Researchers at the Karlsruhe Institute of Technology (KIT) are hoping to make greater strides in biomedical applications through fabrication of microstructures that can adapt like more natural substances, morphing into a ‘switchable’ form. The scientists at KIT have been focused on laser 3D printing in their studies, often a favored mode due to higher levels of performance, strength, and accuracy—along with greater potential for controlling a variety of materials.
In ‘Movable microstructures from the printer: Microstructures can be moved by light and temperature,’ published recently in Nature Communications, the scientists discuss how they are using lasers to control pre-programmed objects with temperature and light to make more dynamic—and useful—systems, particularly for medicine. Using direct laser writing, the KIT team can now easily create smaller 3D printed structures:
“However, for many applications, particularly in biology and biomedicine, it would be desirable not only to produce rigid structures but also active systems that are still movable after the printing process, e.g., that can change their shapes by an external signal,” says Professor Martin Bastmeyer from KIT’s Zoological Institute, along with the KIT Institute of Functional Interfaces.
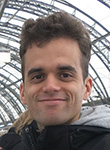
Marc Hippler (Photo credit: KIT)
This innovative KIT study was an interdisciplinary project in the ‘3D Matter Made to Order’ excellence cluster, in coordination with Karlsruhe Institute of Technology and Heidelberg University. Also participating were PhD students attending Karlsruhe School of Optics & Photonics (KSOP) of KIT. The end result has been the creation of structures that move in response to stimulation—mainly via temperature. What makes them unique also is that they are viable in ‘aqueous environments’ and will be helpful in biomedicine.
Grayscale lithography is behind much of the success in this project, allowing for precise settings for movement with focused light serving as a controlling signal.
“We have developed the method to such an extent that we can also manufacture complex structures in which, as a result of external stimulation, the moving parts do not all react in the same way, but show different but precisely defined reactions,” says Marc Hippler, first author in the study.
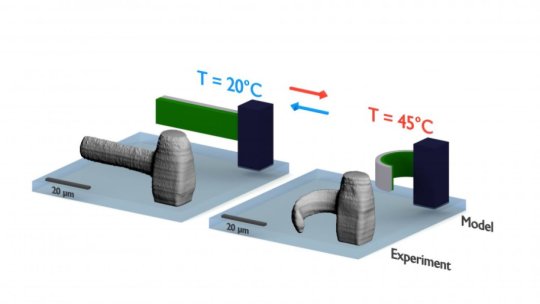
The right material does the trick: The objects from the 3D printer are still movable even after printing and can be stimulated, for example, by a change in temperature.
(Photo Credit: Marc Hippler, C)
Innovation today often draws from sources—sometimes unlikely—like nature, for example, whether we are inspired by something as simple as blades of grass for creating lightweight materials or fish in helping us to move forward in building underwater robots. Making a connection between natural life and creating physical items or hardware that is ultimately, artificial, is the product of creative, open minds whether on the part of a scientist, artist, engineer, or other innovator. Rigidity in thinking or in structures can leave far too many opportunities closed, which is why so many scientists today are taking the 3D realm one step further in 4D, allowing for greater transformation and customization in artificial, printed objects.
What do you think of this news? Let us know your thoughts! Join the discussion of this and other 3D printing topics at 3DPrintBoard.com.
[Source: Science Daily]Subscribe to Our Email Newsletter
Stay up-to-date on all the latest news from the 3D printing industry and receive information and offers from third party vendors.
Print Services
Upload your 3D Models and get them printed quickly and efficiently.
You May Also Like
Consolidation in AM: How 2025 Is Shaping the Industry’s New Normal
The first half of 2025 has been marked by a clear shift in the additive manufacturing (AM) industry. Companies are no longer just focused on developing new tech by themselves....
Etsy Design Rule Change Reduces Selection of 3D Printed Goods
Online marketplace Etsy has implemented a rule change requiring all 3D printed goods on the site to be original designs. The update to the site’s Creativity Standards states, ¨Items produced using...
U.S. Congress Calls Out 3D Printing in Proposal for Commercial Reserve Manufacturing Network
Last week, the U.S. House of Representatives’ Appropriations Committee moved the FY 2026 defense bill forward to the House floor. Included in the legislation is a $131 million proposal for...
Transforming From Tourist to Native: Duro CEO Michael Corr Explains Why the Company Rebuilt its PLM Software on AI
In these early innings of the AI boom, many market analysts have expressed concern that AI spend has gotten too far ahead of the technology’s proven ability to deliver significant...