While dark-field acoustics may sound mysterious, they pertain to imaging capabilities that are helpful to researchers in a wide range of applications. In ‘A versatile dark-field acoustic-resolution photoacoustic microscopy system aided by 3D printing,’ authors Chenyao Wen, Lingyi Zhao, Tao Han, Wenzhao Li, Guangjie Zhang, and Changhui Li–all from Peking University in Beijing–are using new techniques to create a stronger, more flexible photoacoustic microscopy system.
Photoacoustic imaging relies on pulses and pressure, ultimately, to target specific images; for instance, PAT systems are popular for use by researchers involved in biomedical imaging for life science and clinical diagnosis. AR-PAM systems are even more popular for use by scientists, offering a more streamlined approach in comparison to more complex PAT systems, along with benefits such as less reconstruction artifacts, greater sensitivity, and more affordability in use.
“Until now, AR-PAM systems with different types of transducers (frequency range covering from 5 MHz to 50 MHz) have been successfully used in imaging various biological tissues, including skin, the brain, the intestine, eyes, and the abdomen of rats.”
Dark-field systems use a ‘donut-shaped’ dark-field illumination that is positioned underneath an ultrasonic transducer and can be used to eliminate undesired photoacoustic signals, while allowing PA waves; however, due to the opaque quality of the ultrasonic transducer, a customized optical condenser must be employed.
The authors point out that while previous labs have created different types of condensers—including those using internal reflection and mirror reflection—such choices are not always suitable for lab use. Here, the researchers developed a new system with inexpensive 3D printed parts and a fiber bundle for optical coupling and delivery. The new system also means that the angle of illumination is tunable, and transducers are easily replaced.
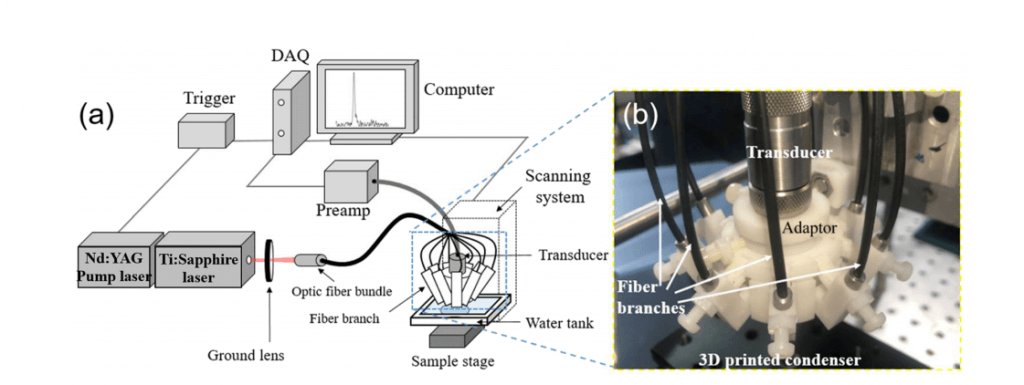
(a) The schematic of the AR-PAM system. (b) Photograph of the 3D printed optical condenser with the transducer.
“A tunable Ti:sapphire pulsed laser (LT-2211A, LOTIS TII, Minsk, Belarus) pumped by a Q-switched Nd:YAG pump laser (LS-2137/2, LOTIS TII, Minsk, Belarus) served as the illumination source, which has a repetition rate of 10 Hz and a pulse width of 16-ns. The 800 nm near-infrared (NIR) laser was generated by the pulsed Ti:sapphire laser. The fiber bundle consists of a total of 5670 multimode glass fibers (core diameter, 50 μm; NA, 0.62) with one combined terminal end (diameter, 5 mm) for laser input and nine equal branching terminal ends (diameter, 1.5 mm) for laser output,” explained the authors.
Rather than offering just a single multimode fiber, the researchers sought more power with a fiber bundle, consisting of fibers ‘randomized into nine branches.’ Each terminal was mounted around the 3D printed condenser, composed of 3D printed adjustable joints, with an ultrasonic transducer in the center.
The 3D printed condenser consists of the following:
- Fiber holder
- Transducer adaptor
- Interconnecting pieces
- Angle-adjust ring
- Main body
The design of the condenser and the 3D printed adaptors also allowed the researchers to fit in transducers of different sizes. What is even more impressive, however, is that the overall cost to 3D print the condenser was $10 USD, with assembly completed in one hour.
“Only a few metal nuts were glued onto the condenser since 3D printing is unable to print robust fine screw threads in resin material. The 3D printing files and fiber design are available for free upon request,” explained the researchers.
For both simulation and phantom experiments, the researchers used the following measurements:
- Illumination angle of 30 degrees
- Outer diameter and inner diameter of the donut – 20mm and 12mm, respectively
- Illumination patterns of fiber bundles – a circle with a diameter of 4mm
- Inner diameter of nine circles set at 12mm

Scheme of the 3D printed condenser and the mechanism of changing the illumination angle. (a)Structural scheme of the condenser. TA, transducer adaptor; ADR, angle adjust ring; FH, fiber holder; ICP, interconnecting pieces. Multimedia view: https://doi.org/10.1063/1.5094862.1 (b) Sectional view of the holder; angle θ (marked as a green curve) between the sensor and the fiber changes following the vertical movement of the ADR, which is marked as a red twin arrow. (c) Photograph of illuminated donut patterns at three different angles of 20○, 30○, and 45○.
During simulation, the researchers realized that depth had a major impact on power of the system and specifically, optical fluence between the fiber bundle and the donut illumination.
“Although the fiber bundle has a much larger terminal for laser coupling, the coupling efficiency is generally less than that of a single multimode fiber,” concluded the researchers. “It is because there exist interfiber spaces that waste part of the illuminating laser. An alternative way is to use the so-called ‘Fused End Bundles’ by CeramOptec®, which could help increase the coupling efficiency.
“ … the current system is more suitable for relative low frequency transducers that need smaller illumination angles. Since the 3D printing optical lens also becomes popular, we will explore methods to converge the output laser via gluing a printed lens on top of the branching fiber bundle terminal in future work.”
While scientists around the globe are engaged in spectacular research projects regarding bioprinting, new additive manufacturing processes, industrial design, and so much more, scientists are also able to create a wide range of tools to help complete many different studies—some replacing common components made by conventional methods, and others that could not have been possible otherwise.
What do you think of this news? Let us know your thoughts! Join the discussion of this and other 3D printing topics at 3DPrintBoard.com.

The schematic of two different illumination conditions: the traditional dark-field reflection mode (left) and the fiber illuminating mode (right).
Subscribe to Our Email Newsletter
Stay up-to-date on all the latest news from the 3D printing industry and receive information and offers from third party vendors.
Print Services
Upload your 3D Models and get them printed quickly and efficiently.
You May Also Like
Nikon SLM Solutions Sells SLM 500 to Primary Weapon Systems to Expand Suppressor Production
Primary Weapons Systems (PWS) is a Boise, Idaho-based manufacturer of suppressors, firearms, and related components. A subsidiary of Vigilant Gear and a sister company to aftermarket Glock slide manufacturer Lone...
3DPOD 261: Tooling and Cooling for AM with Jason Murphy, NXC MFG
Jason Murphy´s NXC MFG (Next Chapter Manufacturing) is not a generalist service; instead, the company specializes in making tooling. Using LPBF and binder jet, the company produces some of the...
HP and Firestorm Labs Form Partnership to Use Multi Jet Fusion 3D Printers in Deployable Factories
HP Inc., maker of a range of additive manufacturing (AM) solutions including the Multi Jet Fusion (MJF) ecosystem, has announced a partnership with Firestorm Labs, a developer of containerized, deployable...
3D Printing News Briefs, July 2, 2025: Copper Alloys, Defense Manufacturing, & More
We’re starting off with metals in today’s 3D Printing News Briefs, as Farsoon has unveiled a large-scale AM solution for copper alloys, and Meltio used its wire-laser metal solution to...