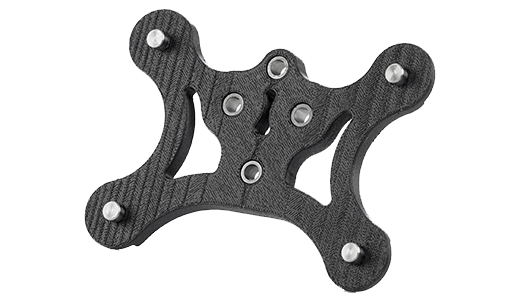
A Carbon Fiber Polyamide Jig made by Stratasys
When Stratasys released the $70,000 Fortus 380mc Carbon Fiber Edition the company already alluded to Team Penske using Stratasys machines for their racing team. Team Penske is a leading Indy, Nascar and IMSA racing team. Active since the late nineteen sixties the team has won Indycar Championships numerous times and is one of the most celebrated teams in the sport while winning 174 Nascar victories as well. We interviewed Stratasys and Team Penske about their collaboration to see how racing car teams use 3D printing.
Matt Gimbel, Team Penske Production Manager told 3DPrint.com that, “3D printing enables us to do things that we can’t do or can’t do as fast with other manufacturing methods.” When asked what the team made with 3D Printing Gimble told us that they make “Wind tunnel model test components, composite tooling, manufacturing jigs and fixtures, engineering prototypes and race car components.” The Team turns to 3D printing because “we can design and print manufacturing and composite tools faster than machining in metal and tooling board. 3D printed prototype components can also help avoid costly mistakes in the design process.”
With car companies its usually short-run mass customization parts or prototypes that get 3D printed. In many race teams such as F1 teams use 3D printing, their motivation is usually in saving weight on the car. With Penske speed seems to be the critical factor as well as making unique parts that can not be manufactured through other means. The company seems to be using this as a practical technology to extend their capability. Gimbel also mentioned that they are looking at internal topology optimization. If they indeed are looking at the inside of all of their components then this could have decided advantages for the team in optimizing air flow to intakes for example or other key components. Looking beyond weight at attaining the right fuel mix for example or optimizing air or fuel flow through a part would be an excellent way for them to use 3D printing to get better results on race day. Carbon Fiber-filled Nylon 12 would let them place such parts on numerous components perhaps even in some parts of the engine bay and throughout much of the car.
Scott Sevcik, VP Manufacturing Solutions at Stratasys said about the collaboration,
The race track is an extreme environment where new technologies are put to the test in an effort to give the race team an edge. As a result, it’s an incredible learning environment. Race teams push the boundaries of automobile performance, and technologies that prove themselves on the track then tend to transition to the mass market to scale the same performance benefits highlighted by the race team. So yes, the fact that Stratasys FDM is proving itself on the track and in the pit is a major step toward finding our place on the highway and on the production floor. Transition takes time, so it’s not something we will see over night, but Stratasys FDM is mature, has proven its value in these challenging environments, and is definitely making great strides into production today.
In a subsequent press release, the Team also mentioned mirror housings and other aero components on the car that could be optimized with the FDM materials. This kind of components has been made a long time in car racing with 3D printing. The inside joke has always been that race car teams “only print mirrors.” Since car racing is so competitive and often engineering details are guarded secrets the only thing race car teams routinely talk about are the 3D printed mirrors. In the paddock, however, you can see that the technology is used much more throughout. Fused Deposition Modeling is ideal for housings and things such as jigs and fixtures. Especially with stiff materials such as carbon fiber enhanced materials durable components such as those can really aid a team. The technology also reliably can print dimensionally accurate tough parts suited for many of the polymer components of a race car. Whats an interesting to note here is that Penske seems to have adopted 3D printing as a regular process throughout their design and development process. No longer the exotic white elephant here is an example where it seems to be an integrated bit of tooling for the design and manufacturing of race cars. The normalization of 3D printing and its adoption in manufacturing is the key thing that Penske and others are doing with our technology
Subscribe to Our Email Newsletter
Stay up-to-date on all the latest news from the 3D printing industry and receive information and offers from third party vendors.
Print Services
Upload your 3D Models and get them printed quickly and efficiently.
You May Also Like
Consolidation in AM: How 2025 Is Shaping the Industry’s New Normal
The first half of 2025 has been marked by a clear shift in the additive manufacturing (AM) industry. Companies are no longer just focused on developing new tech by themselves....
Etsy Design Rule Change Reduces Selection of 3D Printed Goods
Online marketplace Etsy has implemented a rule change requiring all 3D printed goods on the site to be original designs. The update to the site’s Creativity Standards states, ¨Items produced using...
U.S. Congress Calls Out 3D Printing in Proposal for Commercial Reserve Manufacturing Network
Last week, the U.S. House of Representatives’ Appropriations Committee moved the FY 2026 defense bill forward to the House floor. Included in the legislation is a $131 million proposal for...
Transforming From Tourist to Native: Duro CEO Michael Corr Explains Why the Company Rebuilt its PLM Software on AI
In these early innings of the AI boom, many market analysts have expressed concern that AI spend has gotten too far ahead of the technology’s proven ability to deliver significant...