing Competition and Innovation
Both Birkmeyer and Bartosik acknowledged the growing competition in the AM industry, particularly in the metal binder jetting and EB-PBF spaces. They view this competition as a catalyst for innovation.
“Competition’s healthy,” Bartosik stated. “It’s driving all of us to innovate. That was a big chunk of what pushed out Point Melt—to give us a little more competitive edge.”
Birkmeyer echoed this sentiment regarding the binder jet space: “Competition’s good because it pushes people to do better anyway.”
The full commercial release of the Series 3 metal binder jet system marks a significant milestone for Colibrium Additive. The company’s careful approach to development ensures that they are delivering a reliable, production-ready system that meets the evolving needs of the industry.
With continued innovation in both binder jet and EB-PBF technologies, and a commitment to customer collaboration, Colibrium Additive is well-positioned to maintain its leadership in the AM sector.
“We’re just ready to start bringing on the users,” Birkmeyer affirmed. “The Series 3 is here and ready for business.”
Bartosik added, “We’re not resting on our laurels. With Point Melt and other developments, we’re pushing the boundaries of what’s possible in EB-PBF technology.”
Subscribe to Our Email Newsletter
Stay up-to-date on all the latest news from the 3D printing industry and receive information and offers from third party vendors.
Print Services
Upload your 3D Models and get them printed quickly and efficiently.
You May Also Like
Nikon SLM Solutions Sells SLM 500 to Primary Weapon Systems to Expand Suppressor Production
Primary Weapons Systems (PWS) is a Boise, Idaho-based manufacturer of suppressors, firearms, and related components. A subsidiary of Vigilant Gear and a sister company to aftermarket Glock slide manufacturer Lone...
3DPOD 261: Tooling and Cooling for AM with Jason Murphy, NXC MFG
Jason Murphy´s NXC MFG (Next Chapter Manufacturing) is not a generalist service; instead, the company specializes in making tooling. Using LPBF and binder jet, the company produces some of the...
HP and Firestorm Labs Form Partnership to Use Multi Jet Fusion 3D Printers in Deployable Factories
HP Inc., maker of a range of additive manufacturing (AM) solutions including the Multi Jet Fusion (MJF) ecosystem, has announced a partnership with Firestorm Labs, a developer of containerized, deployable...
3D Printing News Briefs, July 2, 2025: Copper Alloys, Defense Manufacturing, & More
We’re starting off with metals in today’s 3D Printing News Briefs, as Farsoon has unveiled a large-scale AM solution for copper alloys, and Meltio used its wire-laser metal solution to...