It’s not unlikely in most cases today that when we hear the words firsts and technology—3D printing is usually right around the corner, if not front and center, in the innovative mix. And what a ‘mix’ that is—reaching around the globe to affect nearly every sector of manufacturing and product development. But when NASA is announcing yet another dramatic first—and a new part—that tends to overshadow nearly anything being produced today, from bio-inks and 3D printed cellular structures, to spectacular new automotive components, new materials, and far more.
We perk up when we hear about space travel and all that entails quite simply because it’s still so unknown, so fascinating, so almost inconceivably far away—and there is always an element of uncertainty involved. While everything may test out on Earth–will it work once we send it into orbit? Scientists and aerospace engineers are continually working to take the risk factor out of their very costly missions to space. A very important part of that involves researching and developing strong new materials for added durability and functionality in the outer expanses of our universe.
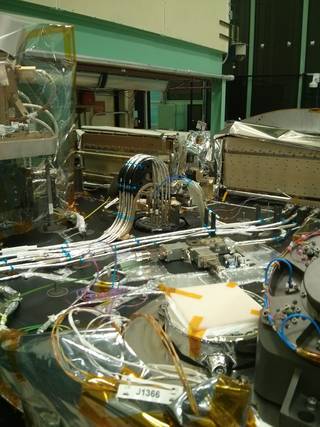
The 3D manufactured part — a black bracket holding the instrument’s fiber-optic cables — is visible in the back of the ATLAS instrument. (Photo credits: NASA)
Currently, one new 3D printed part is garnering a lot of attention as part of the latest ICESat-2 project, which aims to examine and measure changes in ice-sheet elevations, sea-ice thicknesses, and global vegetation in Greenland and the Antarctic. The Ice, Cloud and Land Elevation Satellite-2 will bear a 3D printed bracket that supports the fiber-optic cables for the central instrument of this satellite: the Advanced Topographic Laser Altimeter System (ATLAS).
As we reported very recently, the material being used for this bracket was customized and created by Stratasys just for the rigors of space travel. Polyetherketoneketone (PEKK) will make its debut in space as part of the satellite in two years, allowing for this central bracket component to be only the second 3D printed part to go into space so far.
Aside from the considerable perks of being able to make the bracket quickly, on demand, and at a much lower cost (with a savings of up to four times greater), PEKK is desired in this construction mainly because of its electrostatic dissipative properties, durability, and heat resistance—qualities found in Stratasys materials that are predecessors—ABS-ESD7 and ULTEM 9085, which also played a part in constructing materials that were produced and flown on the International Space Station by the Ames Research Center’s Synchronized Position Hold, Engage, Reorient, Experimental Satellites (SPHERES) program. PEKK’s base resin also allows for speedy manufacturing of other parts and components.
“Had we manufactured this part classically, it would have taken six to eight weeks. We got it in two days,” said Oren Sheinman, the ATLAS mechanical systems engineer.
The dissipative qualities ensure that electrostatically sensitive devices are more protected, due to the reduction of build-up in static electricity. Another interesting benefit is that little ‘outgassing’ is experienced with PEKK (think about the ‘new car’ smell as a good example of a symptom of this), again protecting instruments in helping to eliminate condensation on crucial devices.
ATLAS is certainly crucial in itself—and according to ATLAS Instrument Scientist Tony Martino, is a ‘technical marvel,’ as the first space-borne, photon-counting laser altimeter. This precision instrument will help to record the ‘time-offlight’ of individual photons as they travel from the instrument, reflect off Earth’s surface, and then return. Scientists are then able to calculate Earth’s surface elevation as they are examining the ice sheets.
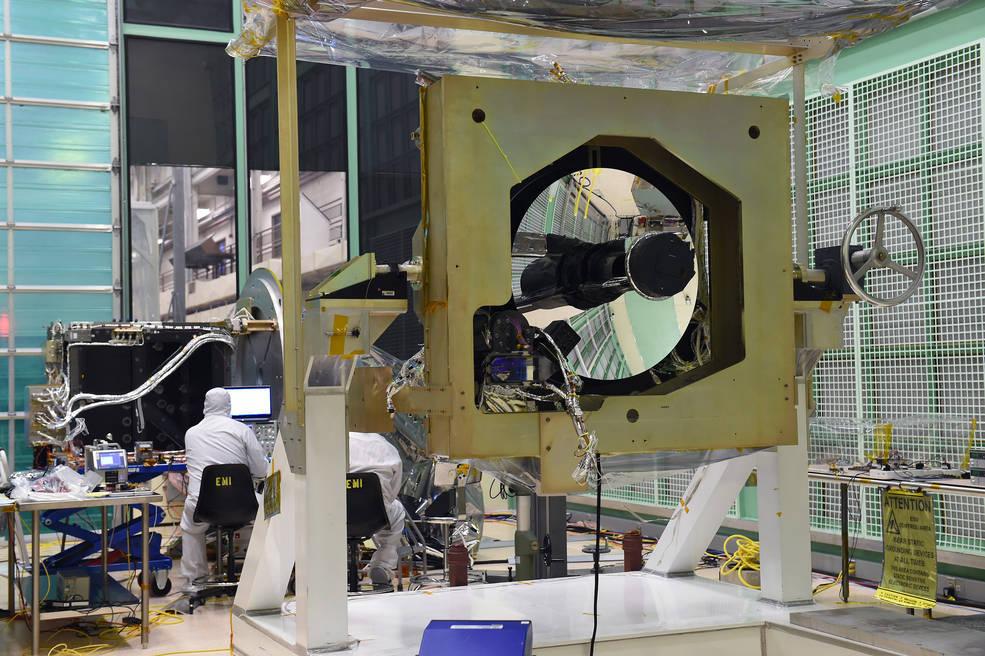
The ATLAS instrument inside a Goddard cleanroom where it was assembled. (Photo credit: NASA/D. McCallum)
This second ICESat mission is different in that for the first one, only a single laser was employed. ICESat-2 offers incredible new innovation, allowing for a green-light laser to split into six beams, arranged in three pairs, firing continuously at a rapid 10,000 pulses per second toward Earth—and offering much better data samples. Higher speed and higher resolution will mean much better performance and results from this study, due to the innovations and ‘dense crosstrack samples’ offered with ATLAS. Over three years, the satellite will traverse over the same area every 90 days, offering consistent, true data regarding changes in the ice.
“It’s almost completely built,” Martino said, adding that the spacecraft will fly on the last Delta II launch vehicle. “All functional parts are there and our first comprehensive testing starts in February. We’re on track.”
The material used to make the bracket for ATLAS encompasses nearly all of the reasons that 3D printing is making such an impact on the world—and missions to space, especially the much-publicized Project Orion Mission, set to go to Mars, with astronauts wearing futuristic new spacesuits and rocket components featuring 3D printed components. Another concept being intricately explored is that of 3D printed, self-sustainable habitats for space missions, and colonization. Discuss this new mission in the 3D Printed Bracket for ICESat-2 forum over at 3DPB.com.
[Sources: Engineering.com; NASA’s Cutting Edge]Subscribe to Our Email Newsletter
Stay up-to-date on all the latest news from the 3D printing industry and receive information and offers from third party vendors.
Print Services
Upload your 3D Models and get them printed quickly and efficiently.
You May Also Like
Nikon SLM Solutions Sells SLM 500 to Primary Weapon Systems to Expand Suppressor Production
Primary Weapons Systems (PWS) is a Boise, Idaho-based manufacturer of suppressors, firearms, and related components. A subsidiary of Vigilant Gear and a sister company to aftermarket Glock slide manufacturer Lone...
3DPOD 261: Tooling and Cooling for AM with Jason Murphy, NXC MFG
Jason Murphy´s NXC MFG (Next Chapter Manufacturing) is not a generalist service; instead, the company specializes in making tooling. Using LPBF and binder jet, the company produces some of the...
HP and Firestorm Labs Form Partnership to Use Multi Jet Fusion 3D Printers in Deployable Factories
HP Inc., maker of a range of additive manufacturing (AM) solutions including the Multi Jet Fusion (MJF) ecosystem, has announced a partnership with Firestorm Labs, a developer of containerized, deployable...
3D Printing News Briefs, July 2, 2025: Copper Alloys, Defense Manufacturing, & More
We’re starting off with metals in today’s 3D Printing News Briefs, as Farsoon has unveiled a large-scale AM solution for copper alloys, and Meltio used its wire-laser metal solution to...