As the aviation industry continues to struggle with rising costs and the question of long-term environmental sustainability, there may be an option that can help with both problems. The 3D printing of airplane parts is already a reality, and it not only helps cut down on emissions, it also presents a cheaper alternative to conventional manufacturing. In fact, Boeing says it saves $3 million per plane when it uses 3D-printed parts.
For now, 3D printing is generally limited to prototyping and manufacturing less-essential parts, but with rapidly advancing technology, that could change. One day, we may even see some of the most important parts of planes being made this way, including key engine components.
But what impact could 3D printing have on safety-critical hardware and systems? And how is the mindset of using 3D printing on the assembly line changing the aviation industry as a whole?
Advantages of 3D-Printed Airplane Parts
The advantages of using 3D-printed parts on airplanes aren’t limited to cost savings. There’s also increased prototyping capabilities, faster and more precise manufacturing, and a smaller carbon footprint.
Let’s start with prototyping. Creating prototypes with 3D printed parts saves thousands of hours of work time, since a new prototype or model can be printed in minutes instead of created over days or weeks. It’s also easy to make changes with 3D printing compared to traditional manufacturing, since you can quickly create and view a low-cost prototype in a more affordable material. In other words, you can see how an aircraft part will look and use it for aerodynamics testing and analysis in a lighter, less costly material than the final product and make adjustments prior to investing in a full-cost metal component.
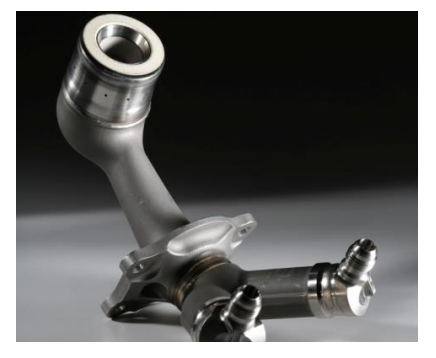
3D printing has also made manufacturing faster and more precise, especially in the area of fixtures that aid in the manufacturing process. To reduce the margin for change and error from one part to another, parts created through traditional manufacturing need to be held in place during machining by fixtures, like metal pins. But the time it takes to make thousands of fixtures, or the cost of purchasing them, is a constant challenge for traditional manufacturers. By contrast, 3D printing allows manufacturers to create thousands of fixtures at just 40 percent of the cost and effort traditional manufacturing requires.
Finally, saving all that time and effort in prototyping and manufacturing means more parts can be manufactured with less energy and waste. Since manufacturing and production cause over a fifth of the world’s total carbon emissions, prioritizing more sustainable manufacturing should be a given. 3D-printing could reduce material consumption by up to 90 percent. That leads to a considerably smaller carbon footprint.
Is 3D Printing in Aviation Safe?
Still, 3D printing comes with some safety concerns due to the way the process works. 3D printing relies on layering lightweight materials to form parts, rather than cutting the parts from blocks of heavy, strong material. The layering process has often resulted in weaker, more porous or breakable final products. Due to the strict nature of hardware certification requirements, the FAA was initially slow to certify 3D printed parts that were more likely to break or suffer damage than parts made with traditional manufacturing. Now, with new technology finally allowing titanium 3D printing, the materials and therefore the final product are stronger than ever before, and it’s likely that certification could move more quickly going forward.
After all, the safety protocols and regulations surrounding 3D-printed aircrafts and their parts are comprehensive enough to ensure that any 3D printed materials that end up on planes will not negatively affect safety. DO-254 and related standards for aviation hardware already require a deep level of testing and quality assurance, which helps to assure that 3D printing will either only apply to parts that are not safety-critical or will involve enough checks and tests to keep people and aircraft safe.
Aviation Trends Around 3D Printing
3D printing is only one small aspect of how avionics is changing. But the mindset around 3D printing could help bring a whole new system of air travel to fruition, as well as change the way aircraft manufacturers think about compliance and certification.
Better 3D printing could help overcome some of the current supply chain challenges for aircraft manufacturing. As such, it could help to power Urban Air Mobility (UAM). UAM is the concept that one day we might all use air taxis instead of, or in addition to, traditional cars. But for UAM to work, we need a lot more small-scale aircraft. 3D printing could facilitate that process.
For example, vertical take-off and landing aircraft (VTOLs) are an important technology for UAM, since they don’t require large runways and can fly at low altitudes with ease. Developers are currently working on 3D-printed parts for these aircraft. In fact, just this month, a new VTOL aircraft prototype from Horizon Aircraft took to the skies with nearly 800 3D-printed parts.
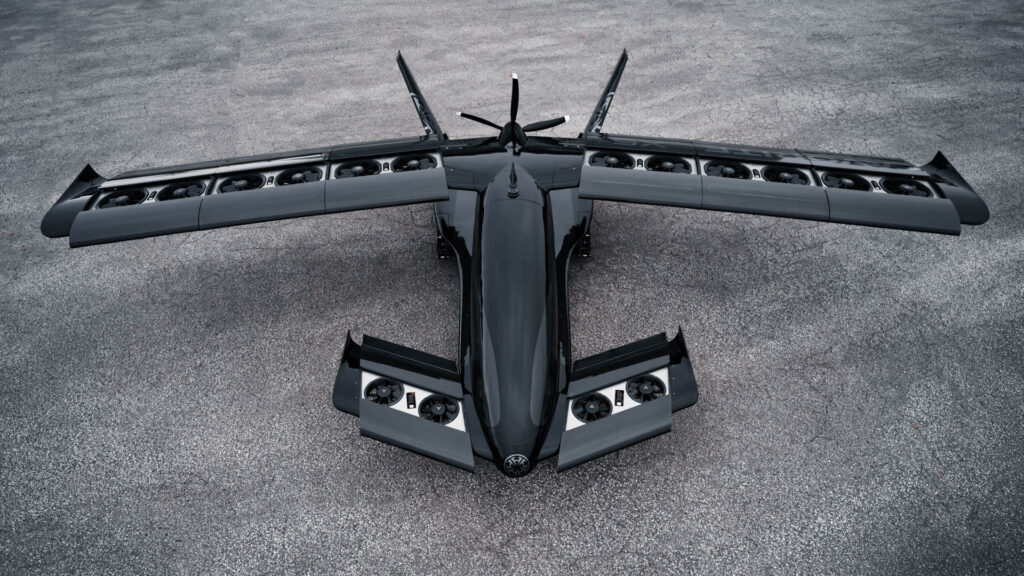
Plus, just as 3D printing could in the future facilitate a building blocks approach to manufacturing aircraft, we’re also seeing the industry adopt a kind of “assembly line” mindset when it comes to both software and hardware compliance and certification building blocks in avionics.
For example, templates are an essential building block of compliance and certification, since they allow manufacturers and aircraft developers to certify new designs in a way that is efficient and repeatable. So just as 3D printing provides a building blocks-based approach to prototyping and manufacturing parts, there are various types of templates that can act as building blocks to how companies design, manufacture, and develop new aircraft and ensure compliance based on standards like DO-178C for software, DO-254 for hardware, and others.
It will be exciting to see how 3D-printing will continue to contribute to the development of modern technologies and processes in aviation and elsewhere. Maybe one day you’ll fly in an aircraft that has been 100% 3D printed, and perhaps one day, an air taxi will be as familiar to you as an Uber is today.
About the Author
Vance Hilderman, is the principal founder/CTO of three of the world’s most significant aviation development/certification companies including TekSci, HighRely, and AFuzion. Hilderman has trained over 31,000 engineers in over 700 aviation companies and 30+ countries. His intellectual property is in use by 70% of the world’s top 300 aviation and systems developers worldwide, and he has employed and personally presided over 500 of the world’s foremost aviation engineers on 300+ projects the past thirty-five years. AFuzion’s solutions are on 90% of the aircraft developed over the past three decades. His latest book, Aviation Development Ecosystem, debuted at #1 on the Aviation category best-seller list.
Subscribe to Our Email Newsletter
Stay up-to-date on all the latest news from the 3D printing industry and receive information and offers from third party vendors.
Print Services
Upload your 3D Models and get them printed quickly and efficiently.
You May Also Like
Nikon SLM Solutions Sells SLM 500 to Primary Weapon Systems to Expand Suppressor Production
Primary Weapons Systems (PWS) is a Boise, Idaho-based manufacturer of suppressors, firearms, and related components. A subsidiary of Vigilant Gear and a sister company to aftermarket Glock slide manufacturer Lone...
3DPOD 261: Tooling and Cooling for AM with Jason Murphy, NXC MFG
Jason Murphy´s NXC MFG (Next Chapter Manufacturing) is not a generalist service; instead, the company specializes in making tooling. Using LPBF and binder jet, the company produces some of the...
HP and Firestorm Labs Form Partnership to Use Multi Jet Fusion 3D Printers in Deployable Factories
HP Inc., maker of a range of additive manufacturing (AM) solutions including the Multi Jet Fusion (MJF) ecosystem, has announced a partnership with Firestorm Labs, a developer of containerized, deployable...
3D Printing News Briefs, July 2, 2025: Copper Alloys, Defense Manufacturing, & More
We’re starting off with metals in today’s 3D Printing News Briefs, as Farsoon has unveiled a large-scale AM solution for copper alloys, and Meltio used its wire-laser metal solution to...