
Glidewell, the largest privately owned dental lab in the U.S., is poised to commercialize its proprietary micro-CT scanner for use in other industries. The California-based company has worked diligently to make an impact in computed tomography technology, effectively finding a balance of affordability, speed and size to help facilitate digital and additive manufacturing (AM) workflows.
In an industry where AM is projected to reach a global market size of $16.4 billion by 2030[1], it was critical they get a jump on the competition and make a mark of their own. After buying and using CT scanners offered by other companies, it soon became clear that what they needed was not being fulfilled by those machines. Costs started to mount due to the steep price tag and constant repairs. The scanners were slow and cumbersome, unable to cycle through the substantial demands necessary for the lab’s production. It was at this point that the company decided to take matters into their own hands.
“The superpower of CT scanning is that it’s not limited by line of sight,” said Glidewell Senior Vice President of Engineering, David Leeson. “In our manufacturing field, as well as many others, scanners are complimentary to additive manufacturing in that they can inspect complex geometry. Our scanners can accomplish that in a sped-up, high-demand workflow at a fraction of the cost of currently available scanners.”

Because of Glidewell’s unique workflow in which every physical impression of teeth sent in by dentists is converted into a digital file, they are responsible for CT scanning hundreds of thousands of objects every year — a massive undertaking that is dependent on reliable equipment. The engineering team had to figure out how to make a scanner that reconciles speed with quality, while also making it small and affordable. They surely had their work cut out for them, but with the support and resources of the entire company, they were able to address the glaring deficiencies of the other commercial scanners:
- Cost: Being affordable was a cornerstone of Glidewell’s approach to developing a CT scanner. The ability to scale up production at any point as the market demanded meant that budget should not be a determining factor when making that decision. At a fraction of the cost of other scanners, Glidewell operates nearly 100 scanners today.
- Speed: Not only do Glidewell’s CT scanners scan quickly, but they are also exceptional for constant cycling and mass production lines. They can execute a three-dimensional scan at 50 microns in just 30–60 seconds, allowing for details unseen by the naked eye to be identified. Additionally, after a scan is completed, while the digital file is still being uploaded to Glidewell’s in-house cloud service, the next round of items can be staged in the CT scanner, allowing for an asynchronous sequence of events, saving time and increasing productivity.
- Size: Precious real estate makes the size of scanners critical. And because the objects being scanned are so small and detailed, the large, bulky scanners were deemed inconvenient and unnecessary. Glidewell’s scanners are smaller and more compact without curtailing any of the quality of a larger scanner. With a body measuring only 37.5 x 20 x 15 inches, they are fit for companies that want to conserve space.
Additionally, the success of the scanner is best exemplified in its versatility, especially in the field of quality control. As it is able to examine highly detailed tooth and product designs to ensure an accurate fit that both the dentist and patient could be happy with. The small footprint and high-resolution digitization capability make Glidewell’s CT scanners ideal for inspecting and discovering hidden defects, inaccuracies or errors from the manufacturing process.
Glidewell is actively exploring new industries and applications for the CT scanners and is excited about the possibility of commercialization. Due to its precision and applicability, the new technology can be especially valuable in industries such as medical device manufacturing, automotive, industrial metrology and quality assurance, among many others.
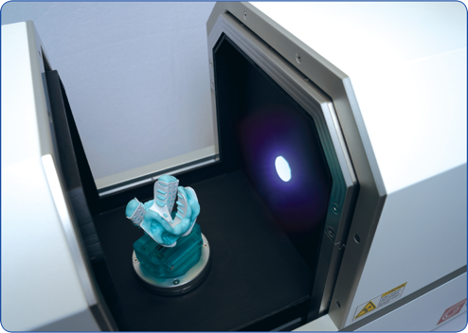
“Our goal was to democratize CT scanning,” said Leeson. “The vast majority of available scanners were intended for university and research institutes, not necessarily for factory lines. Our scanners are quick, reliable and relatively simple to use, allowing them to be operated by anyone and opening the door for many other industries to get in on the benefits without such a high barrier of entry.”
As additive manufacturing continues to grow in the field of dentistry and other industries at large, there will be a greater demand for personalization in quality control and scalability of equipment. As exemplified by this CT scanner, the engineers at Glidewell have stepped up to the plate to address those concerns with flying colors.
[1] Market Stats Ville: Dental 3D Printing Market 2022 [internet]. Cited 2022 June. Available from: marketstatsville.com/dental-3d-printing-market
Subscribe to Our Email Newsletter
Stay up-to-date on all the latest news from the 3D printing industry and receive information and offers from third party vendors.
Print Services
Upload your 3D Models and get them printed quickly and efficiently.
You May Also Like
Consolidation in AM: How 2025 Is Shaping the Industry’s New Normal
The first half of 2025 has been marked by a clear shift in the additive manufacturing (AM) industry. Companies are no longer just focused on developing new tech by themselves....
Etsy Design Rule Change Reduces Selection of 3D Printed Goods
Online marketplace Etsy has implemented a rule change requiring all 3D printed goods on the site to be original designs. The update to the site’s Creativity Standards states, ¨Items produced using...
U.S. Congress Calls Out 3D Printing in Proposal for Commercial Reserve Manufacturing Network
Last week, the U.S. House of Representatives’ Appropriations Committee moved the FY 2026 defense bill forward to the House floor. Included in the legislation is a $131 million proposal for...
Transforming From Tourist to Native: Duro CEO Michael Corr Explains Why the Company Rebuilt its PLM Software on AI
In these early innings of the AI boom, many market analysts have expressed concern that AI spend has gotten too far ahead of the technology’s proven ability to deliver significant...