RadTech has recognized three companies for their leadership in sustainability through 3D printing technology as part of its annual sustainability awards. The nonprofit association, known for promoting the use and development of ultraviolet (UV), electron beam (EB), and light-emitting diode (LED) technologies, selected four winners in 2022. Each represents a different sector of the UV/EB/LED end-user market, and each offers a unique product sustainability advantage.
From Sydney, Australia, RadTech chose MicroTau for their microprinting technology work to improve airliner performance. The company found a way to recreate sharkskin patterns that reduce aerodynamic drag, which helps increase flight efficiency and performance.
Working out of a small lab in the University of Sydney’s School of Physics in 2015, MicroTau Founder and CEO, the experimental physicist and entrepreneur Henry Bilinsky, developed a new fabrication technique. Combining computer chip fabrication and ultraviolet-curable coating technology, Bilinsky’s method uses light to print drag-reducing microstructures, called riblets, into aircraft paint to reduce fuel consumption.
These riblets were initially discovered by looking at sharks’ skin under a microscope and noticing that millions of years of evolution have made its ridges decrease drag so sharks would become more efficient hunters. At the time, Bilinksy and his startup even won a contract with the U.S. Air Force, seeking a way to reduce fuel consumption on their legacy transport aircraft.
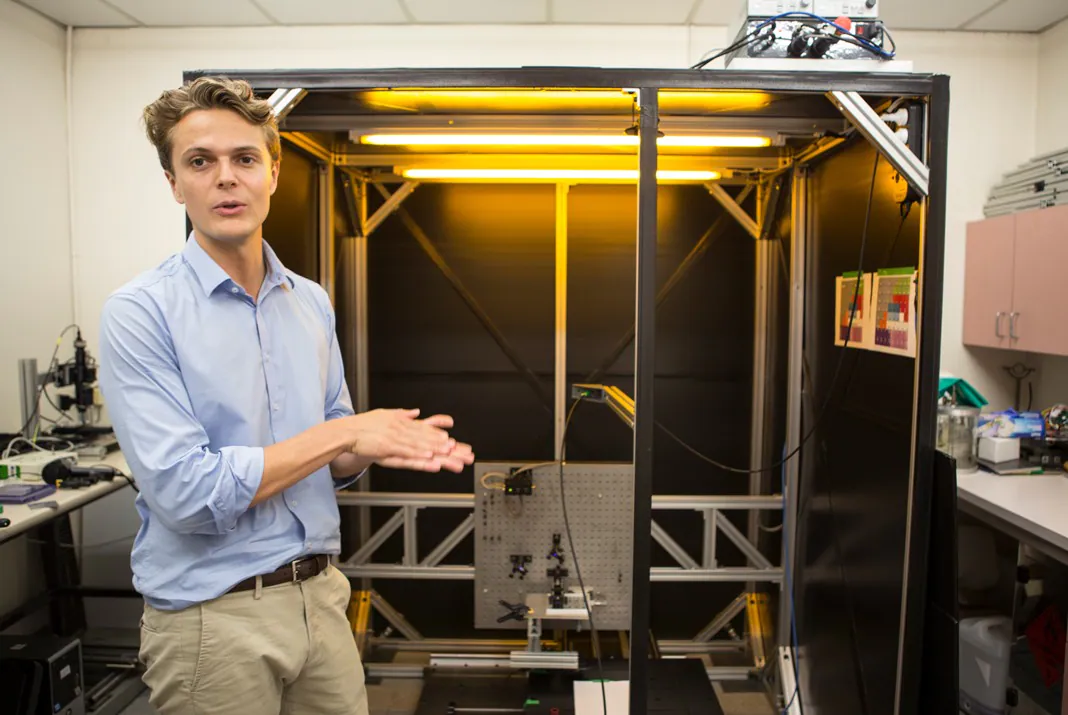
Henry Bilinsky, in his lab at the School of Physics, explained how the prototype prints sharkskin structures onto a surface using light. Image courtesy of the University of Sydney.
Like many other startups, MicroTau is a bioinspired business looking to nature to solve humanity’s problems. According to the company, the natural microscopic patterns found on plants and animals have functional properties, so the group decided to create a proprietary new advanced manufacturing process called Direct Contactless Microfabrication (DCM) technology, or “Nature’s 3D printer,” which replicates these microscopic patterns and can also reproduce its valuable qualities.
MicroTau’s DCM recreates microscopic patterns with light and is scalable to large surfaces. As a result, it has the potential to offer faster, cheaper, more versatile microfabrication, at least an order of magnitude improvement over existing technologies. In addition, it can print out current UV curable coatings used in industries like aerospace, shipping, and energy.
By recreating sharkskin patterns, MicroTau can reduce aerodynamic drag. So far, it grows these patterns out of UV curable coatings and has demonstrated performance in wind tunnel and flight testing; in fact, 3D printed riblets reliably showed 7% drag reduction.
Considering that aircraft and ships spend most of their fuel overcoming drag, MicroTau’s innovation can save commercial aviation, maritime, and energy industries more than $10 billion in fuel costs and as much as 100 million tons of carbon emissions annually. In addition, MicroTau is scaling up its manufacturing to deliver the technology to airliners and improve sustainability.
Wood that doesn’t burn?
Additionally, RadTech chose Texas A&M University researchers Thomas Kolibaba and Jaime Grunlan as recipients of its “Special Academic Award” for their work on fire-resistant wood coatings that limit the flammability of wood used in construction. This environmentally friendly process could also be applied to other flammable materials, such as photopolymer 3D printed parts.
With the potential to mitigate the spread and damage of fire, the newly developed coating treatment doesn’t have many of the drawbacks typically associated with fire retardant solutions, including the toxicity of commercially available halogenated flame retardants (these are being regulated out of the marketplace due to health and bioaccumulation concerns).
The application of this technology has the potential to be used in a variety of markets, including compatible wood treatment solutions and fabric finishing textile treatment. In fact, Kolibaba suggests that UV-cured polymers could also be used as a resin to make 3D printed parts that are otherwise flammable when produced with conventional resins. In addition, he observed that this could be a significant advantage in aerospace applications, including the International Space Station.
This is not the first time Kolibaba has incurred in additive manufacturing solutions. Last year, the graduate student and postdoctoral researcher at the university’s Grunlan Lab published a paper on an environmentally benign flame retardant polyamide‐6 filament for 3D printing and was previously engaged in research on a self-extinguishing AM filament.
For his latest coating development, there is also potential as a preventive measure against future forest fires. Ultimately, the team behind the invention hopes that the coating will become accessible to anyone who needs it, allowing those who live in high-risk areas to treat their own homes and property with the coating to protect against fire damage.
Finally, award winners Water Gremlin from White Bear Lake in Minnesota, and the duo Thistle and Bee from Memphis, Tennessee, and GOpak Flexibles from Delafield, Wisconsin, also came up with ingenious developments. Water Gremlin has implemented a solvent-free UV curable coating process for battery terminals with less environmental impact than traditional coatings. While Thistle and Bee and GOpak Flexibles created flexible yet sustainable packaging for GOpak’s granola bars using 100% recyclable material and electron beam curing to make the packaging safe for consumption.
Winners will be celebrated at the Awards Dinner during RadTech 2022, taking place May 9 through 12 in Orlando.
Subscribe to Our Email Newsletter
Stay up-to-date on all the latest news from the 3D printing industry and receive information and offers from third party vendors.
Print Services
Upload your 3D Models and get them printed quickly and efficiently.
You May Also Like
Consolidation in AM: How 2025 Is Shaping the Industry’s New Normal
The first half of 2025 has been marked by a clear shift in the additive manufacturing (AM) industry. Companies are no longer just focused on developing new tech by themselves....
Etsy Design Rule Change Reduces Selection of 3D Printed Goods
Online marketplace Etsy has implemented a rule change requiring all 3D printed goods on the site to be original designs. The update to the site’s Creativity Standards states, ¨Items produced using...
U.S. Congress Calls Out 3D Printing in Proposal for Commercial Reserve Manufacturing Network
Last week, the U.S. House of Representatives’ Appropriations Committee moved the FY 2026 defense bill forward to the House floor. Included in the legislation is a $131 million proposal for...
Transforming From Tourist to Native: Duro CEO Michael Corr Explains Why the Company Rebuilt its PLM Software on AI
In these early innings of the AI boom, many market analysts have expressed concern that AI spend has gotten too far ahead of the technology’s proven ability to deliver significant...