Ursa Major, the Colorado-based manufacturer of rocket engines produced with additive manufacturing (AM), has unveiled Lynx, the company’s first design and production process for solid rocket motors (SRMs). Given that, in recent history, missile inventories have come to represent the primary application space for SRMs, Lynx is of the utmost relevance to the Department of Defense’s (DoD’s) AM objectives.
Ursa Major has deep experience working with DoD, and, in 2023, won multiple contracts from the Air Force Research Laboratory (AFRL) to build and test liquid propellant engines for the US hypersonic program. In August, the company also extended its partnership with Manufacturing Innovation Institute (MII) America Makes — originally begun in 2021 with the establishment of the Ursa Major Advanced Manufacturing Lab — through mid-2024.
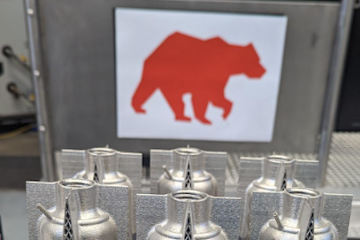
Now, Ursa Major will bring the expertise and innovation it has spent years cultivating and demonstrating in the liquid engine space to the market for SRMs. The company’s chief operating officer (COO), Nick Doucette, who once ran AM operations for SpaceX, explained to 3DPrint.com the significance of this development for both rocket manufacturing as well as the AM sector. The key to understanding both is modularity.
“Every SRM size has different manufacturing challenges,” Doucette told me. “With the larger motors, the main challenges are tooling, getting consistency in the propellant itself, and how to structure the case to ensure its solidity. With the smaller ones, the challenge is more along the lines of how we move from our current process of making this part in twelve steps to just four. So, we’re starting with a smaller design because we can iterate faster. It’s no different from how we approach liquids. We built a small version of our liquid engine first and then tested it over and over again. Once we verified its effectiveness by using all of those lessons, we were able to scale up the process very quickly. That allows us to iterate, learn, and keep moving. From a capital perspective, it also gives a chance to squeeze more out of our capital expenditure, simply because we can do more with the smaller models.”
Smaller models could be especially important for SRMs, specifically, insofar as the missiles they’re most typically used in, such as Javelins and Stingers, are man-portable. This means that they’re designed to be carried by one person over long distances. Currently, one of the biggest obstacles for output of those weapons, which is causing ever-longer lead times for the US defense industrial base (DIB), is the fact that production lines for Stingers only make parts for Stingers, and those for Javelins only make parts for Javelins, etc. However, the modularity of Lynx, only possible thanks to AM, is meant to change precisely that.
“Let’s say we have two or three different man-portable SRM models that we’re making,” Doucette began. “From our perspective, a print’s a print. A print job could be made up of six small SRMs and three big ones, and then back to six small ones and, then, say, six big ones. If you can imagine a factory filled with printers that are making the motor cases, you could easily switch production lines over back and forth between different sizes. That’s one of the biggest challenges for the supply chain in its current form. One production line makes only this one motor, so if we need to increase surge capacity for that man-portable SRM, there’s no choice but to go to that one dedicated line. If you have a factory of printers working on multiple models simultaneously, though, it gives you more control to dictate the makeup of a production surge based on incoming demand. And it is truly ‘one-click,’ because it’s just a model change — it’s open this file, not that file, and that’s all there is to it. Maybe in reality it’s two or three clicks, but you get the idea.”
To be sure, Doucette is only able to make things sound this straightforward because he and everyone else at Ursa Major have spent around a decade conceptualizing, developing, and refining the underlying techniques involved. Nonetheless, the COO said that Ursa Major originally turned to AM for three fairly simple reasons:
“Ursa started out focused on liquid engines, an, from day one, we leaned heavily into additive. There were three theses behind that. The first was speed through development — obviously, manufacturing times can be greatly reduced with 3D printing. That doesn’t always mean it’s the most cost-effective method during the development phase, but it is certainly one of the fastest. The cost-effectiveness comes in afterwards with the second thesis, which is adding simplicity to the manufacturing process: combining parts, reducing the number of steps. On the liquid side, for instance, you can eliminate steps like welding and brazing if you use 3D printing strategically.
“Lastly, the third thesis is improved performance. There’s a weight savings, with a specific geometry that helps maximize and achieve different performance metrics, which you really wouldn’t be able to achieve without very customized additive processes. Our proof of the validity of those three theses has paid dividends over the last five or six years. As we looked at SRMs over the last couple of years, we recognized significant shortcomings in the speed for new product development. Thinking through how much additive helped solve some of the liquid issues and shrunk the development timelines and the manufacturing complexity, we saw the same issues with SRMs… We’ve been shocked about how well additive translates across applications. But essentially what we’re doing is trying to take advanced manufacturing methods, apply them to a very traditional manufacturing process, and doing so to make everything faster and cheaper, which are always common goals for most manufacturing companies.”

The increasing ability of AM to successfully execute in new ways on those age-old objectives of all manufacturing operations has caused the DoD, among others, to start taking the technology very seriously in 2023. According to the new report from Additive Manufacturing Research, Additive Manufacturing for Military and Defense, the DoD will spend an estimated $300 million on 3D printers in 2023. Along these lines, it is becoming more and more evident to those at the intersection of defense and advanced manufacturing that a nation’s AM capabilities are rightly viewed as a form of deterrence: the more missiles the US proves it can make, the less leverage its strategic competitors have in flexing the same muscles.
At the same time, Doucette concluded the interview by pointing out that there’s still much work to be done, when it comes to raising awareness about the connection between manufacturing capacity and national security.
“I hate to draw parallels to the late thirties and early forties, because that was an environment that was radically different from the present. However, to be a global leader in defense and space, a nation needs a certain capacity to manufacture not just consumer goods, but defense hardware and other critical items — for instance, semiconductors. With the CHIPS Act, we saw recognition that, as a nation, we need to control certain aspects that comprise so many critical aspects of our everyday life. So, it may be defense, it may be consumer goods, but the more you depend on external sources, you become a bit exposed. And I think we’re seeing demand gaps grow more and more.
“That data is now becoming more and more relevant, because, unfortunately, there’s an increasing number of conflicts in the world. I hate to say that’s the reason, but it is. Ukraine first, then the conflict in the Middle East, not to mention any sort of simulated conflict in the South China Sea. We’re not measuring deficiencies in missile supply in days or weeks or even months — it’s years. You take SpaceX out of the equation and China outlaunches the US by a ratio of four to one. So we’re seeing that we a re falling behind on developing critical national capabilities. We’re starting to wake up to the fact that we have to be careful about maintaining the types of manufacturing capabilities the US really needs to continue its position as a world leader. And I think deterrence is one of the ten or fifteen things that’s on the list of reasons why we have to make sure we have stable domestic supply chains — from raw material to the final, integrated product.”
Images courtesy of Ursa Major
Subscribe to Our Email Newsletter
Stay up-to-date on all the latest news from the 3D printing industry and receive information and offers from third party vendors.
Print Services
Upload your 3D Models and get them printed quickly and efficiently.
You May Also Like
Nikon SLM Solutions Sells SLM 500 to Primary Weapon Systems to Expand Suppressor Production
Primary Weapons Systems (PWS) is a Boise, Idaho-based manufacturer of suppressors, firearms, and related components. A subsidiary of Vigilant Gear and a sister company to aftermarket Glock slide manufacturer Lone...
3DPOD 261: Tooling and Cooling for AM with Jason Murphy, NXC MFG
Jason Murphy´s NXC MFG (Next Chapter Manufacturing) is not a generalist service; instead, the company specializes in making tooling. Using LPBF and binder jet, the company produces some of the...
HP and Firestorm Labs Form Partnership to Use Multi Jet Fusion 3D Printers in Deployable Factories
HP Inc., maker of a range of additive manufacturing (AM) solutions including the Multi Jet Fusion (MJF) ecosystem, has announced a partnership with Firestorm Labs, a developer of containerized, deployable...
3D Printing News Briefs, July 2, 2025: Copper Alloys, Defense Manufacturing, & More
We’re starting off with metals in today’s 3D Printing News Briefs, as Farsoon has unveiled a large-scale AM solution for copper alloys, and Meltio used its wire-laser metal solution to...