The concept of distributed manufacturing, which we’ve covered numerous times, could play an interesting role in a climate-disrupted world. Just as large swaths of a centralized electrical grid can suddenly go out during a storm, a globalized supply chain reliant on centralized production facilities can easily be impacted by major events.
This is something we are currently witnessing with the COVID-19 pandemic, but our unfolding ecological collapse will see many devastating events potentially wreak havoc on the way we produce and ship goods. Not only will individual (and compounding) extreme weather events cause issues with various production centers around the world, but global warming is projected to increase the rate of epidemics, such as cholera, malaria, dengue fever, chikungunya, and West Nile virus. It is already thought to be responsible for increases in Lyme disease.
Regardless of the exact cause of supply chain disruptions, it’s apparent that the globalized nature of manufacturing has major drawbacks that could potentially benefit from distributed manufacturing. As it currently stands, a factory on one part of the planet will mass produce huge numbers of a specific component, ship to them another facility where is is assembled with other pieces into a final product that is shipped by road, sea and air to a warehouse that maintains a steady stock of these goods to send off to brick and mortar or online retailers or Amazon distribution centers to wind up in the hands of the end user.
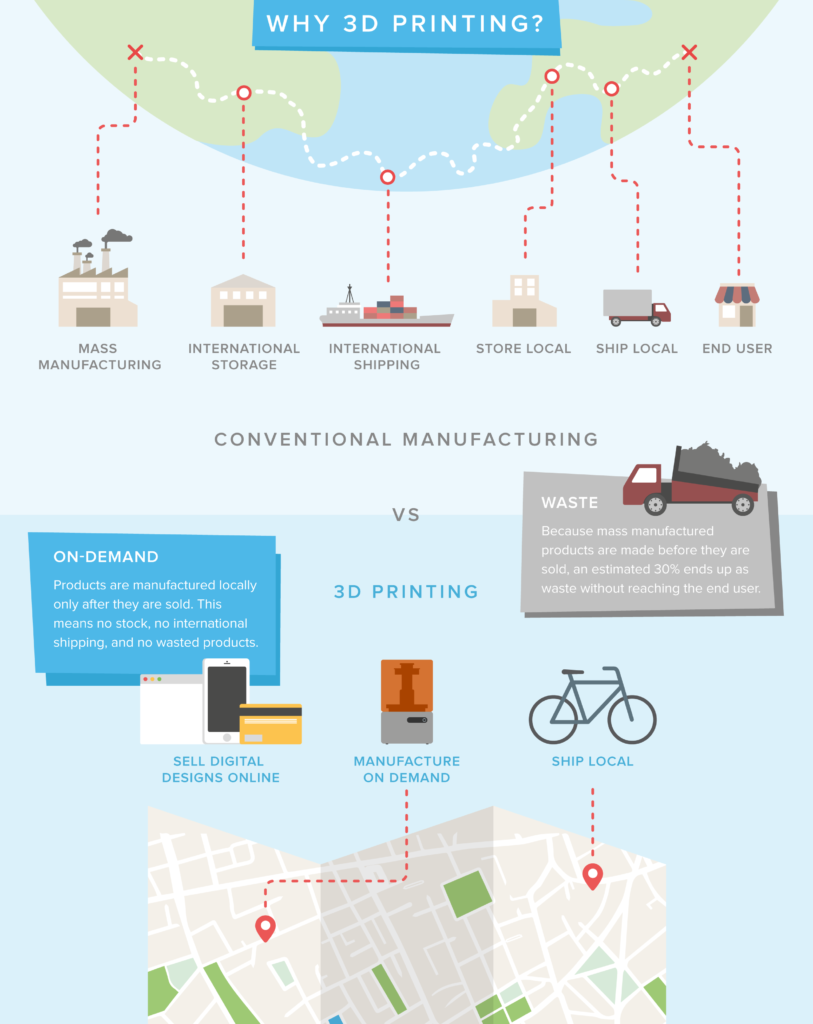
A graphic from a 3D Hubs blog post about distributed vs centralized manufacturing. Image courtesy of 3D Hubs.
The point of distributed manufacturing is that AM and other digital fabrication technologies will make it possible to produce parts close to their point of use. This model of decentralized production usually involves either a network of geographically disparate manufacturing sites all connected using various IT tools or production performed locally based on the cottage industry model.
In an ideal world, entire items could be 3D printed locally for their users. In such a world, this method of production could potentially reduce or eliminate physical stock. Instead of maintaining warehouses filled with items whose supplies are determined by rough annual estimates of demand, businesses could maintain digital inventories and make goods on-demand.
Not only would this prevent major disruptions in the supply chain, but it would greatly reduce greenhouse gas (GHG) emissions. According to a 2015 study, aviation and maritime shipping represent three to four percent of global GHG emissions. That number is expected to hit 17 percent by 2050, based on our current trajectory. The Air and Waste Management Association estimated emissions for heavy truck, rail and water transport to represent 25 percent of CO2 emissions for the U.S. and 30 percent of Europe in 2007.
Currently, AM is not capable of making complete, complex end-products, but producing end parts is increasingly viable. Therefore, we are still reliant on aspects of the existing, globalized manufacturing and supply model. Existing models of distributed manufacturing use a network of global service bureaus to produce parts in locations near to their end users.
3D Hubs and similar companies helped to popularize the concept of distributed manufacturing by providing a central website for accessing the services of 3D printer users worldwide. Originally, the vast majority of 3D Hubs users were owners of desktop material extrusion machines and the startup would continually give updates as to how many printer users were on their site, in what cities around the world, with what materials and what printers. In some ways, this seemed to suggest the technological possibility of the latter cottage industry-style of distributed manufacturing mentioned above.
However, after the consumer 3D printing bubble of 2014, desktop 3D printing was no longer seen as the revenue opportunity for investors and manufacturers that it once was. In turn, businesses that previously emphasized low-cost technology for consumer use shifted toward more industrial machines. This included 3D Hubs, which still networks an array of AM service providers, but no longer focuses on low-cost material extrusion. Alongside industrial AM services, the startup now also offers CNC machining, injection molding, and sheet metal fabrication, making 3D Hubs more akin to other manufacturing service providers in the space, like Proto Labs, Xometry, Stratasys Direct Manufacturing, and 3D Systems On Demand.
As a result, of the two distributed manufacturing concepts described above, the more high-tech version has come to dominate the AM industry ideologically. 3D Hubs’ service providers are no longer easily visible, but there isn’t much doubt that they are globally distributed. Xometry, too, offers fabrication services through a dispersed network of providers. In both cases, these providers are engineering firms and manufacturing outfits, with Xometry and 3D Hubs developing increasingly sophisticated software for ensuring the viability of designs, determining costs, selecting materials and production options and more.
Those are firms that have based their entire business models off of distributed manufacturing; the success of larger names trying to implement similar concepts is harder to grasp They all have their own names and seem to be discrete, but HP, Jabil, Siemens and SAP all appear to be a part of the same distributed additive network. HP has a growing number of service bureau customers who use Multi Jet Fusion to make parts for clients and Jabil performs contract manufacturing, but it is unclear the extent that these overlapping networks have been realized. SAP, for instance, has not provided an update to its distributed AM program since 2018.
Distributed manufacturing will continue to evolve so that, during future disruptions, it may be used to help work around bottlenecks in the supply chain. This will, of course, be essential for manufacturing items that may be in short supply during a time of crisis. The further development of high-tech distributed manufacturing technology, however, doesn’t preclude a return to the older cottage-based model of local production. We can envision that, as AM advances, it may be possible for local service bureaus to manufacture goods locally alongside small businesses.
Subscribe to Our Email Newsletter
Stay up-to-date on all the latest news from the 3D printing industry and receive information and offers from third party vendors.
Print Services
Upload your 3D Models and get them printed quickly and efficiently.
You May Also Like
Consolidation in AM: How 2025 Is Shaping the Industry’s New Normal
The first half of 2025 has been marked by a clear shift in the additive manufacturing (AM) industry. Companies are no longer just focused on developing new tech by themselves....
Etsy Design Rule Change Reduces Selection of 3D Printed Goods
Online marketplace Etsy has implemented a rule change requiring all 3D printed goods on the site to be original designs. The update to the site’s Creativity Standards states, ¨Items produced using...
U.S. Congress Calls Out 3D Printing in Proposal for Commercial Reserve Manufacturing Network
Last week, the U.S. House of Representatives’ Appropriations Committee moved the FY 2026 defense bill forward to the House floor. Included in the legislation is a $131 million proposal for...
Transforming From Tourist to Native: Duro CEO Michael Corr Explains Why the Company Rebuilt its PLM Software on AI
In these early innings of the AI boom, many market analysts have expressed concern that AI spend has gotten too far ahead of the technology’s proven ability to deliver significant...