Researchers in Germany Design Lower-Cost Device Screen Using Luminescent Proteins & 3D Printing Technique
In today’s society, it seems nearly everyone owns at least two or three devices with screens. Most devices with a screen these days, from televisions to more portable things like tablets and cell phones, use liquid crystal display (LCD) screens, mainly because of their use of inorganic white light-emitting diodes (LEDs). LED screens are energy-efficient and provide high-quality images. However, it’s not all good: LCD screens use expensive color filters, and other components used to create them are not easy to recycle. These displays also have limited brightness and contrast levels. However, a team of German and Spanish scientists with the Friedrich-Alexander University of Erlangen-Nurnberg (FAU) may have the solution to these challenges. We’ve written about this university before, when its Factory Automation and Production Systems Institute (FAPS) worked with printing conductive elements at microscopic levels using an Aerosol Jet Quad Print Engine.
The research team, supported by FAU’s Emerging Field Initiative (EFI), has designed a new, cheaper screen, which is made of an ecological hybrid material of natural elements: luminescent proteins. The proteins can be used in color filters and backlighting systems, and are made with 3D printing, lowering costs and environmental footprint of production. The proteins are used in two parts of the new display, the first of which is the backlighting. The proteins use a Bio-LED, featuring white light, with colored luminescent proteins. This technology can effectively be used as a substitute for the rare and more expensive inorganic phosphorous that is traditionally used in LED displays.
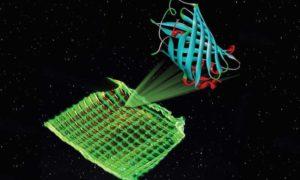
Image of a colour filter with green and red luminescent proteins printed on a microgrid structure. [Credit: Katharina Weber]
Rubén D. Costa, who is leading the team of scientists, says, “The proteins have a photoluminescence quantum yield of more than 75 percent. High efficiency is guaranteed. In addition, they have a low emission bandwidth (30 to 50 nm), ensuring high color quality and degradation does not produce significant colour changes.”
The details of the second display component enhanced by the luminescent proteins, the color filter, are described in an paper published in the journal Advanced Functional Materials. Using an SLA 3D printing technique, the luminescent proteins are stored in a “polymeric matrix with micrometric resolution,” which allows them to keep their luminescence and stability. The paper, “Micropatterned Down-Converting Coating for White Bio-Hybrid Light-Emitting Diodes“, explains that the scientific community has recently started to develop a new kind of LED, specifically white hybrid light-emitting diodes (WHLED). These look to be a solid solution for environmentally sustainable white lighting sources, because they are, among other things, nontoxic and low-cost.

From the paper: (Upper part) Images of protein-based rubbers with line (left), open-grid (middle), and closed-grid (right) microstructures prepared from a b-PEO:l-PEO gel 10:1 wt under UV excitation (310 nm; 8 W). Please note that mCherry and eGFP correspond to red and green colors, respectively. (Central part) The corresponding height profiles obtained via alpha-step measurements. (Lower part) Images that provide clear insights into the easy peel-off from the substrates and the easy handling of the protein-based rubbers under room light (left and middle) and UV excitation (right, 310 nm; 8 W).
The paper explains the process thoroughly, but the researchers were able to control the placement of these proteins using 3D printing, describing “a straightforward way to design microstructured single-layer coatings, in which the proteins are placed at our command by using 3D printing” as they turned to stereolithography to plot the proteins. Their packing fabrication process involves “the preparation of a gel before the formation of a rubber-like material,” so the proteins were precisely placed during “the plotting of the gels in different micropatterned forms, such as lines, open-grids, and closed-grids. They were further applied as single-layer down-converting coatings for preparing Bio-WHLEDs.”
Costa explains, “This colour filter meets the necessary requirement to improve displays currently being used in terms of contrast and brightness, within quality standards demanded across the market. This new material will allow for the development of energy-efficient Bio-displays for TVs and mobile telephones, with low production costs, high image quality and ecological sustainability. Also, these filters are not rigid, allowing them to be used in devices which are flexible and light.”
“Micropatterned Down-Converting Coating for White Bio-Hybrid Light-Emitting Diodes” is available here, and the paper’s authors include Lukas Niklaus, Samira Tansaz, Haider Dakhil, Katharina T. Weber, Marlene Pröschel, Martina Lang, Monika Kostrzewa, Pedro B. Coto, Rainer Detsch, Uwe Sonnewald, Andreas Wierschem, Aldo R. Boccaccini, and Rubén D. Costa. Discuss in the 3D Printed Screens forum at 3DPB.com.
[Sources/Images: Phys Org / Advanced Functional Materials]
Subscribe to Our Email Newsletter
Stay up-to-date on all the latest news from the 3D printing industry and receive information and offers from third party vendors.
Print Services
Upload your 3D Models and get them printed quickly and efficiently.
You May Also Like
Consolidation in AM: How 2025 Is Shaping the Industry’s New Normal
The first half of 2025 has been marked by a clear shift in the additive manufacturing (AM) industry. Companies are no longer just focused on developing new tech by themselves....
Etsy Design Rule Change Reduces Selection of 3D Printed Goods
Online marketplace Etsy has implemented a rule change requiring all 3D printed goods on the site to be original designs. The update to the site’s Creativity Standards states, ¨Items produced using...
U.S. Congress Calls Out 3D Printing in Proposal for Commercial Reserve Manufacturing Network
Last week, the U.S. House of Representatives’ Appropriations Committee moved the FY 2026 defense bill forward to the House floor. Included in the legislation is a $131 million proposal for...
Transforming From Tourist to Native: Duro CEO Michael Corr Explains Why the Company Rebuilt its PLM Software on AI
In these early innings of the AI boom, many market analysts have expressed concern that AI spend has gotten too far ahead of the technology’s proven ability to deliver significant...