Kentucky’s Somerset Community College 3D Prints in Metal on Modified FDM 3D Printers that Cost $600 Each
While 3D printing, 4D printing, bioprinting, and additive manufacturing processes abound in the US and around the globe, some programs are not previously as well-known but are also real powerhouses of digital fabrication. Offering two main campuses and four centers, the Kentucky-based Somerset Community College has just announced that their additive manufacturing program has completed the successful 3D printing of numerous 316L stainless steel metal parts on multiple desktop 3D printers that cost only $600.
Bringing affordability and accessibility to their student base in an extraordinary way, the SCC AM faculty and staff began the program with several FDM 3D printers costing less than $450 each. They continued with customizations, including upgrading the machines to accommodate metal filament extrusion (with metal infused filaments provided by Virtual Foundry and BASF). They also modified the 3D printers for improved build plate adhesion. While normal issues such as shrinkage had to be accounted for, parts were soon 3D printed.

Stainless steel parts produced on a desktop 3D printer, with the back left and right plates having been welded together after printing
“This project is one of the first applications where fully metal parts that were 3D printed on a sub $600 desktop printer have been successfully welded together using conventional welding techniques,” stated the SCC team in their recent press release sent to 3DPrint.com. “SCC’s process is based on Bound Metal Additive Manufacturing (BMAM), predicted by researchers to be one of the fastest growing methods of additive production over the next several years.”
SCC sought help for the de-binding and sintering process, working with DSH Technologies. In the final phase of production and post processing, senior Welding Professor, Karl Watson of the SCC Welding Department, and his team ‘worked their magic’ using gas tungsten arc welding (GTAW) on six samples, adding fillet and groove welds.
Watson noted that the finished parts have not shown any inconsistencies despite some tests showing hardness values slightly less than stock 316L. Welding of stainless materials also yielded higher levels of heat dissipation than normal.
“The welds flowed very smoothly and we had very good penetration control,” said Watson. “Because of the nature of 3D printing and research we have seen around the concept of welding such parts, I expected to see more porosity in the weld, but that wasn’t the case with these specimens at all. I am looking forward to doing some bend tests to determine the potential malleability as well as welding other samples using SMAW, GMAW, and FCAW.”
On the heels of this successful project, SCC states that their goal now is to offer 3D printing technology with metal to both schools and the workforce throughout Kentucky. SCC plans to provide workshops, as well as offering setup of 3D printing equipment for ‘select educators’ in high schools and other community colleges, all funded by the Kentucky National Science Foundation (NSF) EPSCoR (or Established Program to Stimulate Competitive Research) grant, titled Kentucky Advanced Partnership for Enhanced Robotics and Structures.
SCC will also be partnering with Autodesk to provide training in advanced AM design processes, integrating the use of Fusion 360’s Generative Design suite. They will also partner with both the University of Louisville and the University of Kentucky for introducing low-cost BMAM skills, with the Tennessee Technological University (TTU) for assistance in working over state lines, and then they will be choosing training sites for instructors to educate interested members of the Kentucky workforce.
“We are so very grateful for all of the funding and support we have received from the NSF, USDA Rural Business Development, Southeastern Kentucky Economic Development (SKED), the Office of Career and Technical Education and Student Transition at the Kentucky Department of Education, and the Kentucky Highlands Investment Corporation, as well as the support from local businesses that fully understand the disruptive power of additive,” says Eric Wooldridge, Director of SCC’s Additive Manufacturing program. “Being able to bring truly low cost metal 3D printing and advanced product design directly to schools and colleges across Kentucky is a chance of a lifetime opportunity for us, and we are very excited to get started.
“There is a lot for us to learn about practical welding of 3D printed metal parts, especially parts that have been produced on a desktop 3D printer. Factors of shrinkage, potential zones of weakness, and the best welding practices are still to be determined. These are very exciting but uncharted waters to be sure,” continued Wooldridge.
The ultimate goal of SCC is to see that individuals working in AM processes with metal and polymers find it to be ‘the norm and not the exception.’ Their plan is extensive, meant to establish programs in schools, and then they will seek added funding to begin working with businesses and entrepreneurs.
“When you look at all the big investments in additive manufacturing by the aerospace and automotive industries, the announcements from the Department of Defense, and the number of products already on the market that are produced using 3D printing technology,” says Wooldridge, “practical skills in this technology are what any advanced workforce needs. Having a state-wide workforce that is capable of 3D printing metal parts at a fraction of the typical cost; that’s just an innovation revolution waiting to happen.”
Find out more about SCC’s Additive Manufacturing program here or check out their YouTube channel, The Additive Guru. Somerset Community College is a comprehensive two-year institution of higher education. SCC has campuses in Somerset and London, and centers in Clinton, McCreary, Casey, and Russell counties.
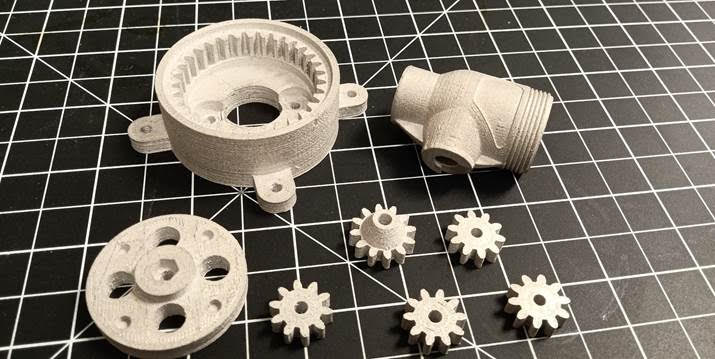
Close up of several stainless steel 3D printed parts, including a ball valve housing and a planetary gear assembly
Schools at all levels today are engrossed in teaching 3D printing and AM processes to their students, and many young innovators are soaring to new levels with their imaginations as they enjoy workshops, learn to bioprint, and even create visual aids for their own classes. What do you think of this news? Let us know your thoughts; join the discussion of this and other 3D printing topics at 3DPrintBoard.com.
[Source / Images: Somerset Community College]Subscribe to Our Email Newsletter
Stay up-to-date on all the latest news from the 3D printing industry and receive information and offers from third party vendors.
Print Services
Upload your 3D Models and get them printed quickly and efficiently.
You May Also Like
Consolidation in AM: How 2025 Is Shaping the Industry’s New Normal
The first half of 2025 has been marked by a clear shift in the additive manufacturing (AM) industry. Companies are no longer just focused on developing new tech by themselves....
Etsy Design Rule Change Reduces Selection of 3D Printed Goods
Online marketplace Etsy has implemented a rule change requiring all 3D printed goods on the site to be original designs. The update to the site’s Creativity Standards states, ¨Items produced using...
U.S. Congress Calls Out 3D Printing in Proposal for Commercial Reserve Manufacturing Network
Last week, the U.S. House of Representatives’ Appropriations Committee moved the FY 2026 defense bill forward to the House floor. Included in the legislation is a $131 million proposal for...
Transforming From Tourist to Native: Duro CEO Michael Corr Explains Why the Company Rebuilt its PLM Software on AI
In these early innings of the AI boom, many market analysts have expressed concern that AI spend has gotten too far ahead of the technology’s proven ability to deliver significant...