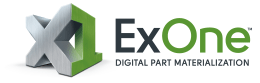
In the world of consumer products, speed is the name of the game. The faster products get to market, the faster they can be purchased by consumers. To maintain a true-to-factory-appearance and superior product quality for their exterior automotive panels, OAM needed durable and flexible tooling. Steel, composite, or wood tools required constant maintenance while aluminum tooling was cost and time prohibitive.
OAM turned to ExOne 3D printed thermoforming tooling after traditional methods proved to be unsustainable for business. Zach Kowalik, CEO and Co-Founder, explained the challenges of the original tooling made of steel, composite, or wood. “They required a lot of repair and maintenance, and we often struggled to place vacuum holes in precise locations due to the material and design constraints.” Although seen as the gold standard of thermoform tooling, OAM avoided aluminum because it was cost and lead time prohibitive.
With speed to market front of mind and in need of a tooling option that increased durability while also offering more flexible vacuum-hole routing, the company researched binder jetting. “When we finally discovered 3D printed tooling, we felt like we struck gold,” Kowalik said.
OAM typically receives its X1 ThermoForm tooling delivery about two weeks after finalizing its design. After the shape 3D printed on ExOne sand binder jetting machines the tool is infiltrated and coated to provide the durability to withstand vacuum forming production. Compared to past aluminum tools ordered by the company, the X1 ThermoForm tool was half the cost and saved over three months of lead time.
“This is a game-changer for the industry,” Kowalik said, emphasizing the role rapid tooling plays in speeding time to market. “Our product launch times are an order of magnitude faster than we could have ever dreamed of before.” The previously targeted one launch per quarter, but Kowalik now sees the company launching a product each month with the speed and cost-effectiveness of sand tooling while making product volumes not previously viable profitable and product variations an opportunity for expansion.
With quality standards akin to Class A automotive, OAM requires precision tooling that delivers consistently high results. Download the complete case study with durability results as OAM scans its 3D printed sand tool after several production runs.
Subscribe to Our Email Newsletter
Stay up-to-date on all the latest news from the 3D printing industry and receive information and offers from third party vendors.
You May Also Like
Printing Money Episode 17: Recent 3D Printing Deals, with Alex Kingsbury
Printing Money is back with Episode 17! Our host, NewCap Partners‘ Danny Piper, is joined by Alex Kingsbury for this episode, so you can prepare yourself for smart coverage laced...
Insights from Cantor Fitzgerald on AM’s Q1 2024 Landscape
A recent survey by Cantor Fitzgerald sheds light on the persistent challenges within the additive manufacturing (AM) industry in the first quarter of 2024. Based on responses from 38 industry...
3D Printing Financials: Xometry’s Scaling up and Strong Start to 2024
Xometry (Nasdaq: XMTR) kicked off 2024 with strong results, boosting its marketplace and technology to new heights. Both revenue and gross margin soared, fueled by an expanding global network of...
3D Printing Financials: Desktop Metal Targets Recovery Amid Net Losses and Revenue Downturn
Despite facing a decline in revenue and the persistent challenges of a tight economic climate, Desktop Metal (NYSE: DM) is making strides toward operational efficiency. The first quarter of 2024...