As researchers from the Department of Chemistry at the University of Texas at Austin began to expand their work in applications such as tissue engineering and soft robotics, they realized a need to explore photochemistry further to develop “novel panchromatic photopolymer resins” for better speed and higher resolution in printing. The current speed they were working with was not realistic for the types of composites, complex structures, or hydrogels that they were seeking to create, due to complicated electron transfer, slow curing times, and high irradiation intensity.

Presented method and opportunities offered by visible light photocuring for 3D printing. Illustration shows the general mechanism for digital light processing (DLP), with exchangeable light emitting diodes (LEDs). For UV and visible light photocuring, a green check mark indicates an attractive feature, while a red “X” represents a current challenge.
Resins were created in violet, blue, green, and red, containing the following:
- Monomer
- Photoredox catalyst (PRC)
- Two co-initiators
- Opaquing agent
The researchers relied on the PRC to promote electron transfers and consequent production of radicals, resulting in polymerization. Resolution was improved as the opaquing agent (a passive absorber) improved curing in their digital light processing (DLP) system with visible LEDs. Explaining their work in “Rapid High-Resolution Visible Light 3D Printing,” authors Dowon Ahn, Lynn M. Stevens, Kevin Zhou, and Zachariah A. Page showed that they were able to double the number of radicals produced for each photon being absorbed.
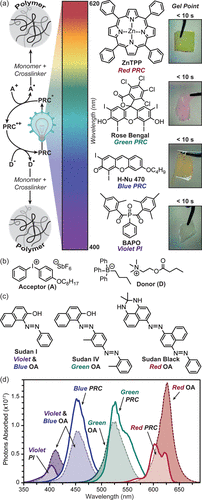
Visible light curing. (a) General mechanism (oxidative quenching) for a three-component system (left). Chemical structures of photoinitiator (PI) and photoredox catalysts (PRCs), and corresponding pictures of photocured films with qualitative gel times (right). (b) Chemical structures of iodonium acceptor (A) and borate donor (D) coinitiators. (c) Chemical structures of opaquing agents (OAs). (d) Photons absorbed vs wavelength for PI and PRC compounds at optimal photocuring concentration, and OA at 0.5 mM (red) and 1 mM (green, blue, and violet). Light exposure was from calibrated violet (405 nm), blue (460 nm), green (525 nm), and red (615 nm) LEDs at the DLP 3D printer image plane.
Printing with a layer thickness of 100 μm, the researchers had better results in evaluating the quality of resolution and mechanical properties. Better speed occurred with thicker layers, and their new “resolution print” was successful in offering better efficiency, speed, and resolution due to improved control in exposure time for each layer.
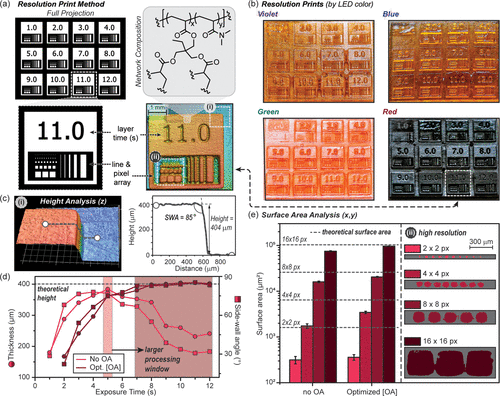
3D print optimization protocol using the “resolution print” method. (a) Digital projection layer at one second when all squares are illuminated simultaneously (white regions correspond to exposure) (top left). Expanded square for 11 s exposure/layer showing the line and pixel array for the projection (bottom left) and red light resolution print taken with optical profilometry (bottom right). Chemical composition for photocured stiff resin comprising dimethyl acrylamide and trimethylolpropane triacrylate (top right). (b) Optical images of prints from the four resins by exposure color (100 μm layers, 4 layers for each numbered square on top of 12 base layers). (c) z-resolution analysis: 3D image of a corner on the 11 s square outlined as box i in the profilometry image above in part a. Height and sidewall angle (SWA) were determined using an average of 10 line traces per corner (with one shown for reference). (d) Graph of thickness and SWA vs exposure time for the red resin. The light and dark red shaded regions represent exposure times (or processing windows) to provide optimal z-resolution without OA and with optimized [OA], respectively (theoretical height = 400 μm). (e) x-, y-resolution analysis: Plot of surface areas measured for 16, 8, 4, and 2 pixel wide squares using optical profilometry. Surface areas are averages from 3, 5, 8, and 10 squares for the 2, 4, 8, and 16 pixel wide features, respectively (error represents ±1 standard deviation). Dashed lines represent theoretical surface areas, and error bars represent ±1 standard deviation, showing how OA enhances print fidelity and reproducibility of features below 100 μm in length.
“Tensile testing revealed an E = 0.8 ± 0.1 MPa, which is 3 orders of magnitude lower than those from the stiff resin. Moreover, swelling tests in water for six cubes printed with either stiff or soft resin qualitatively highlight the difference in chemical makeup,” stated the authors.
“The soft cubes had a much larger water uptake (177 ± 1% increase in weight) compared to the stiff resin (54 ± 2% increase in weight), which is attributed to a combination of lower cross-link density and increased hydrophilicity of the alcohol-laden soft network.”
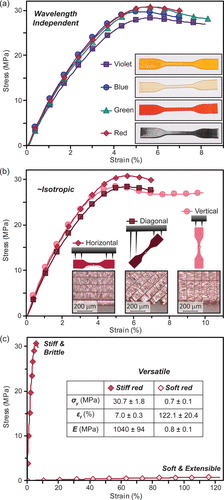
Mechanical testing of 3D printed dogbones. (a) Stress–strain curves of violet, blue, green, and red dogbones showing wavelength independent properties. (b) Red dogbones printed at three different edge-on angles (horizontal, diagonal, and vertical), demonstrating near isotropic mechanical properties. Insets are drawings of each dogbone orientation, with supports to the build platform shown, and close up images to visualize each layer. (c) Stress–strain curves of stiff and elastic red resin. The inset shows a table highlighting the disparate mechanical properties, and associated versatility of the platform.
Along with the production of a octet truss that demonstrated complexity and functionality, the researchers concluded that mechanical and chemical properties have potential due to their versatility, and ability for using a wide range of materials in the future without involving “harmful UV light.”

Hierarchical octet truss as a complex 3D print demonstration. (a) Digital rendering. (b) Photograph of the printed object using the stiff red resin composition and red light exposure (∼2.1 mW/cm2) for 8 s/25 μm layer. (c, d) Scanning electron microscope images at different magnifications showing the structural hierarchy.
Subscribe to Our Email Newsletter
Stay up-to-date on all the latest news from the 3D printing industry and receive information and offers from third party vendors.
Print Services
Upload your 3D Models and get them printed quickly and efficiently.
You May Also Like
Consolidation in AM: How 2025 Is Shaping the Industry’s New Normal
The first half of 2025 has been marked by a clear shift in the additive manufacturing (AM) industry. Companies are no longer just focused on developing new tech by themselves....
Etsy Design Rule Change Reduces Selection of 3D Printed Goods
Online marketplace Etsy has implemented a rule change requiring all 3D printed goods on the site to be original designs. The update to the site’s Creativity Standards states, ¨Items produced using...
U.S. Congress Calls Out 3D Printing in Proposal for Commercial Reserve Manufacturing Network
Last week, the U.S. House of Representatives’ Appropriations Committee moved the FY 2026 defense bill forward to the House floor. Included in the legislation is a $131 million proposal for...
Transforming From Tourist to Native: Duro CEO Michael Corr Explains Why the Company Rebuilt its PLM Software on AI
In these early innings of the AI boom, many market analysts have expressed concern that AI spend has gotten too far ahead of the technology’s proven ability to deliver significant...