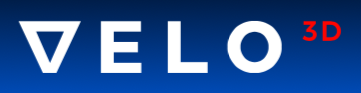
VELO3D’s Zach Murphee will be speaking at 3DPrint.com’s upcoming AMS online industry summit (Feb 9-10, 2021). Register here.
The quality of parts produced by industrial metal additive manufacturing (AM, aka 3D printing) systems has dramatically risen in recent years, to the point where certified end-use parts are now fully functional in a variety of innovative aerospace, power generation, energy and motorsport applications. Manufacturers who’ve discovered AM are producing higher-performing, often extremely complex parts within a much simpler, more efficient, workflow than traditional methods.
Not surprisingly, 3D printing equipment makers are now turning their attention to creating AM build chambers with ever-larger interior dimensions to accommodate engineers’ imaginations about how big they can go with 3D printing, both in terms of individual parts as well as batches printed in one shot.
But taller and wider builds have the potential to bring with them higher costs and associated risks. Larger systems have higher amortized costs, operational expenses (for powder, gas and other consumables) can be greater, and the risk of failure of a longer, large-part build can scale upward with a greater impact on the bottom line—or the price that must be charged to the end-customer.
Quality can also be negatively impacted with bigger build chambers: optical characteristics such as galvo mapping, spot size, and focus can be hard to dial in and maintain over a large build area. The overlay between multiple lasers can drift with time. Residual stresses can build up over a lengthy build, with flaws discovered only after the process is complete. In some systems, the amount of powder in the tool isn’t sufficient to build to the maximum Z height—necessitating pauses for refills that can cause part shifts and failures. A facility power outage or argon shortage can also lead to scrapping of a valuable, large build.
Such risks are not the same for all AM printers. VELO3D, the creator of the industry’s first SupportFree solution for 3D metal printing, announced in 2020 both the tallest metal AM build chamber (at 1 meter high) in their Sapphire 1MZ, and a larger (wider base) and higher throughput system, the Sapphire XC. From day one, VELO3D has designed all its systems with quality control metrology built into every function. The core strengths of the foundational Sapphire system—continuous build monitoring, defect detection, robust SupportFree processes, and height mapping, along with many others—are what make the newer, larger systems so reliable. On top of this, software enhancements and more lasers (in the case of the XC) have reduced build times and costs while improving productivity.
VELO3D’s 1-meter-high machine enables taller, high aspect ratio components for such applications as oilfield service tools (one customer is 3D printing an elongated well-completion part that used to be manufactured via five distinct subtractive processes), or flight hardware like full-length rocket nozzles with complex interior channels printed support-free.
VELO3D’s extra-capacity printer enables time- and cost-reducing production of whole new classes of parts, such as a jet engine combustor with 240 inducer airfoils and 17,000 shaped holes integrated into a monolithic single module. The wider build plate also brings with it over 4 times the build area for large batches of smaller parts, enabling the printing of components like multiple rocket engines at a single time.
Capabilities such as these are broadening the possibilities of AM at a larger scale, freeing engineers to explore geometry and size to the furthest extent of their imaginations—and to manufacture production parts that are competitive and successful in the industrial marketplace.
Subscribe to Our Email Newsletter
Stay up-to-date on all the latest news from the 3D printing industry and receive information and offers from third party vendors.
Print Services
Upload your 3D Models and get them printed quickly and efficiently.
You May Also Like
Nikon SLM Solutions Sells SLM 500 to Primary Weapon Systems to Expand Suppressor Production
Primary Weapons Systems (PWS) is a Boise, Idaho-based manufacturer of suppressors, firearms, and related components. A subsidiary of Vigilant Gear and a sister company to aftermarket Glock slide manufacturer Lone...
3DPOD 261: Tooling and Cooling for AM with Jason Murphy, NXC MFG
Jason Murphy´s NXC MFG (Next Chapter Manufacturing) is not a generalist service; instead, the company specializes in making tooling. Using LPBF and binder jet, the company produces some of the...
HP and Firestorm Labs Form Partnership to Use Multi Jet Fusion 3D Printers in Deployable Factories
HP Inc., maker of a range of additive manufacturing (AM) solutions including the Multi Jet Fusion (MJF) ecosystem, has announced a partnership with Firestorm Labs, a developer of containerized, deployable...
3D Printing News Briefs, July 2, 2025: Copper Alloys, Defense Manufacturing, & More
We’re starting off with metals in today’s 3D Printing News Briefs, as Farsoon has unveiled a large-scale AM solution for copper alloys, and Meltio used its wire-laser metal solution to...