Many factors impact the quality of 3D printed parts, and as the technology is used more and more for production of final parts rather than just prototyping, it is necessary to investigate those factors more thoroughly so that these final parts can be produced with optimal properties. In a paper entitled “Investigating the effect of fabrication temperature on mechanical properties of fused deposition modeling parts using X-ray computed tomography,” a group of researchers study the effect of printing temperature on the final quality of 3D printed parts.
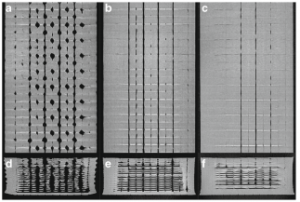
Cross-sectional areas of specimens fabricated at 180 ◦C, 220 ◦C, and 260 ◦C at a–c XY plane and d–f XZ plane
Defects in 3D printed parts are not always visible, but internal defects can have even more of a negative effect than visible ones. In this study, the researchers used CT scanning to non-destructively study 3D printed parts and check their quality. An Ultimaker 2 3D printer was used to print several sample parts from black PLA. Nine sets of three samples each were printed, and the parameters for each part were identical except for the print temperature, which differed in degrees of 10 over a range from 180º to 260ºC.
The 3D printed samples were subjected to tensile tests, and then a CT system was used to test one out of each three-sample set. A 20-mm-long section from the middle of each sample was scanned, and the CT data was used to analyze the porosity of each sample. The researchers found that the weight of the samples was influenced by the temperature at which they had been printed – the higher the temperature, the heavier the part. Part quality also became higher at higher temperatures.
“An in-depth investigation was carried out on the internal geometry of the specimens at the ROI obtained from CT data,” the researchers state. “The lack of deposition resulting in bigger air gap was observed for the specimens fabricated at lower temperatures which confirms the results obtained from the weight measurement.”
The longitudinal filaments showed a lack of bonding at lower temperatures, as did the transverse filaments, although the transverse filaments had less of an effect on the strength of each part than the longitudinal ones. The porosity of each part decreased as temperature went up, as well.
“All the specimens were subjected to a uniaxial tensile load,” the researchers continue. “The results showed that the mechanical properties of PLA specimens are dependent on fabrication temperature. The specimens fabricated at lower temperatures had a higher percentage of elongation and lower yield stress. On the contrary, those fabricated at higher temperatures showed higher yield stress and lower strain at break.”
Overall, it was discovered that parts 3D printed at lower temperatures had greater air gaps in them, which decreased their strength, meaning that for strong parts, higher printing temperatures are ideal.
“Using CT, it was shown that the local density varies throughout the parts regardless of fabrication temperature,” the researchers add. “This means that FDM parts, even those printed at recommended temperature range with 100 % infill, do not achieve homogenous internal structure. Since the porosity is not distributed homogenously throughout the FDM parts, it is not the only parameter for assessing the strength of FDM parts; however, internal geometry features such as minimum cross-sectional area obtained from CT give better information for evaluating the expected strength of FDM parts.”
Authors of the paper include Amir Reza Zekavat, Anton Jansson, Joakim Larsson and Lars Pejryd.
Discuss this and other 3D printing topics at 3DPrintBoard.com or share your thoughts below.
Subscribe to Our Email Newsletter
Stay up-to-date on all the latest news from the 3D printing industry and receive information and offers from third party vendors.
Print Services
Upload your 3D Models and get them printed quickly and efficiently.
You May Also Like
Consolidation in AM: How 2025 Is Shaping the Industry’s New Normal
The first half of 2025 has been marked by a clear shift in the additive manufacturing (AM) industry. Companies are no longer just focused on developing new tech by themselves....
Etsy Design Rule Change Reduces Selection of 3D Printed Goods
Online marketplace Etsy has implemented a rule change requiring all 3D printed goods on the site to be original designs. The update to the site’s Creativity Standards states, ¨Items produced using...
U.S. Congress Calls Out 3D Printing in Proposal for Commercial Reserve Manufacturing Network
Last week, the U.S. House of Representatives’ Appropriations Committee moved the FY 2026 defense bill forward to the House floor. Included in the legislation is a $131 million proposal for...
Transforming From Tourist to Native: Duro CEO Michael Corr Explains Why the Company Rebuilt its PLM Software on AI
In these early innings of the AI boom, many market analysts have expressed concern that AI spend has gotten too far ahead of the technology’s proven ability to deliver significant...