A powerful combination between innovation and the emergence of additive manufacturing has increased the demand for high-quality material alloys. 3D printing has become a powerful tool for making geometrically complex and customized parts, and the metal hardware market is one of the fastest-growing segments of additive manufacturing. However, not all metals lend themselves to 3D printing easily, and costs for AM metal materials have always been significantly higher than those for traditional manufacturing processes. Despite the challenges of developing metal powders and alloys suitable for 3D printing, more material suppliers are designing new metal resources for the technology.
One new partnership could help solve the lack of material options in the aerospace and space industries in particular. Now that SLM Solutions announced it is teaming up with Elementum 3D to design exclusive aluminum alloys for SLM technology, many applications stand to benefit from the materials.

According to the companies, the aerospace and space industries are eager to integrate new materials. Still, they have faced various challenges with difficult-to-print, highly sought-after alloys that are prone to cracking. Although they are used to the materials’ versatility, high strength, and corrosion resistance, cracking has become a real pain point for the hyperactive aerospace industry.
AM materials suppliers
The duo will create four new materials for SLM Technology that will be available to users as soon as 2023. Among them, high-strength aluminum alloy 2024 is suitable for aerospace projects requiring a high strength-to-weight ratio and excellent fatigue resistance, such as wing and fuselage structures that frequently come under tension. Another upcoming material will be the 7050 aircraft aluminum alloy, described as a heat-treatable aerospace grade material with very high mechanical properties and fracture toughness, making it popular against corrosion cracking and at subzero temperatures, and commonly seen in aircraft structure and rocket propeller parts.
Additionally, the collaboration will result in exclusive aluminum alloys 6061, one of the most widely used aluminum alloys for structure applications, and 7075, one the strongest aluminum alloys with a strength comparable to many steels.
Harnessing additive technologies and new alloy designs open up new opportunities for the direct production of end-use components for aerospace and space applications. Through this partnership, both companies are teaming up to further enhance material offerings on the SLM’s twelve-laser technology in its NXG XII 600E used to print end-use parts traveling to space.
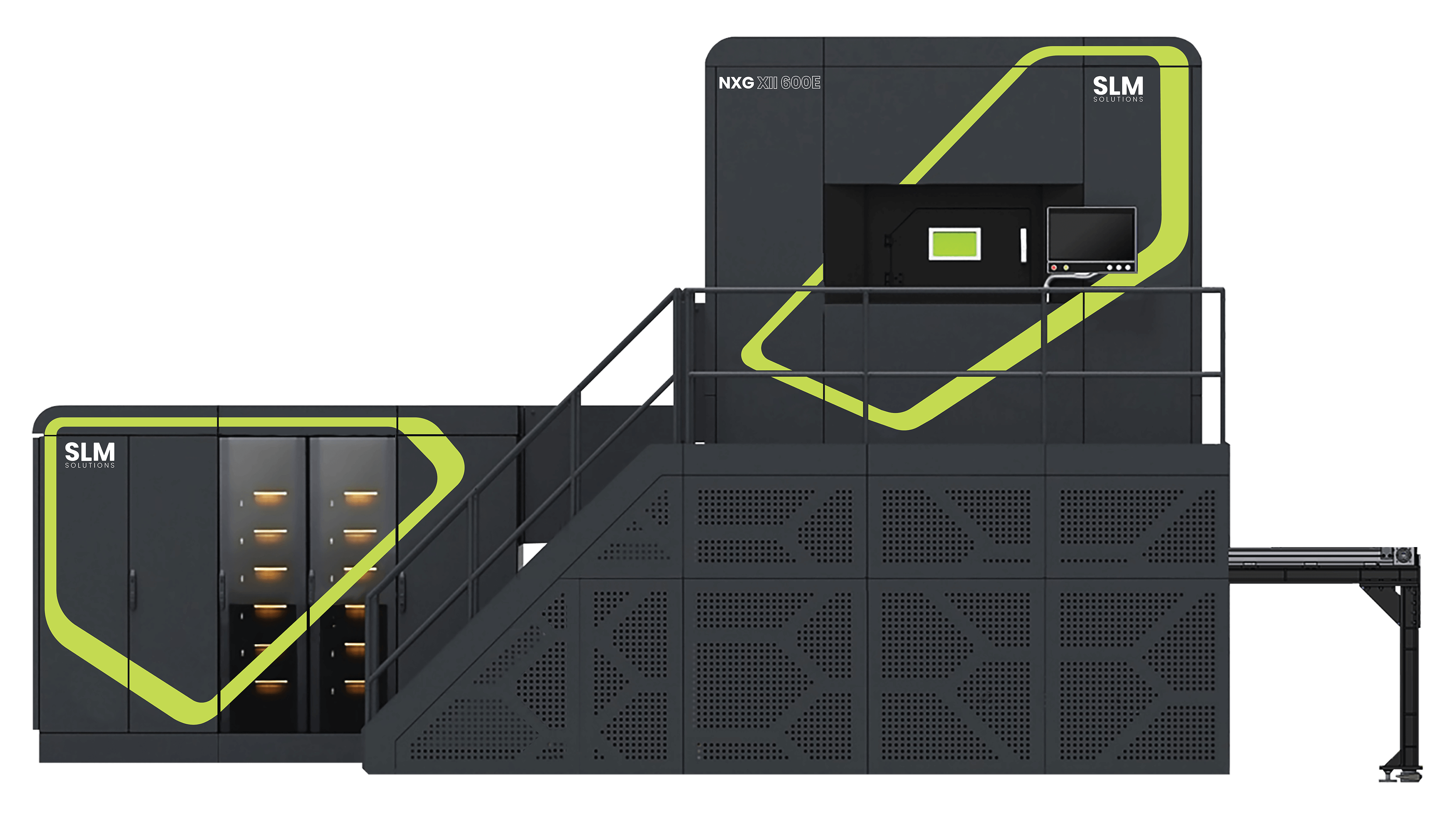
As part of the deal, Elementum 3D’s reactive additive manufacturing (RAM) technology to synthesize product materials in situ during the additive fusion process will ensure safe processing and successful outcome of additively manufactured parts with these difficult-to-print materials and therefore opens completely new possibilities in terms of component size, processing speeds, and material properties.
In addition to and within the start of the joint development agreement, Elementum 3D acquired SLM Solutions’ most productive machine, the NXG XII 600. Together, the companies are committed to providing and developing cutting-edge technologies and materials to create parameters and market Elementum 3D materials for use in SLM machines, especially on the NXG XII 600.
Achieving challenging materials
As a result of the agreement, the companies expect to expand the use of additive manufacturing, increase the exposure for Elementum 3D materials and allow SLM Solutions to grow the material selection for its 12-laser system rapidly.
Both companies top executives expressed their excitement about the partnership, significantly how new materials will help offer better solutions for organizations ready to take their ideas to production. By providing customers with an enhanced material portfolio for their applications, the companies are “focusing on accelerating the idea-to-production platform,” as SLM Solutions CEO Sam O’Leary described. Elementum 3D Founder and President Jacob Nuechterlein added that the new material products would be ground-breaking for the company.
This collaboration between hardware original equipment manufacturer SLM Solutions and material provider Elementum 3D is an excellent opportunity to solve customers’ problems and one we see more of lately. Working together is essential to advance the industry to new heights, especially as there continues to be an innovation of fascinating new products in many industries, and the demand for high-quality material alloys is likely to accelerate.
Subscribe to Our Email Newsletter
Stay up-to-date on all the latest news from the 3D printing industry and receive information and offers from third party vendors.
Print Services
Upload your 3D Models and get them printed quickly and efficiently.
You May Also Like
Consolidation in AM: How 2025 Is Shaping the Industry’s New Normal
The first half of 2025 has been marked by a clear shift in the additive manufacturing (AM) industry. Companies are no longer just focused on developing new tech by themselves....
Etsy Design Rule Change Reduces Selection of 3D Printed Goods
Online marketplace Etsy has implemented a rule change requiring all 3D printed goods on the site to be original designs. The update to the site’s Creativity Standards states, ¨Items produced using...
U.S. Congress Calls Out 3D Printing in Proposal for Commercial Reserve Manufacturing Network
Last week, the U.S. House of Representatives’ Appropriations Committee moved the FY 2026 defense bill forward to the House floor. Included in the legislation is a $131 million proposal for...
Transforming From Tourist to Native: Duro CEO Michael Corr Explains Why the Company Rebuilt its PLM Software on AI
In these early innings of the AI boom, many market analysts have expressed concern that AI spend has gotten too far ahead of the technology’s proven ability to deliver significant...