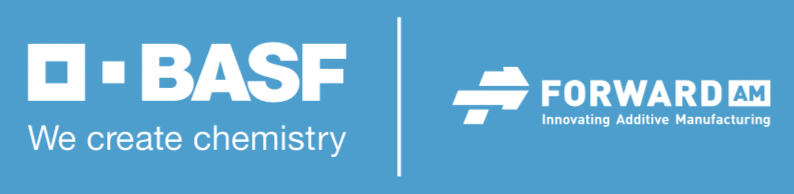
BASF Forward AM has steadily increased its stake in the additive manufacturing (AM) industry, not only through acquisitions such as that of Sculpteo but with the introduction of wholly unique materials. Among those that the company’s Forward AM brand has tackled are flexible polymers, which aren’t limited to a single 3D printing technology but span the gamut from powders for sintering, resins for vat photopolymerization, and filaments for material extrusion.
Flexible Materials in PBF
Across the entire AM industry, material limitations are a consistent issue. Typically, thermoplastics that are standard in injection molding must have specialty formulations prepared for 3D printing. Generally speaking, powder bed fusion (PBF) has a particularly narrow range of available materials, due to the nature of the build process.
When it comes to flexible materials, there are even fewer options, meaning that engineers, product designers, and manufacturers have very little to work with when 3D printing elastic parts. This could be anything from wearable items—like medical devices, shoes, or helmets—to industrial components, such hinges and gaskets.
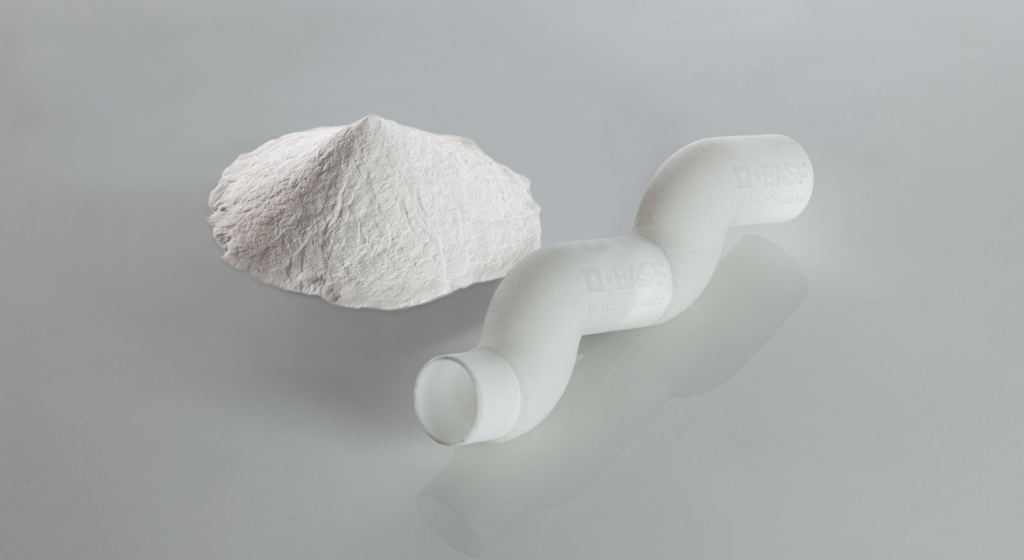
A pipe 3D printed with TPU 88A.
BASF Forward AM is not only one of the leading manufacturers of flexible materials for PBF, but also one of the few. Based on BASF’s Elastollan® line, Forward AM has developed Ultrasint® TPU01 for MJF, as well as TPU 88A and TPU 88A Black for SLS. In fact, Ultrasint® TPU01 is the only flexible material commercially available for the HP 5200 series of MJF 3D printers.
Outside of the benefits of rubber-like properties, Forward AM’s TPUs offer high fatigue-, abrasion-, and impact-resistance. Described as very printable and easy to use, the material is said to have a large application window with high process stability and throughput. All Forward AM TPUs have a biocompatibility statement, meaning that they can be used for skin contact in medical and consumer applications. They have also been tested for UV and rossflex fatigue, assuring durability of the end part for long-lasting use.
This makes Forward AM TPUs ideal for a variety of applications. In industrial settings, 3D printing can be used to create custom jigs and fixtures that may be customized for a given shopfloor task. At the same time, they exhibit impact resistance and noise and vibration reduction, ideal for industrial applications. Outside of general industry, the material also meets regulatory requirements for vehicle interiors, including flame resistance.
For medical applications, the material may be suited for custom prosthetic sockets, due to the skin contact safety of the material, along with its flexibility and stiffness balance. These elements essential for prosthetics, but may also represent low-hanging fruit for orthotists and prosthetists wishing to introduce 3D printing to their practices.
For similar reasons, the materials can be used for consumer goods and protective equipment, such as helmets and footwear. In these instances, lattice structures are perfect for improved foam replacement, as they can be designed to absorb and distribute impact forces, reducing the risk of injury from high-impact activities. These benefits are complemented by the lightweight and breathable nature of 3D printed padding. Forward AM TPUs also have the added advantage of UV resistance.
Forward AM Flexible Filaments
Beyond PBF powders, Forward AM also offers Elastollan-derived filaments, including Ultrafuse® TPU 85A, 95A, and 64D. The filaments are similar to the PBF powders in that they are durable with a high printing success rate and large application window. They also offer high abrasion- and impact-resistance and are compatible with water soluble supports, which is not always the case for flexible materials made by other manufacturers.
The brand’s thermoplastic filaments are said to be more durable. This means the production of jigs and fixtures requiring the same flexibility as polypropylene, as well as wheels and rollers, transport belts, tubes, and hoses in the industrial space. For consumer and medical applications, the company highlights ski boots, ski tips and ends, skateboard rollers, orthopedics/prosthetics, insoles and midsoles as potential use cases. For automotive applications, users might consider sealings, vibration dampers, and decorative covers.
Forward AM Flexible Photopolymers
In addition to powders and filaments, Forward AM offers a variety of flexible photopolymers. With materials such as Ultracur3D® EL 60, EL 150, EL 4000, FL 60 and FL 300, the portfolio consists of a broad range of shore hardnesses, from 40 A to 90 A. The materials require no thermal post-curing and replace traditional finishing-intensive silicon, urethane, and butyl rubber molding, thus minimizing redesign cycle time and cutting the prototype development expenditure.
The high elongation at break of the Ultracur3D® photopolymers makes them ideal for applications that require materials with high levels of flexibility and resilience. The Ultracur3D® flexible product line has been subjected to various tests, including drop tower analysis showing the rebound resilience of the materials as an important indication of their ability to withstand repeated stress and deformation.
The video below shows the specs and results of the test helping customers to choose the right material for their specific needs. Another important material property when it comes to flexible materials is the ability to absorb shocks. This feature is required in many application fields, such as sports equipment to make protective gear such as helmets and padding or consumer goods and industrial as protection of critical components. Due to their unique composition, Ultracur3D® flexible materials provide superior protection against damage and withstand significant impacts.
BASF-Ultracur3D-EL-FL_Drop-tower-test_EN-1
Ultracur3D® materials are known for their fast printing and easy processability, making them a perfect choice for rapid printing without compromising on quality. Besides that, test results for chemical resistance against industrial fluids and the biocompatibility statement are available for almost the full material portfolio, as well as UV stability for Ultracur3D® EL 4000 & FL 60. The materials are used in various industries and applications, such as insoles in footwear, protective gears in sports goods, anatomical models in medical applications, sealings and flexible grippers in the industrial space, as well as functional prototyping.
End-to-End 3D Printing Solutions
In addition to Elastollan’s legacy in the larger manufacturing industry, Forward AM’s TPUs bring with them the benefit of end-to-end solutions, from simulation to post-processing expertise. Through Forward AM’s Ultrasim® 3D Services, it’s possible to quantify how a part will perform when 3D printed with the any of Forward AM’s materials using finite element analysis. Other tools include a total cost of ownership calculator and the Ultrasim® 3D Lattice Engine, which make it possible to integrate lattice geometries into a design.
The ability to feature lattice designs in a 3D printed, flexible part is a key differentiator for products, not only for weight savings and material reduction but for introducing unique design features. For instance, when it comes to padding for medical, sports, and consumer goods, lattice structures will be key for altering the cushion performance of a given product. By altering the lattice pattern within a part, it’s possible to alter its shore hardness all using a single material. The Ultrasim® 3D Lattice Engine will streamline this product development for users keen to optimize designs for AM.
Forward AM has also partnered with leading developers of post-processing technology, AMT and Dyemansion, who enable vapor smoothing and dying of PBF parts to offer product finishes that consumers have come to expect from traditional manufacturing technologies. Moreover, post-processing may be key in certain product requirements for achieving proper tolerances and medical device uses. The ability to apply specialty coatings, specifically Ultracur3D® Coat F+ for elastic materials, means that 3D printed parts aren’t limited in terms of color, with Forward AM able to custom-make nearly any color or effect for coating a flexible, 3D printed component.
Subscribe to Our Email Newsletter
Stay up-to-date on all the latest news from the 3D printing industry and receive information and offers from third party vendors.
Print Services
Upload your 3D Models and get them printed quickly and efficiently.
You May Also Like
Consolidation in AM: How 2025 Is Shaping the Industry’s New Normal
The first half of 2025 has been marked by a clear shift in the additive manufacturing (AM) industry. Companies are no longer just focused on developing new tech by themselves....
Etsy Design Rule Change Reduces Selection of 3D Printed Goods
Online marketplace Etsy has implemented a rule change requiring all 3D printed goods on the site to be original designs. The update to the site’s Creativity Standards states, ¨Items produced using...
U.S. Congress Calls Out 3D Printing in Proposal for Commercial Reserve Manufacturing Network
Last week, the U.S. House of Representatives’ Appropriations Committee moved the FY 2026 defense bill forward to the House floor. Included in the legislation is a $131 million proposal for...
Transforming From Tourist to Native: Duro CEO Michael Corr Explains Why the Company Rebuilt its PLM Software on AI
In these early innings of the AI boom, many market analysts have expressed concern that AI spend has gotten too far ahead of the technology’s proven ability to deliver significant...