If you have ever experienced a major illness or serious injury, most likely you were extremely thankful for the medical professionals who helped you get your life back; however, it can be both distressing and frustrating—not to mention life-threatening—when doctors or nurses make mistakes that could have grave consequences. US researchers want to make even greater strides to improve safety mechanisms in both storing and preparing of anesthetic medications, outlined in the recently published ‘Anesthesia Workspace Cleanliness and Safety: Implementation of a Novel Syringe Bracket Using 3D Printing Techniques.’
There may be standards in place, and processes for avoiding syringe contamination and medication swaps, but as the authors point out, ‘wide variability’ persists. This is concerning—and dangerous for patients with all too common errors like:
- Delayed responses to critical changes in patient status
- Syringe swaps
- Environmental contamination of syringes
- Cross-contamination of syringes between patients
Even with new standardizations like prefilled syringes and automated labeling, there are errors—enough to present ‘widespread challenges.’ The problem is so bad that data shows one in fifteen syringes to be contaminated with ‘potentially pathogenic bacteria.’

Prototype syringe bracket with removable support structures printed with a desktop stereolithography 3D printer
“A growing body of evidence had linked postoperative healthcare-associated infections to such microorganisms within the anesthesia workspace, prompting the recent release of the Society for Healthcare Epidemiology of America’s first infection prevention guidelines for the anesthesia work area,” state the researchers.
In seeking solutions for a better quality of care for patients, the research team considered ways to improve the following:
- Handling
- Availability
- Standardization of key medications in the anesthesia workspace
After studying common causes of such mishaps, the research team came to a very important conclusion: rather than just delivering mandates to medical personnel regarding their need to change their behaviors, the whole system needs to be re-engineered—with better tools and better organization to prevent errors.
The project, a ‘quality improvement initiative,’ was completed at Massachusetts General Hospital, as the researchers assessed a baseline in terms of routine practices, developed a device for better organization, and then evaluated provider practices. They used 3D printing to create an organizational device for better safety and efficiency overall. So far, the researchers have tested and used the new 3D printed device in 60 operating rooms at one medical facility with ongoing postintervention surveys and workspace audits a year later.
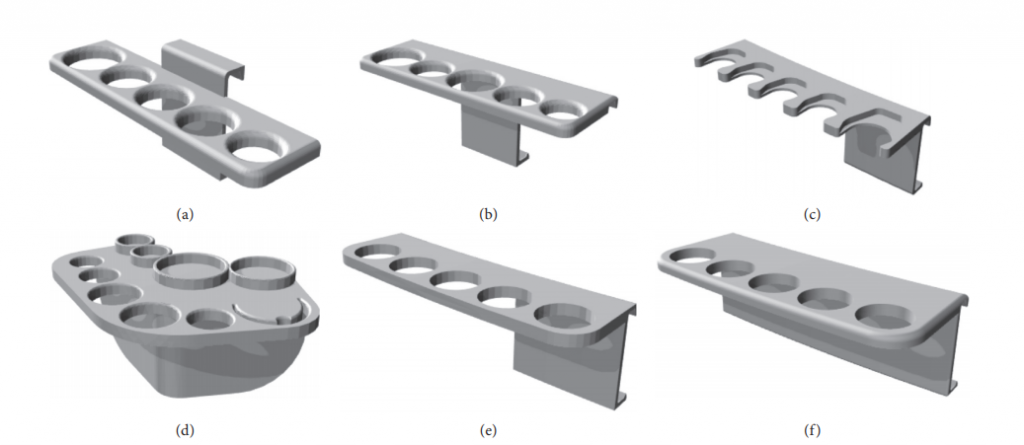
Serial syringe bracket designs based on iterative prototyping and user feedback: (a) initial prototype, (b) elevation of main surface to provide further clearance from anesthesia machine display, (c) alternative slot configuration using flange to hold syringe and allow front loading and unloading, (d) corner-mounted design including holders for unopened medication vials and a bougie, (e) anterior extension of the main surface to provide further clearance from machines with mounted depth of anesthesia monitors, (f ) final design with wider support clip for increased stability. A detailed review of the rationale and utility of each of these design features is provided in Supplementary Table 2.
Their 3D printable syringe bracket system is open-source, operating as a cognitive aid and a way to prevent contamination. Prototypes were created on a Formlabs Form 2, in a series of customized brackets meant to be attached to the anesthesia machine. The goal is for the syringe bracket to reduce ‘transmission events’ by preventing environmental contamination—and offering a way to clearly distinguish emergency medications from those already accessed for another patient. The researchers also developed a ‘one-way’ system for syringes to be accessed only one time and then never placed back in the bracket.
Surveys indicated ‘significantly higher levels of confidence’ in knowing there was a more secure process in place; in fact, 76.2 percent of respondents reported more than 95 percent confidence in knowing where medications where ‘during supervision or handoffs,’ as opposed to the original baseline of 43.7 percent.
“One year after deployment, 94% of users reported that they found the device to be helpful, 96.3% expressed a desire to have the brackets expanded to nonoperating room anesthetizing locations, and 96.2% would like to have them in other hospitals where they may work at present or in the future,” concluded the researchers.
“Measures of practitioner adoption and satisfaction with the device one year after implementation suggest that this intervention resulted in a high-value, meaningful culture change and may yield similar improvements outside of our own institution.”
While 3D printing has made huge impacts within bioprinting and the creation of devices and implants directly affecting patients—offering a better quality of life—this technology has also been responsible for a variety of different models and mechanisms that allow for improved, more efficient processes in hospitals. Find out more about the new syringe bracket here. What do you think of this news? Let us know your thoughts! Join the discussion of this and other 3D printing topics at 3DPrintBoard.com.

Final selective laser-sintering 3D-printed bracket and accompanying bougie holder in use. ‘e bracket clips securely to the corner of the anesthesia machine and accepts five 10–20 mL BD syringes (standard setup including phenylephrine, ephedrine, glycopyrrolate, succinylcholine, and propofol shown).
Subscribe to Our Email Newsletter
Stay up-to-date on all the latest news from the 3D printing industry and receive information and offers from third party vendors.
Print Services
Upload your 3D Models and get them printed quickly and efficiently.
You May Also Like
Nikon SLM Solutions Sells SLM 500 to Primary Weapon Systems to Expand Suppressor Production
Primary Weapons Systems (PWS) is a Boise, Idaho-based manufacturer of suppressors, firearms, and related components. A subsidiary of Vigilant Gear and a sister company to aftermarket Glock slide manufacturer Lone...
3DPOD 261: Tooling and Cooling for AM with Jason Murphy, NXC MFG
Jason Murphy´s NXC MFG (Next Chapter Manufacturing) is not a generalist service; instead, the company specializes in making tooling. Using LPBF and binder jet, the company produces some of the...
HP and Firestorm Labs Form Partnership to Use Multi Jet Fusion 3D Printers in Deployable Factories
HP Inc., maker of a range of additive manufacturing (AM) solutions including the Multi Jet Fusion (MJF) ecosystem, has announced a partnership with Firestorm Labs, a developer of containerized, deployable...
3D Printing News Briefs, July 2, 2025: Copper Alloys, Defense Manufacturing, & More
We’re starting off with metals in today’s 3D Printing News Briefs, as Farsoon has unveiled a large-scale AM solution for copper alloys, and Meltio used its wire-laser metal solution to...