Titanium is the lifeblood of metal 3D printing. As the technology was initially driven by the aerospace and weapons sectors, it has become the metal of choice for its high strength-to-weight ratio. Now, Desktop Metal (NYSE: DM) has qualified titanium alloy Ti-6Al-4V (Ti64) for its Studio Systems 2, making it one of the first office-friendly machines capable of 3D printing with titanium. One of Desktop Metal’s first customers in the space appears to be Apple co-founder Steve Wozniak, whose new startup, Privateer Space, aims to clean up space junk.
In addition to its high strength and light weight, Ti64 is the most widely used titanium alloy for its corrosion resistance and biocompatibility. For this reason, it’s used in industries as diverse as oil and gas, automotive, and medical. Desktop Metal claims that titanium parts made with the Studio System 2 offer 730 MPa yield strength, 845 MPa ultimate tensile strength, and 17 percent elongation, properties beyond ASTM F2885-17 standards for metal injection molded surgical implants.
“Titanium has been a challenging material for bound metal 3D printing because it is both extremely reactive in powder form and difficult to sinter,” said Jonah Myerberg, co-founder and CTO of Desktop Metal. “We are excited to be the first to commercialize the most common titanium alloy, Ti64, for 3D printing through our Studio System 2 solution, opening the door to more accessible production of high-performance titanium parts.”
Among the users of the material so far is Privateer Space. Founded by Apple co-founder Steve Wozniak, the firm is dedicated to dealing with the space junk problem caused by the proliferation of satellites in space. From what this writer can tell, Desktop Metal’s press release is the first to make public any information regarding Woz’s NewSpace startup. The company is still in stealth mode and plans to make a public splash at the Advanced Maui Optical and Space Surveillance Technologies (AMOS) Conference, taking place September 14-17, 2021 in Maui, Hawaii.
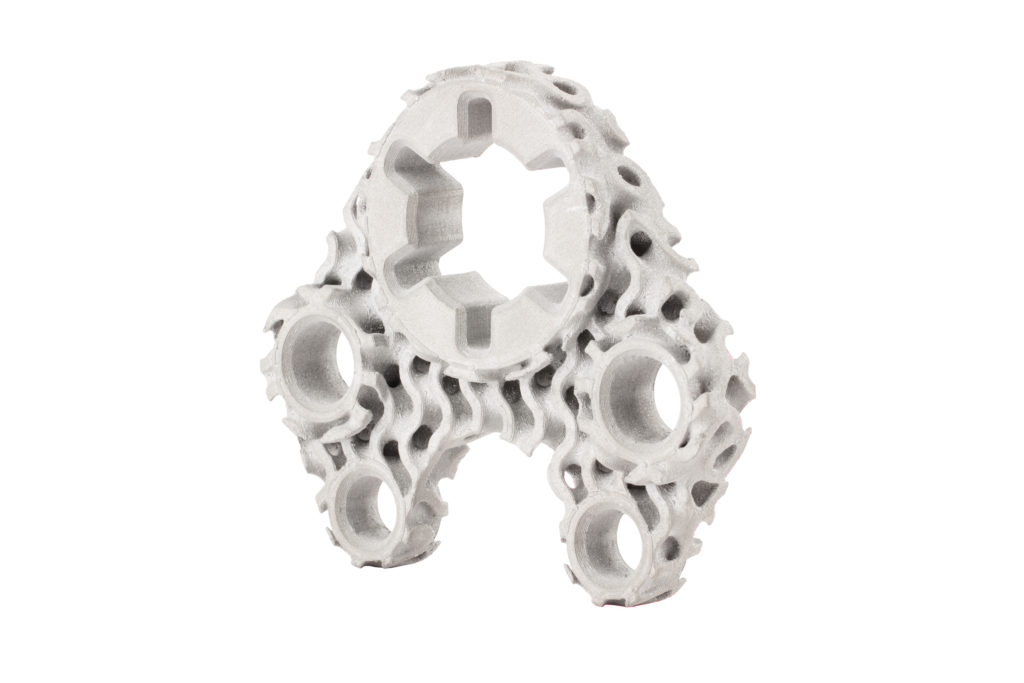
A 3D printed machine bracket made from titanium using the Studio System 2. Image courtesy of Desktop Metal.
In the press release, Wozniak explained the role that Desktop Metal’s technology will have in his startup’s mission to monitoring and cleaning up objects in space:
“3D printing with titanium is incredibly valuable in industries like aerospace because of the material’s ability to support complex and lightweight designs. With the Studio System 2, the team at Privateer Space will be able to achieve the affordability and lightweighting capabilities needed to pave the way for our satellite design and launch. This technology is truly a differentiator in helping companies to accelerate innovations in space and, through the material advancements that Desktop Metal is making, we have an amazing opportunity to collaborate and keep space accessible for future generations.”
Alex Fielding, Executive Chairman at Privateer Space, specified in a LinkedIn exactly how the firm would be using 3D printing. With Desktop Metal, the company plans to 3D print a satellite chassis that will be flown in space as soon as Q1 2022. Fielding wrote:
“I’m really thrilled to be apart of the news at Desktop Metal today around the launch of their Ti64 qualified Studio System 2. DM continues to lead the way on 3D metal printing; bringing the capabilities of fast and highly accurate additive manufacturing to space with Titanium and Privateer. Privateer had the pleasure of being a launch partner for the release and are continually impressed with the new found capabilities. Privateer and DM will have a 3D printed satellite chassis space flown in Q1 2022. Stay tuned for more to come soon!”
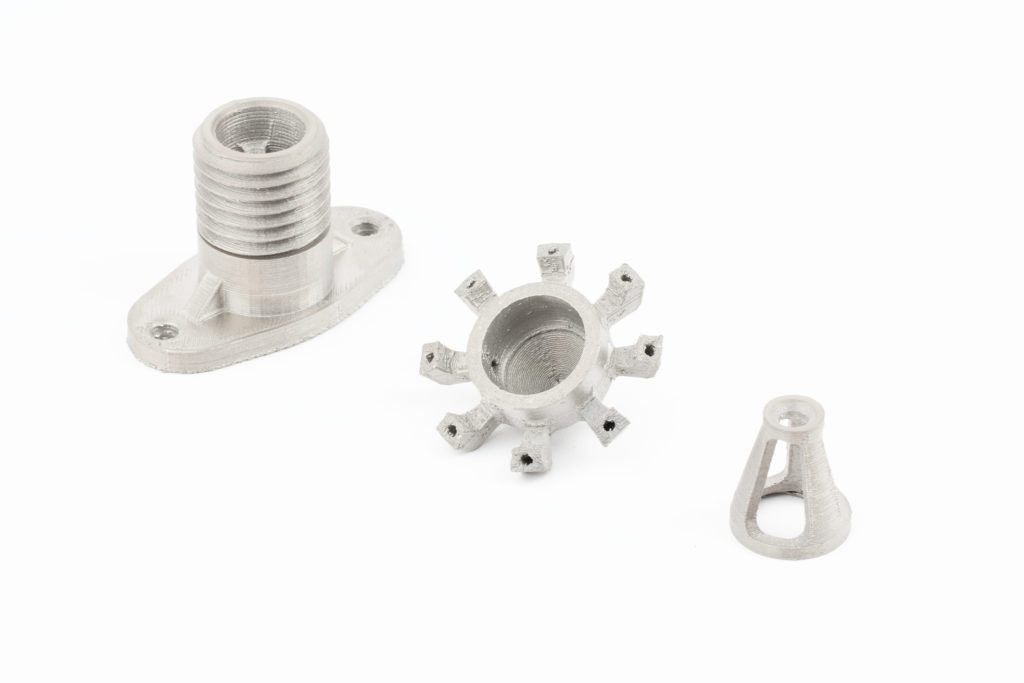
From left to right, a drone coupling, a fuel injector nozzle, and a telescope focus ring 3D printed in titanium with the Studio System 2. Image courtesy of Desktop Metal.
Desktop Metal demonstrated several applications for its new material, including a machine bracket with a gyroid lattice infill. By 3D printing the part in Ti64, the weight was cut by 59 percent. Another example was a telescope focus ring, meant to hold lenses in place on a mobile telescope. By 3D printing the part, it could be possible to use smaller motors, cutting overall cost, weight, and wear. Six focus rings could be made by the Studio System 2 in less than a day and eliminates the need for expensive tooling.
A drone coupling for linking to assemblies in a drone frame were also 3D printed. Desktop Metal highlighted the impact that weight has on drone battery life, noting that 3D printing this part could help reduce weight and extend battery life. It further pointed out that 15 to 25 drone couplings could be made per week on the Studio System 2. Desktop Metal also 3D printed a fuel injector nozzle designed with internal channels for improving burner performance. With Desktop Metal’s technology, engineers could iterate nozzle designs, 3D printing up to four versions in less than 24 hours.
In a press release, Desktop Metal claims that, once its Ti64 material begins shipping in September, it “will be the first and only company to make the material commercially available for extrusion-based bound metal additive manufacturing technologies.” This isn’t exactly true. Though the closest competitors, Markforged and ExOne/Rapidia, are still in the development stages for titanium products for their extrusion systems, The Virtual Foundry already offers a product called Ti64-5 Filamet for 3D printing. The firm’s materials can be 3D printed with just about any extrusion 3D printer. Once printed, these green objects must be debound and sintered in a standard kiln.
Unlike the aforementioned firms, however, The Virtual Foundry is not in the business of creating a tightly controlled ecosystem for its products. Though labs could experiment with its myriad metal and ceramic filaments, each material is not strictly designed to operate with a specific machine using optimized parameters. Therefore, it may be that companies like Desktop Metal, Markforged, and ExOne/Rapidia are offering products that work more directly and predictably out of the box. They additionally have the financial and business backing to potentially create a user experience that can yield useable parts much more quickly and reliably, thus earning them customers such as Privateer Space.
Interestingly, Desktop Metal, like many tech companies, seems to be echoing the Apple aesthetic, which is one of hip user-friendliness. However, Desktop Metal is so far the only one with an endorsement from the Woz.
Subscribe to Our Email Newsletter
Stay up-to-date on all the latest news from the 3D printing industry and receive information and offers from third party vendors.
Print Services
Upload your 3D Models and get them printed quickly and efficiently.
You May Also Like
Consolidation in AM: How 2025 Is Shaping the Industry’s New Normal
The first half of 2025 has been marked by a clear shift in the additive manufacturing (AM) industry. Companies are no longer just focused on developing new tech by themselves....
Etsy Design Rule Change Reduces Selection of 3D Printed Goods
Online marketplace Etsy has implemented a rule change requiring all 3D printed goods on the site to be original designs. The update to the site’s Creativity Standards states, ¨Items produced using...
U.S. Congress Calls Out 3D Printing in Proposal for Commercial Reserve Manufacturing Network
Last week, the U.S. House of Representatives’ Appropriations Committee moved the FY 2026 defense bill forward to the House floor. Included in the legislation is a $131 million proposal for...
Transforming From Tourist to Native: Duro CEO Michael Corr Explains Why the Company Rebuilt its PLM Software on AI
In these early innings of the AI boom, many market analysts have expressed concern that AI spend has gotten too far ahead of the technology’s proven ability to deliver significant...