90 to 95 percent of the part files I received as a Regional Technical Manager for Desktop Metal were designed and proved out for another manufacturing process. Companies all over the map were looking for a better alternative for producing their components, sometimes because of supply chain issues, such as extremely long lead times (the longest I heard was 42 weeks).
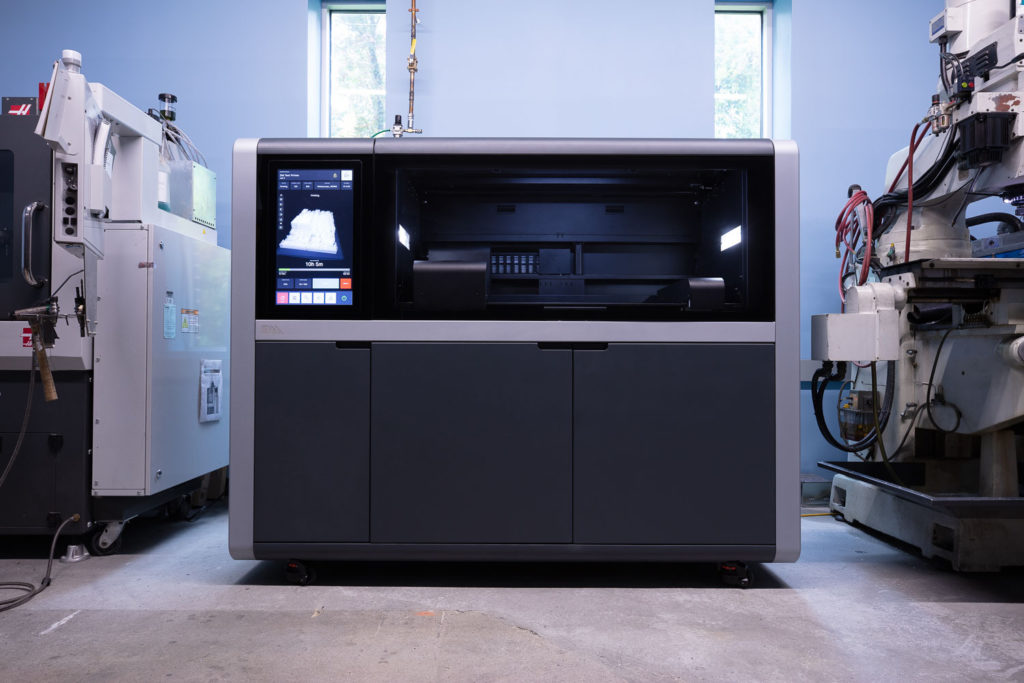
I firmly believe we’re still feeling the after effects of the COVID pandemic, but my time spent learning and supporting metal binder jet has revealed the challenges and benefits of this exciting technology. Let me say this, 3D printer original equipment manufacturers (OEMs) pushing for higher volume part production need to shift their mentalities to actual manufacturing. They need to consider what a process looks like that will take the part from design for AM all the way through qualification and the many steps involved therein.
Additive manufacturing (AM) companies looking to push the technology as a solution for mainstream production are missing the mark when it comes to branding, tailored production, automation partnerships, marketing, and messaging to deepen connections with manufacturers showing interest in this technology.
Metal Binder Jet’s Capabilities
Size: At its current stage, metal binder jet is good for 3D printing small to medium-sized parts—that is roughly 1 in x 1 in x 1 in to 6 in x 6 in x 6 in, after scale-up compensation for shrink during sintering. This is because, with current liquid binders for holding metal powders together, green part strength is not optimal after de-powdering and just prior to the sintering process. This limits the size of parts, as well as the geometries, that can be produced until binders are improved to demonstrate greater strength.
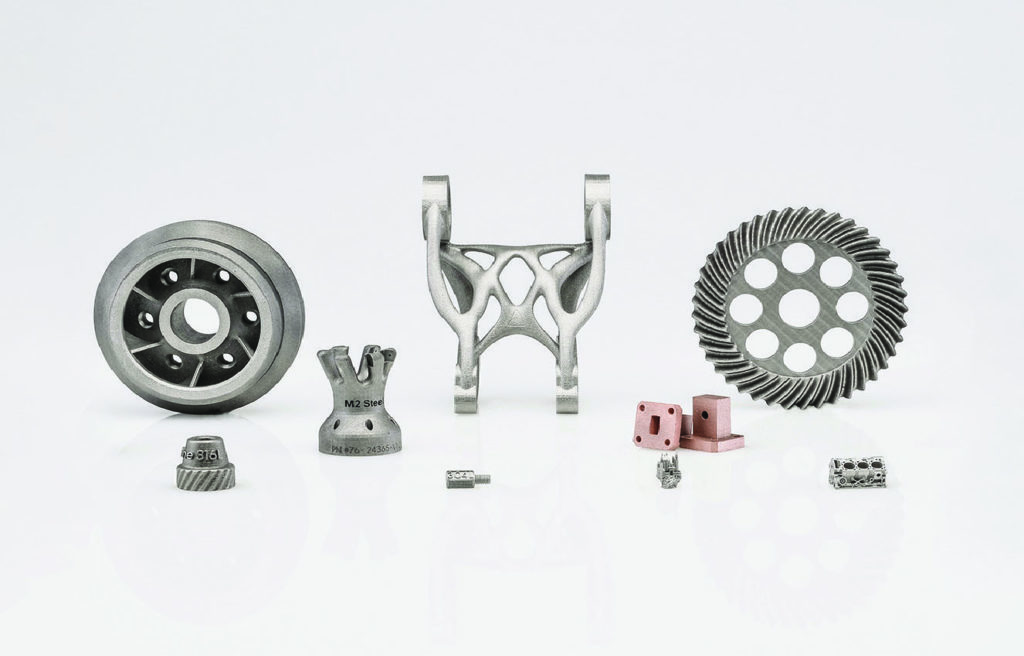
Part quality: Items with metal binder jet demonstrate strength and density (98%) similar to casted parts. Part tolerance is between .3mm – .5mm, increasing the need for post-print machining to achieve desired tolerances. Surface finish out of the printer may not be ideal for consumer standards, so tailored finishing methods will need to be applied. This means that components will need to be post-processed to meet the proper tolerance expectations, part strength, and surface finish requirements. Of course, accuracy and surface finish is not only necessary for metal binder jet, but for most all AM technologies.
Materials: Powder material pricing still remains to be made even more competitive (against other metal AM technologies) to attract more manufacturers. Open material systems will help to diversify powder supply chain costs for users. Material change out for binder jet is much easier compared to other metal printing technologies, requiring, on average, 30-40 minutes to perform. Since this is similar to metal injection molding (MIM), the material availability and speed for material qualification is generally faster.
Speed: To date, metal binder jet is still considered the fastest metal printing technology capable of successfully producing a vast array of geometries. It has certainly come a long way since it was first brought to market in 1999. It’s still the most competitive in terms of ownership when it comes to part price and entry compared to laser powder bed fusion.
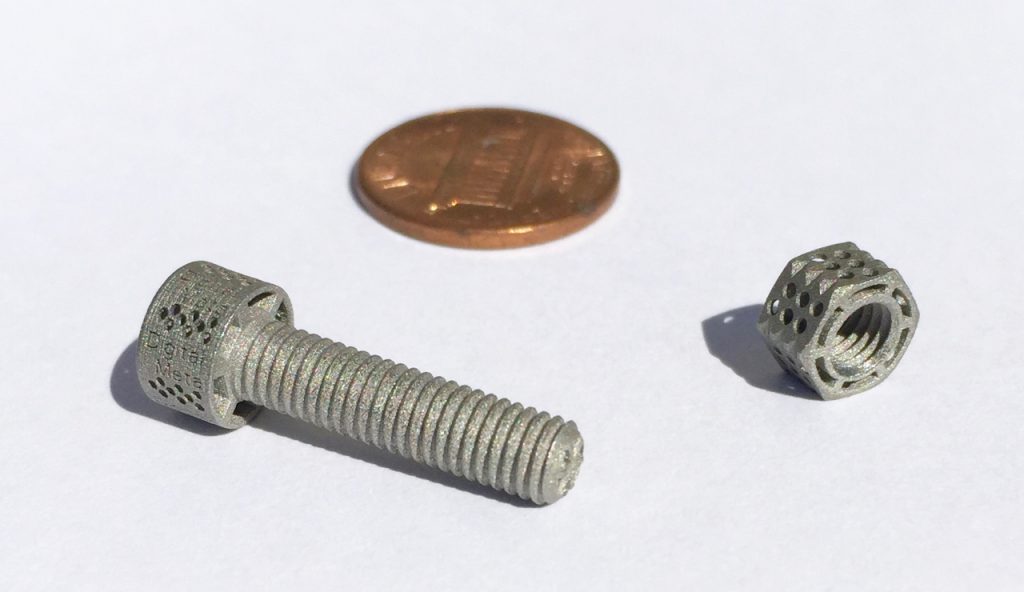
Ease-of-use: I also believe that, to date, metal binder jet could be the easiest technology for producing a metal part without an advanced degree due to the traditionally easy user interface. A user could have a part file processed and ready to print in as little as 20 minutes. This includes the sintering simulation software(s) available, which allow for print optimization, such as negative offsets for warp prediction during the sintering cycle.
Supports: This software also eliminates the need for support setters (there are no anchors attaching the part to the build plate to mitigate warp) and support removal is as easy as lifting the component off the printed support setter due to the application of an anti-sintering agent to the surface of the support setter to eliminate part and support setter bonding.
Truth in Marketing
AM companies, including marketing teams, looking to push the envelope in terms of helping companies adopt metal binder jet need to understand that, in order for the technology to be implemented correctly, the part file that was originally sent will need to go through the approval steps for part qualification (i.e., planning, design, prototype, testing, design for manufacturing, manufacturing, post-manufacturing). There are manufacturing principles that need to be applied to taking a design to mainstream production, just as was the case for the part’s predecessor manufacturing process.
When it comes to discussions with clients seeking to purchase metal binder jet, both parties on either side of the table have to understand that the part file being evaluated for metal binder jet has a very high chance that it has already been proven out for another manufacturing process (CNC, casting, injection molding, etc). If the potential customer is not open to redesigning for AM qualification, I recommend they stick with the current manufacturing process. I have always said and have made engineering teams realize that, once a client is open to redesigning for AM, a whole new realm of possibilities and increases in supply chain options is opened up to them.
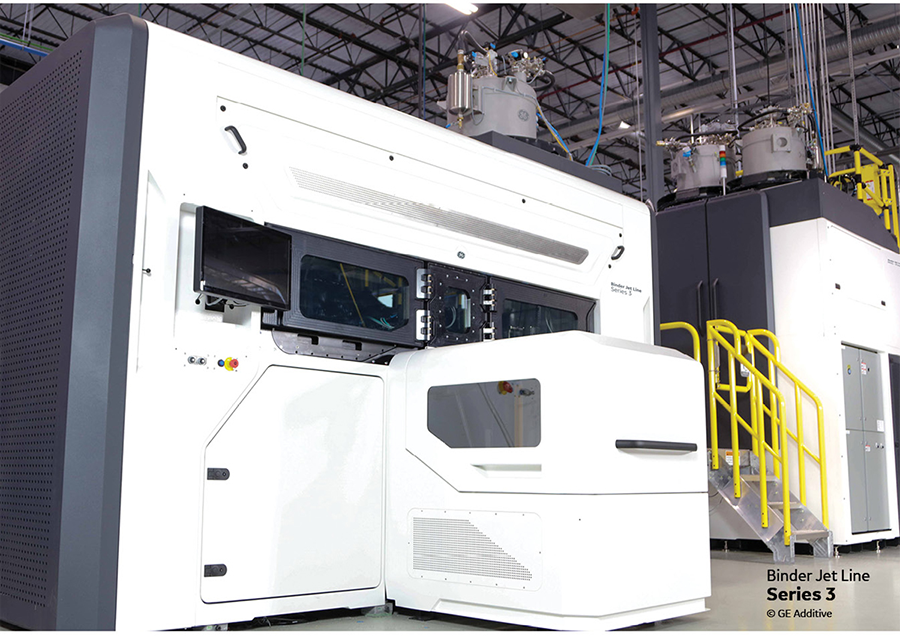
It is crucial that we convey the message that this process isn’t a magic’s button, but another means of producing a part. Of course, qualification can increase unwanted sale cycle times. However, assuring that a component is fit for a given production process is the route manufacturers have gone for years. Simply because the manufacturing technique is 3D printing at higher volumes doesn’t mean that the same mass production principles need to be applied.
If companies are willing to journey down the path of redesigning the part file for metal binder jet to ensure that it qualifies and meets consumer standards, then there is a very high chance you have a partner that will be well invested into adopting the technology.
Takeaways
To sum up, for companies looking to adopt this technology, they will have to be willing to journey the path of part qualification and reaching consumer standards in order for this to be a success and compete with other traditional processes—especially if they are targeting mid-higher part volumes.
On the other side, metal binder jet companies need to put on their manufacturing hats when it comes to language and understanding the steps necessary to qualify a part for a new process. Although metal binder jet seems a bit like magic, we have to take a couple of steps back and comprehend that the part journey to qualification for manufacturing will be similar to traditional production processes.
Could there be more steps involved with metal binder jet? Absolutely, but the end result could be a component that demonstrates increased innovation and performance. In most cases, metal binder jet is not necessarily going to save a customer production steps, but it will result in a printed part in hand much faster, which then leads into the additional finishing steps that are needed to reach consumer quality acceptance.
Overall, I believe there is a place for metal binder jet, but considerations for adoption and success need to be recognized, as is the case with any new or existing manufacturing process that is being explored for implementation.
Feature image courtesy of JPB.
About the Author
Michael Block is currently the Business Development Manager for Nota 3D Solutions. Mike has spent nearly 15 years in additive manufacturing fulfilling various roles with industry leading companies, as well as running his own startup which offered tailored production automation technologies, parts, and consulting services to various clients. Michael has extensive experience with both polymer and metal 3D printing technologies that are pushing the boundaries of production and helping manufacturers find a quicker and more innovative approach to market.
3DPrint.com and SmarTech Analysis are hosting Additive Manufacturing Strategies in New York City on February 7-9, 2023. Register for the event here to learn from and network with the most exciting companies and individuals in AM.
Subscribe to Our Email Newsletter
Stay up-to-date on all the latest news from the 3D printing industry and receive information and offers from third party vendors.
Print Services
Upload your 3D Models and get them printed quickly and efficiently.
You May Also Like
Nikon SLM Solutions Sells SLM 500 to Primary Weapon Systems to Expand Suppressor Production
Primary Weapons Systems (PWS) is a Boise, Idaho-based manufacturer of suppressors, firearms, and related components. A subsidiary of Vigilant Gear and a sister company to aftermarket Glock slide manufacturer Lone...
3DPOD 261: Tooling and Cooling for AM with Jason Murphy, NXC MFG
Jason Murphy´s NXC MFG (Next Chapter Manufacturing) is not a generalist service; instead, the company specializes in making tooling. Using LPBF and binder jet, the company produces some of the...
HP and Firestorm Labs Form Partnership to Use Multi Jet Fusion 3D Printers in Deployable Factories
HP Inc., maker of a range of additive manufacturing (AM) solutions including the Multi Jet Fusion (MJF) ecosystem, has announced a partnership with Firestorm Labs, a developer of containerized, deployable...
3D Printing News Briefs, July 2, 2025: Copper Alloys, Defense Manufacturing, & More
We’re starting off with metals in today’s 3D Printing News Briefs, as Farsoon has unveiled a large-scale AM solution for copper alloys, and Meltio used its wire-laser metal solution to...