In 3D Printing News Briefs today, Meltio is expanding its worldwide partner network, and 3D Systems introduced its VSP Connect portal. Oregon State University and Sandia National Laboratories received a grant to investigate carbon sequestration in 3D printed building materials, and Continuous Composites unveiled its commercial CF3D Enterprise system at the University of Illinois Urbana-Champaign. Finally, a new case study discusses how 3D printing was used to create bird-shaped drones.
Meltio Welcomes New Companies to Worldwide Partner Network
Multinational laser metal deposition technology manufacturer Meltio is working to meet the growing demand for its wire-laser metal 3D printing solutions by expanding its worldwide sales network. Its technology is built around welding wire, which is the cleanest, safest, and most affordable metal feedstock, and enables industrial applications. The Spain-based company has signed sales contracts with four new reseller partners—one in the United States, one in Argentina, another in Italy, and also one in Spain. These new partners will help increase the presence of its Meltio Engine CNC and Robot integration, as well as its Meltio M450 metal 3D printer in different industries.
U.S. company Accufacture LLC will play a major role in distributing and supporting Meltio’s metal AM solutions in the Midwest as a certified system integrator and official sales partner. It will work to build a supportive ecosystem, specializing in integrating the Meltio Engine with Fanuc robot arms. A supportive ecosystem for Meltio’s technology will also be built in Italy, thanks to Wire Trading SRL, which will drive business opportunities alongside academia, robotic integrators, tooling machine companies, and more. DPR Automatismos, just 40 km from Barcelona, is also an official integrator in Spain and Portugal of the Meltio Engine for metal AM with a robotic arm; the agreement was finalized through Meltio’s Iberian sales partner Sicnova. Finally, Tecmahe will work build an ecosystem for distribution and support of Meltio’s solutions in the Argentine market.
3D Systems Announces VSP Connect Surgical Planning Portal
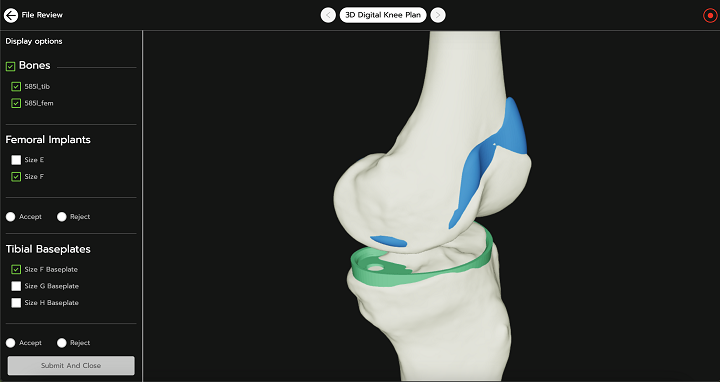
3D Systems (NYSE:DDD) has introduced its cloud-based VSP ® Connect, a centralized portal that integrates both AI and automated workflows in order to streamline preoperative surgical planning. The portal will empower surgeons and medical device manufacturers with improved collaboration capabilities and real-time patient case visualization, which will benefit compliance and traceability, and also facilitate better communication. VSP Connect is empowered by Enhatch, with which 3D Systems already partners to scale personalized medical device delivery; the portal uses its automation and AI technologies, incorporated with 3D Systems’ FDA-cleared workflows for patient-specific solutions. The secure portal enhances 3D Systems’ surgical planning capabilities with its automated workflows, and offers pre-populated designs tailored to standard product types, as well as individual surgeon preferences. All told, VSP Connect should help reduce procedure times and improve patient outcomes.
“3D Systems is on a mission to transform healthcare through the use of additive manufacturing to make patient care easier and smarter. With VSP Connect, we are providing access to the healthcare industry’s most complete additive manufacturing ecosystem,” explained Benjamin Johnson, Vice President, Portfolio & Regulatory, Healthcare, 3D Systems. “Combined with Enhatch technology, our unified approach makes it easier to deliver patient-specific implants and instrumentation in a more efficient, cost-effective manner. It’s part of our ongoing commitment to innovation and helps ensure our customers are at the forefront of medical device development and healthcare delivery.”
Carbon Sequestration in 3D Printed Building Materials

Researchers from Oregon State University and Sandia National Laboratories have received a $540,000 grant from the US Department of Energy for research that could potentially make the construction sector much greener. During the three-year grant, the team, which includes industry partners Graymont and Verdant Building Alternatives and researchers from the Indian Institute of Science and the Indian Institute of Technology Roorkee, will investigate the capture of carbon dioxide from industrial emissions, and then its sequestration in a mineralized form in 3D printed building materials. Developed in England in the early 1800s, Portland cement is the most common type of binder used in concrete, and typically produced by mining, grinding, and heating limestone and clay in industrial kilns up to 2,820°F. This process changes the chemistry of the materials and creates the main cement component, called “clinker,” but also generates plenty of CO2. As Pavan Akula, assistant professor of civil engineering in the OSU College of Engineering, explains, lowering the carbon footprint of cement-based building materials is necessary to make the decarbonization and climate targets set forth by the Paris Agreement.
“The construction industry is responsible for generating 13% of global CO2 emissions. In recent years, 3D-printing technology for concrete has been gaining popularity in building construction as it is a more sustainable alternative – it reduces both waste and transport costs. However, most 3D printing of concrete still relies only on traditional materials that are really carbon intensive,” Akula said.
“We plan to capture CO2 emitted from the lime and cement industries and develop sustainable binders capable of storing and mineralizing the captured CO2 in printed building components such as walls. Our project aims to develop technologies and materials that can significantly reduce the carbon footprint of materials used in 3D printing.”
CF3D Enterprise Unveiled at University of Illinois Urbana-Champaign

Top manufacturer of continuous carbon fiber 3D printing solutions Continuous Composites Inc. announced that it unveiled its commercial CF3D Enterprise system at the University of Illinois Urbana-Champaign. The university held a ceremonial ribbon-cutting and technical symposium in honor of the occasion, and academic and industry experts gave presentations that showcased the potential of Continuous Fiber 3D technology (CF3D) and the many opportunities for the future of manufacturing. Attendees got to see the CF3D Enterprise system up close and learn about how it could impact their industries, and the event also celebrated the university and Continuous Composites continuing their strategic partnership to advance composites manufacturing. The purchase and installment of the system is a major milestone for the pair, and will help usher in new opportunities.
“The CF3D® technology has the potential to revolutionize the composites industry, and we are excited to take our partnership with Continuous Composites to the next level. The CF3D Enterprise™ machine is a platform ripe for innovation and will enable us to advance our research and education programs and create new opportunities for our students, faculty, and industry,” said Dr. Jeffrey Baur, Founder Professor of Aerospace Engineering at the University of Illinois Urbana-Champaign and a longtime partner of Continuous Composites during his service at the Air Force Research Lab.
3D Printed Robotic Bird Drones
Dutch technology company The Drone Bird Company develops fixed-wing and flapping wing bird-shaped drones for the purpose of solving pest bird problems in a non-lethal way, and its falcon drone bird has been in use commercially for the past several years. The lifelike drones can chase birds out of harm’s way, and the main target audience is the aviation industry, which reports that bird strikes and interference can cause up to $500 million in damages each year, according to the FAA. But the company wanted to add polymer 3D printed components to the robotic drone body, instead of the typical fiberglass and epoxy, which were driving down profitability. So it partnered with AM industry veteran EOS, 3D printing service provider Parts on Demand, and Advanced Laser Materials (ALM), an EOS company, to make it happen.
The selective laser sintering (SLS) EOS P 396 system was used to print the body of the drone, and several cover-flaps, using ALM’s customized, buoyant, lightweight PA 640-GSL carbon material. This material makes the drone stronger and more durable, so it can withstand the final product requirements, like holding up under certain weather conditions, and mimicking a bird in flight by flapping its wings, but without stabilizers. The drone can be used together with traditionally manufactured parts, but adding 3D printing to the mix helps to reduce material waste, cost, and production time, and offer more versatility in design, shape, development, and wall thickness. To learn more, you can read ALM’s full case study here.
Subscribe to Our Email Newsletter
Stay up-to-date on all the latest news from the 3D printing industry and receive information and offers from third party vendors.
Print Services
Upload your 3D Models and get them printed quickly and efficiently.
You May Also Like
Nikon SLM Solutions Sells SLM 500 to Primary Weapon Systems to Expand Suppressor Production
Primary Weapons Systems (PWS) is a Boise, Idaho-based manufacturer of suppressors, firearms, and related components. A subsidiary of Vigilant Gear and a sister company to aftermarket Glock slide manufacturer Lone...
3DPOD 261: Tooling and Cooling for AM with Jason Murphy, NXC MFG
Jason Murphy´s NXC MFG (Next Chapter Manufacturing) is not a generalist service; instead, the company specializes in making tooling. Using LPBF and binder jet, the company produces some of the...
HP and Firestorm Labs Form Partnership to Use Multi Jet Fusion 3D Printers in Deployable Factories
HP Inc., maker of a range of additive manufacturing (AM) solutions including the Multi Jet Fusion (MJF) ecosystem, has announced a partnership with Firestorm Labs, a developer of containerized, deployable...
3D Printing News Briefs, July 2, 2025: Copper Alloys, Defense Manufacturing, & More
We’re starting off with metals in today’s 3D Printing News Briefs, as Farsoon has unveiled a large-scale AM solution for copper alloys, and Meltio used its wire-laser metal solution to...