Since the day Made In Space (now a subsidiary of Redwire) first installed a 3D printer aboard the International Space Station (ISS), there have been numerous efforts to advance additive manufacturing (AM) in space. Most recently, the European Space Agency (ESA) unveiled the finalized version of a microgravity polymer printer capable of 3D printing parts larger than the machine itself.
Now, as a part of the Metal3D project, the ESA is working along with a number of firms that include Airbus Defense and Space and AddUp to send a metal 3D printer to the ISS. To be launched in February 2023, the system will be installed in the Columbus module. Already on its second iteration, the Metal3D machine relies on wire-fed directed energy deposition (DED) technology.
“AddUp plays an important role in the realization of this mission, but its involvement in the project goes back to the pre-project phase where the feasibility of the project had to be demonstrated. This first part, carried out on the premises in Salon de Provence, built the foundations of what the machine is today. In the final version of the machine, AddUp is in charge of the mobile axes, the structural parts and the software of the machine,” stated Alexandre Piaget, R&D engineer at AddUp.
DED is a great process for space applications. This is because a contained wire spool is less dangerous than powder, which can be explosive and also could get in absolutely everything and everywhere in case of a spill. The wire DED system will print in 316L stainless steel, a common material with a wide array of applications in bodies, machines and structures. Interestingly, this opens the Metal3D printer up as a single system for many distinct parts.
The system keeps the feeder and head fixed within the frame, while the print platform rotates on three axes. The enclosed chamber is filled with nitrogen, which is filtered and reused. The current printer is a technology demonstrator with which the team hopes to characterize the material and test the machine itself extensively. In one test, identical parts will be printed on the ground and in space to test the effects of microgravity. Hopefully, both machines have very little in the way of run to run difficulties.
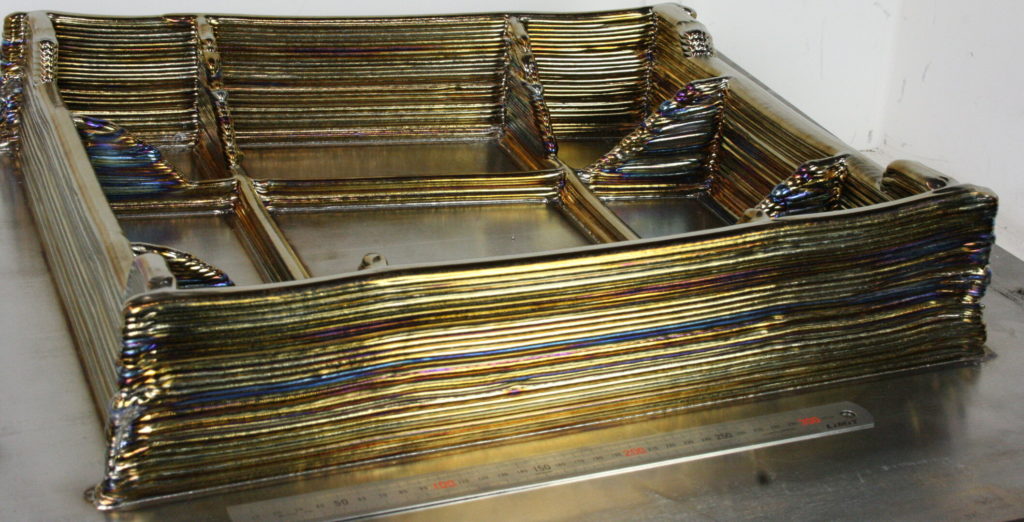
A demo DED structure ESA made in 2013
The project has been commissioned by ESA, with Airbus providing project management, the energy source, and material feed system for the printer, which is being made by Cranfield University. Specialized space engineering firm Highftech will provide the enclosure for the printer. AddUp helped initiate the project and is responsible for motion control and the guts of the machine, including all internal components, communication with the printer, as well as the software.
Europe has long been behind the use of additive in space. The Americans got an early start with high defense spending on satellites rockets and many more similar components. NASA and its Jet Propulsion Laboratory also undertook pioneering roles not only in using 3D printing but also in developing these technologies for use in space. NASA itself took a particular shine to electron beam melting. Now, the commercial U.S. space firms are leading in 3D printing, egged on and helped by NASA´s early work. Additive is the one key production technology shared by all of these commercial firms, especially in propulsion.
According to the “3D Printing in Commercial Space: The AM Ecosystem in the Private Space Industry” report from SmarTech Analysis, the private space 3D printing industry is expected to be worth $5.4 billion by 2031. For rockets and engines, 3D printing is able to bring parts quicker to market, can iterate faster, is lower cost for entirely new parts, and can make novel shapes and textures, all while reducing weight. Meanwhile, for longer space missions, 3D printers seem to be an unmissable piece of kit that can extend journeys by allowing crews to deal with problems and replace broken components in an improvisational manner. With permanent space stations, additive could also be beneficial, even enabling the building of structures on the moon and in space. In other words, it’s good that Europe is becoming more ambitious with space 3D printing.
Will their wire-fed approach win the day? Wire DED processes are cheap and can readily use recycled and comparatively low-quality materials. In a Wall-E-style space scavenging scenario, the process would be very appealing. Wire DED is usually low cost, as well, but this matters less in space.
I love that it is much safer in material storage and in machine operation than the powder bed processes. On the other hand, usually these wire-based systems do not have the accuracy offered by other printing technologies. Typically, parts will have to be machined in order to achieve proper surface smoothness, for example. How ESA engineers its way around these requirements will be key to the future applicability of this technology in space manufacturing.
Subscribe to Our Email Newsletter
Stay up-to-date on all the latest news from the 3D printing industry and receive information and offers from third party vendors.
Print Services
Upload your 3D Models and get them printed quickly and efficiently.
You May Also Like
Nikon SLM Solutions Sells SLM 500 to Primary Weapon Systems to Expand Suppressor Production
Primary Weapons Systems (PWS) is a Boise, Idaho-based manufacturer of suppressors, firearms, and related components. A subsidiary of Vigilant Gear and a sister company to aftermarket Glock slide manufacturer Lone...
3DPOD 261: Tooling and Cooling for AM with Jason Murphy, NXC MFG
Jason Murphy´s NXC MFG (Next Chapter Manufacturing) is not a generalist service; instead, the company specializes in making tooling. Using LPBF and binder jet, the company produces some of the...
HP and Firestorm Labs Form Partnership to Use Multi Jet Fusion 3D Printers in Deployable Factories
HP Inc., maker of a range of additive manufacturing (AM) solutions including the Multi Jet Fusion (MJF) ecosystem, has announced a partnership with Firestorm Labs, a developer of containerized, deployable...
3D Printing News Briefs, July 2, 2025: Copper Alloys, Defense Manufacturing, & More
We’re starting off with metals in today’s 3D Printing News Briefs, as Farsoon has unveiled a large-scale AM solution for copper alloys, and Meltio used its wire-laser metal solution to...