AddUp, an original equipment manufacturer (OEM) in metal 3D printing, announced its participation in a $1.5 million United States Air Force (USAF) research contract. The aim is to harness the potential of laser powder bed fusion (LPBF) and surface finishing technologies to produce Inconel-718 (IN-718) components for existing armament systems. As part of this initiative, AddUp will be working in collaboration with REM Surface Engineering, a specialist in superfinishing technology, and Zeda, a 3D manufacturing company formerly known as PrinterPrezz and Vertex Manufacturing.
Backed by a Direct to Phase II Small Business Innovation Research (SBIR) contract, this project is all about providing a new way to boost the readiness and performance of the USAF’s weaponry systems. The project, called “Development of Manufacturing, Heat Treatment, and Surface Finishing Guidelines to Yield Ready-to-Use IN-718 Additive Manufacturing Components,” is going to explore how different combinations of heat treatment, 3D printing settings, and REM’s special surface finishing technology can influence a component’s qualities, such as its tensile strength (how much it can be stretched without breaking) and fatigue life (how long it can endure repeated stress).
AddUp and Zeda will play a vital role in this exciting endeavor. Their goal is to create a set of manufacturing guidelines that can maximize the abilities of LPBF to meet the USAF’s objectives in keeping their fleet ready and efficient.
Bulking up IN-718
In high-demand situations, like those faced by the USAF, the fatigue strength of machine parts, or how well they can resist wear and tear from repeated use, is crucial. Machine parts that get used repeatedly, like the wing of a plane, need to be strong enough to withstand the constant strain; basically, it needs to have “fatigue strength.” That’s where IN-718 comes in. This super metal, a nickel-based superalloy, has high fatigue strength and stands up well to high temperatures and corrosive environments, making it a popular choice in the aerospace and defense industries.
Key to this endeavor is AddUp’s FormUp 350 machine, designed to boost the fatigue properties of IN-718. This super metal, a nickel-based superalloy, is tough, heat-resistant, and resilient against corrosive environments – qualities that make it a top choice in the aerospace and defense industries. For the task, the machine uses a mix of fine powder and a device known as a roller recoater to improve the surface finish of the material, making it even stronger and more durable.
By ensuring an even layer of powder, smoothing out surface irregularities, and minimizing defects, the machine improves the fatigue resistance of the printed components. This is especially important in aerospace and defense, where long-lasting structural integrity and reliable performance are key.
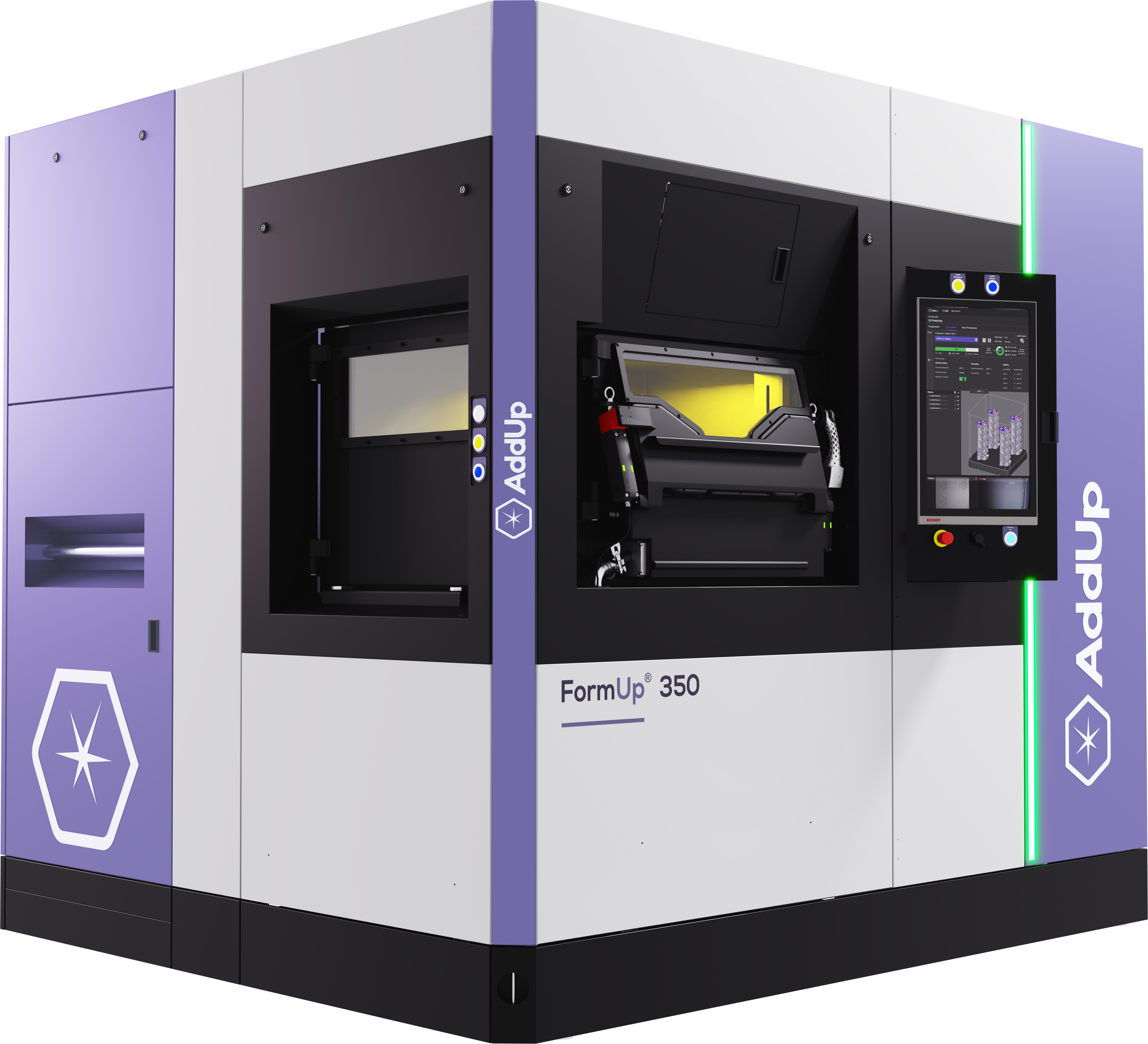
Checking the strength of IN-718 parts made through AM is another vital step in ensuring their quality and reliability. This process, known as fatigue testing, is where AddUp and Zeda come in. They will use AddUp’s FormUp 350 machine and LPBF to create IN-718 test pieces. REM will then use these pieces in a series of tests to find out what we can expect from IN-718 parts made with various levels of surface finish and different production and heat treatment settings. The goal is to confirm the strength of IN-718 parts made with AddUp’s FormUp 350 LPBF technology.
The project, which is about developing guidelines for creating ready-to-use IN-718 parts with AM, marks a big step forward in enhancing the USAF readiness and abilities. It aims to leverage the possibilities offered by LPBF technology and in-depth fatigue testing to boost the performance, reliability, and cost-effectiveness of parts used in aerospace and defense by reducing downtime and ensuring smooth, uninterrupted operations, providing a significant benefit to the industry.
Subscribe to Our Email Newsletter
Stay up-to-date on all the latest news from the 3D printing industry and receive information and offers from third party vendors.
Print Services
Upload your 3D Models and get them printed quickly and efficiently.
You May Also Like
Nikon SLM Solutions Sells SLM 500 to Primary Weapon Systems to Expand Suppressor Production
Primary Weapons Systems (PWS) is a Boise, Idaho-based manufacturer of suppressors, firearms, and related components. A subsidiary of Vigilant Gear and a sister company to aftermarket Glock slide manufacturer Lone...
3DPOD 261: Tooling and Cooling for AM with Jason Murphy, NXC MFG
Jason Murphy´s NXC MFG (Next Chapter Manufacturing) is not a generalist service; instead, the company specializes in making tooling. Using LPBF and binder jet, the company produces some of the...
HP and Firestorm Labs Form Partnership to Use Multi Jet Fusion 3D Printers in Deployable Factories
HP Inc., maker of a range of additive manufacturing (AM) solutions including the Multi Jet Fusion (MJF) ecosystem, has announced a partnership with Firestorm Labs, a developer of containerized, deployable...
3D Printing News Briefs, July 2, 2025: Copper Alloys, Defense Manufacturing, & More
We’re starting off with metals in today’s 3D Printing News Briefs, as Farsoon has unveiled a large-scale AM solution for copper alloys, and Meltio used its wire-laser metal solution to...