Volkswagen Group’s Bentley Motors is doubling the additive manufacturing (AM) capacity at its factory in Crewe, England, responsible for assembly of all Bentley models. Thanks to an investment of £3m investment into the technology, the luxury brand will be able to expand its ability to 3D print parts for a variety of uses.
Bentley claimed that 3D printing has allowed for a 50 percent reduction in cost for parts. In the past, the luxury brand has used AM to 3D print parts for prototype vehicles, including full-scale powertrain and aerodynamic wind tunnel models. Components were also fabricated for record-breaking Bentley used in the Pikes Peak Challenge in America. During the height of the pandemic, some of its 3D printers were used to make face shields for the healthcare sector.
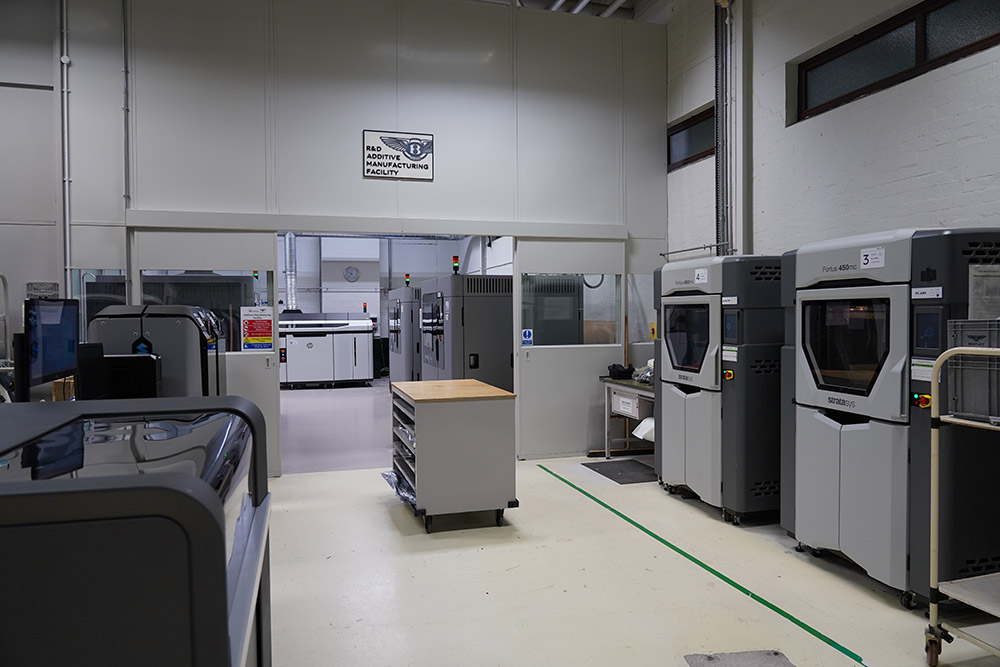
Bentley’s 3D printing facility. Image courtesy of Bentley Motors.
According to the company, Bentley 3D printed over 15,000 parts at the facility in 2021 alone. The manufacturer said that it had already selected some components that it would make with AM, including tooling to assist in the manufacturing process. This includes lightweight sanding blocks used in its wood shop, as well as aids for the assembly of the Bentley Blower Continuation model.

The 1929 Bentley Blower, which Bentley recreated with 3D printing. Image courtesy of Bentley Motors.
Bentley suggested that future 3D printed items may include end parts and greater personalization for customer cars. The idea is that AM would speed up product development for the company, while also allowing it to produce parts without outsourcing. To enable further use of the technology, Bentley is training employees throughout the company in the use of AM.
“Bentley’s approach to additive manufacturing is industry-leading and the facility is quickly becoming a cornerstone of our ‘Dream Factory’ ambitions. One of the key benefits is that it is efficiency led, cutting down on the cost and complexity of a myriad of jobs,” said Peter Bosch, Bentley’s Member of the Board for Manufacturing. “This latest investment is also making a significant impact with our colleagues from across the company, helping to create advanced assisted tools to drive continuous improvement throughout manufacturing processes. As we look to the future, there really is huge potential to where this advanced technology can progress, including having a greater ability to personalize parts for our customers and further enhancing the individualization program offered on every car.”
After autosports racing, luxury vehicles have done the most to introduce 3D printed end parts to the automotive sector. While racecars offer the ability for teams to produce one-off components for high-performance, specialty applications, luxury cars allow manufacturers to expand such experiments to small batches.
Increasing 3D printing capacity at Bentley falls into a larger strategy of AM adoption at the Volkswagen Group, which claims that it will be 3D printing 100,000 parts by 2025. Meanwhile, VW competitor BMW has also steadily increased its use of the technology, including in its Rolls-Royce luxury line. As far back as 2016, Rolls-Royce was using thousands of 3D printed parts in some of its vehicles.
The use of AM fits into VW’s larger goals of transforming its production line as it shifts to electric vehicles, with a goal of making half of its sales electric by 2030. Bentley in particular is slated to produce only electric vehicles by that same year, with its first electric vehicle debuting in 2025. As part of its Dream Factory concept, Bentley hopes to provide customers with unique experiences in which bespoke designs are combined with digital manufacturing. That certainly sounds like customers will be able to go into the facility, customize a nameplate or other feature, and have it 3D printed before their eyes.
“With our new ‘Dream Factory’ concept, we now go to zero also with water, waste, and other environmental impacts until 2030,” Bosch said. “Unique craftsmanship, customer interaction, and employee experience will be enhanced by digital tech, higher flexibility, and new ways of personalization.”
Of course, one of the quickest ways to increasing the sustainability of the automotive industry would probably be to do away with luxury vehicles altogether and put a greater emphasis on mass transit. That would, however, hurt VW’s bottom line.
Subscribe to Our Email Newsletter
Stay up-to-date on all the latest news from the 3D printing industry and receive information and offers from third party vendors.
Print Services
Upload your 3D Models and get them printed quickly and efficiently.
You May Also Like
Consolidation in AM: How 2025 Is Shaping the Industry’s New Normal
The first half of 2025 has been marked by a clear shift in the additive manufacturing (AM) industry. Companies are no longer just focused on developing new tech by themselves....
Etsy Design Rule Change Reduces Selection of 3D Printed Goods
Online marketplace Etsy has implemented a rule change requiring all 3D printed goods on the site to be original designs. The update to the site’s Creativity Standards states, ¨Items produced using...
U.S. Congress Calls Out 3D Printing in Proposal for Commercial Reserve Manufacturing Network
Last week, the U.S. House of Representatives’ Appropriations Committee moved the FY 2026 defense bill forward to the House floor. Included in the legislation is a $131 million proposal for...
Transforming From Tourist to Native: Duro CEO Michael Corr Explains Why the Company Rebuilt its PLM Software on AI
In these early innings of the AI boom, many market analysts have expressed concern that AI spend has gotten too far ahead of the technology’s proven ability to deliver significant...