In ‘Effect of Ultrasonic Vibration on Interlayer Adhesion in Fused Filament Fabrication 3D Printed ABS,’ by Alireza Tofangchi, Pu Han, Julio Izquierdo, Adithya Iyengar and Keng Hsu, the authors examine the future of FFF (FDM, Material Extrusion) 3D printing, along with how different processes affect performance. They foresee greater potential for FFF printing as a serious tool in manufacturing, as materials, accuracy, finishing, and quality in parts begin to evolve.
With the use of 34.4 kHz ultrasonic vibrations during FFF 3D printing, the researchers found up to a 10 percent increase in ABS layer adhesion versus regular FFF processes.
“This increase in the interlayer adhesion strength is attributed to the increase in polymer reptation due to ultrasonic vibration-induced relaxation of the polymer chains from secondary interactions in the interface regions,” state the research team, hailing from the Department of Mechanical Engineering, University of Louisville.
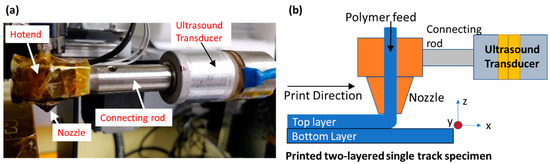
Laboratory-implemented apparatus for incorporating ultrasonic vibrations into Fused Filament Fabrication (FFF)-deposition of thermoplastic polymer. (a) photogragh of actual apparatus. (b) Conceptual sketch.
The team explains that there have been several different methods used for strengthening interlayer bonding; for example, adding more heat during or after printing has proven to be effective through elevating the ‘temperature dependent diffusivity.’ Enhancing the surface of filaments also proved to improve strength, along with both infrared and laser heating—added just before deposition of each layer. The researchers also noted that ‘reducing the radius of gyration of polymer chains could also result in similar improvement in inter-layer strength,’ effected through relaxing the polymer chains left in the 3D printed tracks.
Ultrasound vibrations permit both relaxation and diffusion of polymers, creating better interfacial adhesion—and possibly resulting in parts bearing isotropic mechanical properties. Testing occurred on a MakerGear M3 that the team customized for the inclusion of the vibrations. Vibrations were created with a 40 kHz-piezoelectric crystal-based bolt-clamped transducer with power rated at 25 W. This was connected to the heater block using a connecting rod and threaded fasteners.
“The use of the connecting rod allows for the coupling of vibrations generated by the transducer, and the reduction of heat transfer from the heater block into the transducer,” said the researchers. “With the hotend section mounted on the printhead assembly, the overall resonant frequency of the printhead was measured to be 34.4 kHz.”
“A frequency-adjustable ultrasonic signal generator was adjusted to the resonant frequency of the printhead and connected to the transducer to provide excitation signals that allowed the nozzle surface to vibrate at the measured frequency. This resonant frequency is determined by measuring the maximum vibration amplitude at the surface of the nozzle while sweeping the generator frequency. When excited at frequencies away from the measured resonance, the transducer output is instead dissipated in the entire transducer–connecting rod–hotend assembly as heat.”
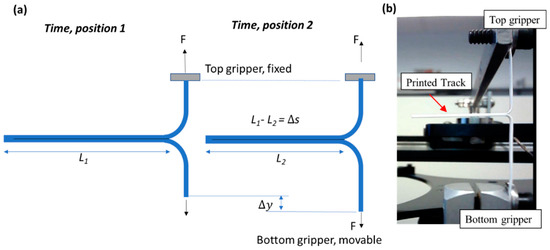
Trouser peel test of two-layer single track specimens for interfacial adhesion strength testing. (a) concept sketch, (b) actual peel test of printed double track specimens.
Researchers measured peeling and energy of the inter-related bonds with the ASTM F88 Peel Test, a system well-known for evaluating adhesion between flexible bands that have been sealed. The test is relevant here as the subject matter is also flexible.
Results of the study show adhesion forces remaining consistent. When track width-to-nozzle diameter ration varies from .74 to 1.47, however, adhesion increases but then balances out at 1.2 and becomes lower at the larger ratios. Such reactions are caused by shear forces in the flow of the polymer traveling from the nozzle to flow horizontally. The wide increases, so do the flow rate and velocity of the polymer increases.
“This increase in flow velocity in turn increases the local shear stresses experienced by the polymer near the top and bottom surfaces of the track and causes an increased amount of disentanglement of polymer chains in those regions,” states the team. “This increase in chain alignment (or decrease in entanglement of polymer chains) can increase the diffusivity of the polymer in the orthogonal directions, which is conducive to an increase in interlayer adhesion due to increased reptation of the polymer across the interface.”
Diffusivity may be caused by polymer chain disentanglement which also adds to chain relaxation and then counteracts polymer reputation increases.
“The effects associated with the use of ultrasound vibrations are attributed to the ultrasound-induced increase in polymer chain relaxation from secondary interaction, and the resulting increase in reptation and entanglement from stretched states,” concluded the researchers.
What do you think of this news? Let us know your thoughts! Join the discussion of this and other 3D printing topics at 3DPrintBoard.com.

(a) Force-Separation distance curves for 1.0 mm-wide example peel tests (b) Interfacial adhesion strength dependence on width of printed tracks for control and ultrasonic vibration-assisted FFF conditions. The error bar represents the standard deviation of adhesion strength measured for four test specimens at a given track width, both in control and ultrasound condition.
Subscribe to Our Email Newsletter
Stay up-to-date on all the latest news from the 3D printing industry and receive information and offers from third party vendors.
Print Services
Upload your 3D Models and get them printed quickly and efficiently.
You May Also Like
Consolidation in AM: How 2025 Is Shaping the Industry’s New Normal
The first half of 2025 has been marked by a clear shift in the additive manufacturing (AM) industry. Companies are no longer just focused on developing new tech by themselves....
Etsy Design Rule Change Reduces Selection of 3D Printed Goods
Online marketplace Etsy has implemented a rule change requiring all 3D printed goods on the site to be original designs. The update to the site’s Creativity Standards states, ¨Items produced using...
U.S. Congress Calls Out 3D Printing in Proposal for Commercial Reserve Manufacturing Network
Last week, the U.S. House of Representatives’ Appropriations Committee moved the FY 2026 defense bill forward to the House floor. Included in the legislation is a $131 million proposal for...
Transforming From Tourist to Native: Duro CEO Michael Corr Explains Why the Company Rebuilt its PLM Software on AI
In these early innings of the AI boom, many market analysts have expressed concern that AI spend has gotten too far ahead of the technology’s proven ability to deliver significant...