In 2019, through the Advanced Research Projects Agency (ARPA-E), GE Research and several partners embarked on the use of metal 3D printing to produce more efficient heat exchangers. These devices, designed to efficiently transfer heat from one matter to another, are increasingly made with 3D printing nowadays due to such technological benefits as better design customization and reduced corrosion. Now, GE Research and its partners have reached a major milestone in the $3.1 million Ultra Performance Heat Exchanger (UPHEAT) project: 3D printing a heat exchanger capable of operating at temperatures of 900°C (1,652°F).
Lana Osusky, Lead Engineer at GE Research, believes that new material and design breakthroughs enabled by 3D printing are partially to thank for this achievement.
“The design freedom afforded by 3D printing processes and design tools is allowing us to more rapidly develop, build and test new heat exchanger designs that were previously not possible,” stated Osusky.
Heat exchangers perform crucial functions in our daily lives that one might not even be aware of, such as reducing the temperatures of your computer, car engine, and other assorted electronics. They’re also key to conditioning the air you breathe when on an airplane. GE and others require heat exchange devices for large-scale jet propulsion and power generation in efficient, clean ways.
A major objective of this interdisciplinary project through ARPA-E’s High Intensity Thermal Exchange through Materials and Manufacturing Processes (HITEMMP) program is to create a high-pressure, high-temperature, and super-compact heat exchanger. These devices need to handle excessive heat in order to enable cleaner, more efficient power generation in power plants and jet engines. If you can run jet engines and power turbines at hotter temperatures, you get higher efficiency levels, which also reduces costs overall.
Now, the project experts from GE Research, Oak Ridge National Laboratory (ORNL), and the University of Maryland have announced that the subscale heat exchanger they created with 3D printing has been successfully tested at temperatures more than 200°C (nearly 400°F) higher than conventional state-of-the art devices, and meets the project’s goal of 900°C (1,652°F). Not only would a heat exchanger like this help to reduce carbon emissions in large-scale power generation and flight, but it could increase efficiency as well.
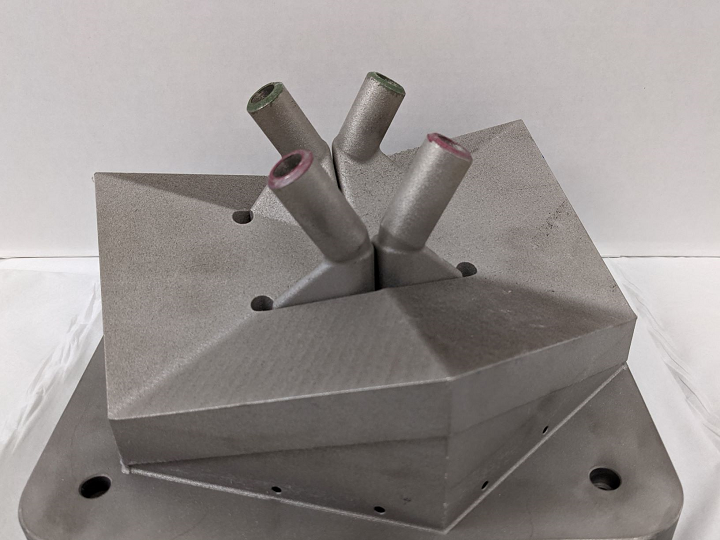
An image of a subscale 3D printed heat exchanger prototype successfully tested at temperatures close to 400°F higher than conventional devices.
What’s interesting about the final geometry is that, after the team designed, simulated, built, and tested a variety of subscale prototype devices, the selected unit resembles a cluster of grapes. This unique design was able to handle the higher temperatures and pressure that the project required, ultimately achieving nearly half the target pressure of 3,626 psi.
Osusky joked, “We may not want to eat these grapes, but we still tasted victory when we completed this key milestone.”
Actually, it’s not the heat exchanger itself that resembles grapes, but rather the design’s composition of thin-walled cells, which you can see in the video below:
Osusky said that the UPHEAT project team is on track to build and demonstrate its final 3D printed heat exchanger prototype, which is supposed to operate at full temperature and pressure—over 1,650°F and 3,600 psi—by the end of the project in Q1 2022.
(Source: GE Research)
Subscribe to Our Email Newsletter
Stay up-to-date on all the latest news from the 3D printing industry and receive information and offers from third party vendors.
Print Services
Upload your 3D Models and get them printed quickly and efficiently.
You May Also Like
Nikon SLM Solutions Sells SLM 500 to Primary Weapon Systems to Expand Suppressor Production
Primary Weapons Systems (PWS) is a Boise, Idaho-based manufacturer of suppressors, firearms, and related components. A subsidiary of Vigilant Gear and a sister company to aftermarket Glock slide manufacturer Lone...
3DPOD 261: Tooling and Cooling for AM with Jason Murphy, NXC MFG
Jason Murphy´s NXC MFG (Next Chapter Manufacturing) is not a generalist service; instead, the company specializes in making tooling. Using LPBF and binder jet, the company produces some of the...
HP and Firestorm Labs Form Partnership to Use Multi Jet Fusion 3D Printers in Deployable Factories
HP Inc., maker of a range of additive manufacturing (AM) solutions including the Multi Jet Fusion (MJF) ecosystem, has announced a partnership with Firestorm Labs, a developer of containerized, deployable...
3D Printing News Briefs, July 2, 2025: Copper Alloys, Defense Manufacturing, & More
We’re starting off with metals in today’s 3D Printing News Briefs, as Farsoon has unveiled a large-scale AM solution for copper alloys, and Meltio used its wire-laser metal solution to...