Even to the most experienced users, you sometimes can’t help but get the feeling that 3D printers are just magic. Looking at a fused deposition modeling (FDM) machine—whether it be something like the Bambu Lab P1P, the Ultimaker S7, or the Prusa MK4—the process seems so automatic and effortless, but under the surface, all of this magic is made possible through the use of sensors and control systems.
The precision, reliability, and overall success of FDM printing heavily rely on a suite of sensors integrated within the printer. These sensors, often unnoticed, are the unsung heroes that monitor and control various aspects of the printing process, ensuring the creation of high-quality 3D prints. From filament detection to temperature regulation, bed leveling to position tracking, each sensor plays a unique and crucial role. They work in harmony, providing real-time feedback to the printer’s control system, enabling it to make necessary adjustments and maintain optimal printing conditions.
This article aims to delve into the world of sensors in FDM printers, exploring their types, how they work, and the critical roles they play in the complex symphony of 3D printing.
Temperature Sensors
In FDM printing, one of the most important functions of the machine is to monitor and maintain system temperatures. Within this, the printer may need to control the temperature of the extruder, the build plate, or even the chamber. Without the proper temperatures, an FDM machine will experience failures, such as jams and adhesion issues.
Two of the most commonly used temperature sensors in FDM printers include thermocouples and thermistors.
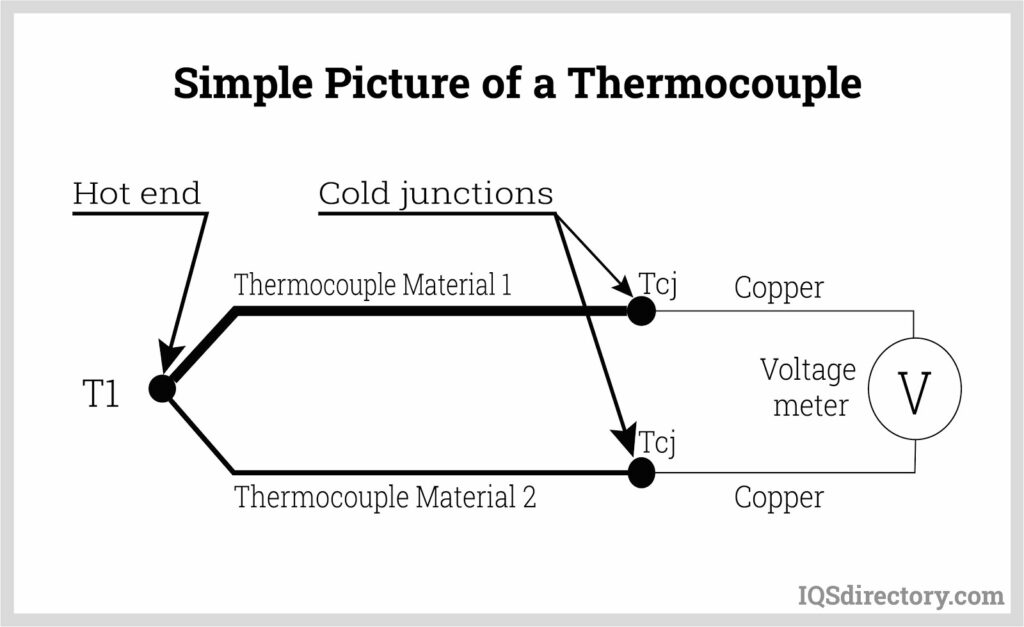
Operation of a thermocouple. Image courtesy of IQS.
A thermocouple is a temperature sensor that consists of two different metals joined together. When the metal junction experiences a temperature difference between the joined end (measuring junction) and the other end (reference junction), a small voltage is generated that is proportional to the temperature difference. From here, the voltage generated by the thermocouple is measured by the printer’s control board and converted into a temperature reading.
Thermistors, on the other hand, work based on the principle that the resistance of certain semiconductor materials changes with temperature. When the temperature increases, the resistance decreases in a negative temperature coefficient (NTC) thermistor. With some supporting circuitry, the printer’s control board measures this resistance and converts it into a temperature reading, allowing it to adjust the heating elements as needed.
Bed Leveling Sensors
To ensure that FDM printers can print successfully without jams or defects, the print bed must be leveled. To this end, bed leveling sensors are a crucial component of FDM 3D printers. There are several types of bed leveling sensors used in FDM printers.
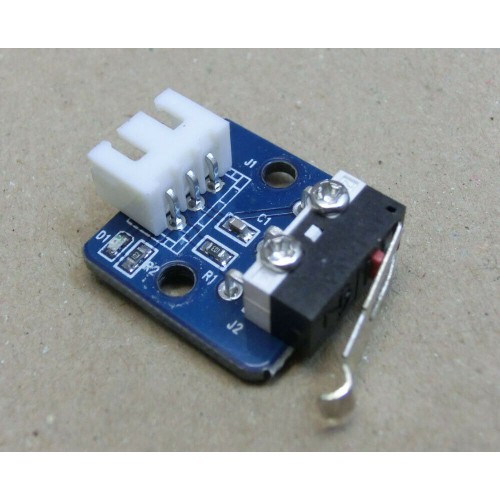
A mechanical endstop switch. Image courtesy of Geeetech.
- Mechanical Switches: These are the simplest form of bed leveling sensors, working on the principle of physical contact. When the nozzle or a separate probe attached to the print head touches the bed, it triggers the switch, sending a signal to the printer’s control board.
- Capacitive and Inductive Sensors: These sensors detect the distance to the bed without physical contact, reducing wear and tear. These sensors detect changes in electric and/or magnetic fields to determine their distance from the print surface. They are typically more precise than mechanical switches, but their readings can be affected by environmental factors such as temperature and humid
With both types of sensors, taking measurements at many points across the build surface allows the system to determine the print bed’s overall levelness.
Optical Endstop Sensors
An optical endstop sensor works based on the principle of light interruption. Generally, optical endstops consist of two main parts: a light emitter (e.g., IR LED) and a light receiver or detector, (e.g., a phototransistor). Positioned such that the light from the emitter reaches the detector under normal conditions, optical endstops detect the presence of an object when the light beam is interrupted.
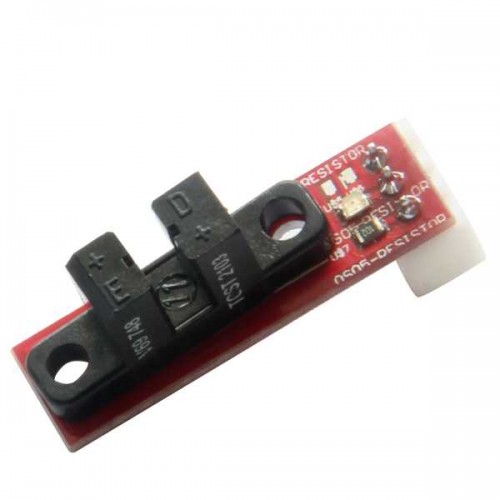
Example of an optical endstop. Image from Geeetech.
In FDM printers, optical endstops are typically located at the ‘home’ positions of the printer’s axes (X, Y, and Z). When the printer starts or when it needs to reestablish its position, it moves along each axis until the corresponding endstop sensor is triggered, indicating it has reached the ‘home’ position. This process, known as ‘homing,’ is crucial for ensuring the printer knows exactly where it is starting from and can accurately control the movement of the print head and bed.
The seemingly magical world of 3D printing, in this case the world of FDM, is powered by a symphony of sensors and control systems working in harmony. Temperature sensors, such as thermocouples and thermistors, diligently monitor and regulate the system temperatures, preventing failures and ensuring smooth prints. Bed leveling sensors, including mechanical switches, capacitive, and inductive sensors, guarantee a level print bed for flawless printing. Optical endstop sensors, with their light interruption technique, enable the printer to establish accurate starting positions and control the movement of the print head and bed. Each sensor, a critical instrument in this intricate dance of technology, contributes to the magic that brings 3D designs to life. Understanding and appreciating the role of these sensors in FDM printing is essential for users and enthusiasts alike, as it unveils the fascinating mechanics behind this captivating realm of technology. So the next time you witness a 3D printer in action, remember the unsung heroes hidden beneath the surface, orchestrating the magic of additive manufacturing.
Subscribe to Our Email Newsletter
Stay up-to-date on all the latest news from the 3D printing industry and receive information and offers from third party vendors.
Print Services
Upload your 3D Models and get them printed quickly and efficiently.
You May Also Like
Consolidation in AM: How 2025 Is Shaping the Industry’s New Normal
The first half of 2025 has been marked by a clear shift in the additive manufacturing (AM) industry. Companies are no longer just focused on developing new tech by themselves....
Etsy Design Rule Change Reduces Selection of 3D Printed Goods
Online marketplace Etsy has implemented a rule change requiring all 3D printed goods on the site to be original designs. The update to the site’s Creativity Standards states, ¨Items produced using...
U.S. Congress Calls Out 3D Printing in Proposal for Commercial Reserve Manufacturing Network
Last week, the U.S. House of Representatives’ Appropriations Committee moved the FY 2026 defense bill forward to the House floor. Included in the legislation is a $131 million proposal for...
Transforming From Tourist to Native: Duro CEO Michael Corr Explains Why the Company Rebuilt its PLM Software on AI
In these early innings of the AI boom, many market analysts have expressed concern that AI spend has gotten too far ahead of the technology’s proven ability to deliver significant...