It was a busy month for 3D printing developer Formlabs. After announcing a new $150 million funding round and doubling its valuation to $2 billion, the ten-year-old company revealed it teamed up with Autodesk to streamline digital workflow with new CAD tools for 3D printing. At the same time, the startup unveiled a new high-performance nylon material powder, which is ideal for users to print parts that need to bend or withstand impacts, such as hinges, clips, and orthotics.
Formlabs users will now have access to a brand new toolset that combines the best of Autodesk’s versatile CAD package with professional 3D printing results. Formlabs and Autodesk’s Fusion 360 teamed up to streamline users’ digital workflow so they can iterate new ideas in just a few steps. The partnering businesses said they were inspired by a diverse, shared user community worldwide that is already leveraging Fusion 360 with Formlabs Form 3 printers. After this announcement, digital workflows for Formlabs 3D resin printers Form 3 and Form 3L will get even more tailored to specific goals since both platforms will be the first to be included in this brand new toolset.
Introduced by the companies as a “match made in 3D printing heaven,” the software integration includes a brand new graphic interface where users can visualize and communicate how parts will fit into the Form 3 and 3L build volumes. According to the companies, designers can customize a design dashboard to align with their most frequently used 3D printing workflows. Teams can streamline file management by directly exporting a .form file from Fusion 360. This eliminates the need for downloading individual STL files, giving designers and manufacturers more reliable version control.

Formlabs and Autodesk’s Fusion 360 have partnered for 3D printing integration, pictured here, a chess set created by Will Qiu. Image courtesy of Formlabs.
Autodesk Senior Product Manager Sualp Ozel said integrating Formlabs printers into Autodesk Fusion 360 is a big step toward streamlining additive workflows, capturing both design and manufacturing intent in a single, unified platform while saving money and improving outcomes.
With the central pursuit of creating synergy, the duo will enable users to design parts effortlessly using Fusion 360’s flexible 3D CAD software. The designs are then directly sent to PreForm, Formlabs’ print preparation software, and finally printed on Form 3 and Form 3L. Using the integration between Fusion 360 and Preform, companies can import scans and print parts on the fly without saving dozens of STL files for single-use parts. For example, Manchester, UK 3D printing hub PrintCity said the combination of Autodesk Fusion 360 and Form 3 enables them to quickly identify a feasible workflow and present it to their clients, no matter the size of the organization.
Other users, like Curtis Kennedy, creator of the wall-mounted massage ball Vertiball for athletes to manage their own muscle pain relief, found that reliability in both Fusion 360 and Form 3 was critical when designing each moving and gliding part of the Vertiball prototype. Vertiball’s design team performed stress analysis in Fusion’s simulation environment before committing material resources to a Form 3 prototype. The key innovation behind Vertiball is its patented industrial-strength suction cup that can attach to smooth, non-porous surfaces, so Kennedy said he needed to validate the theoretical functionality of a design through simulation before prototyping.

Wall-mounted massage ball Vertiball for athletes, Vertiball. Image courtesy of Vertiball.
Aside from enabling faster design and manufacture, Formlabs is constantly looking to provide users with high-performance materials. Their latest addition is a nylon powder, ideal for functional prototyping and small batch production. Fitting for manufacturing, engineering, and healthcare uses, the Nylon 11 Powder is the second material available for Formlabs’ Fuse 1 high-performance selective laser sintering (SLS) industrial printer.
The company said materials are key to expanding the range of possible applications for businesses. Its Nylon 11 Powder was developed to bolster design and creative capabilities with low cost per part. In fact, it is ideal for expanding the accessibility and user-friendliness of Formlabs’ products since the new material was developed to require less training and additional equipment compared to other nylon 11 (PA11) materials on the market.
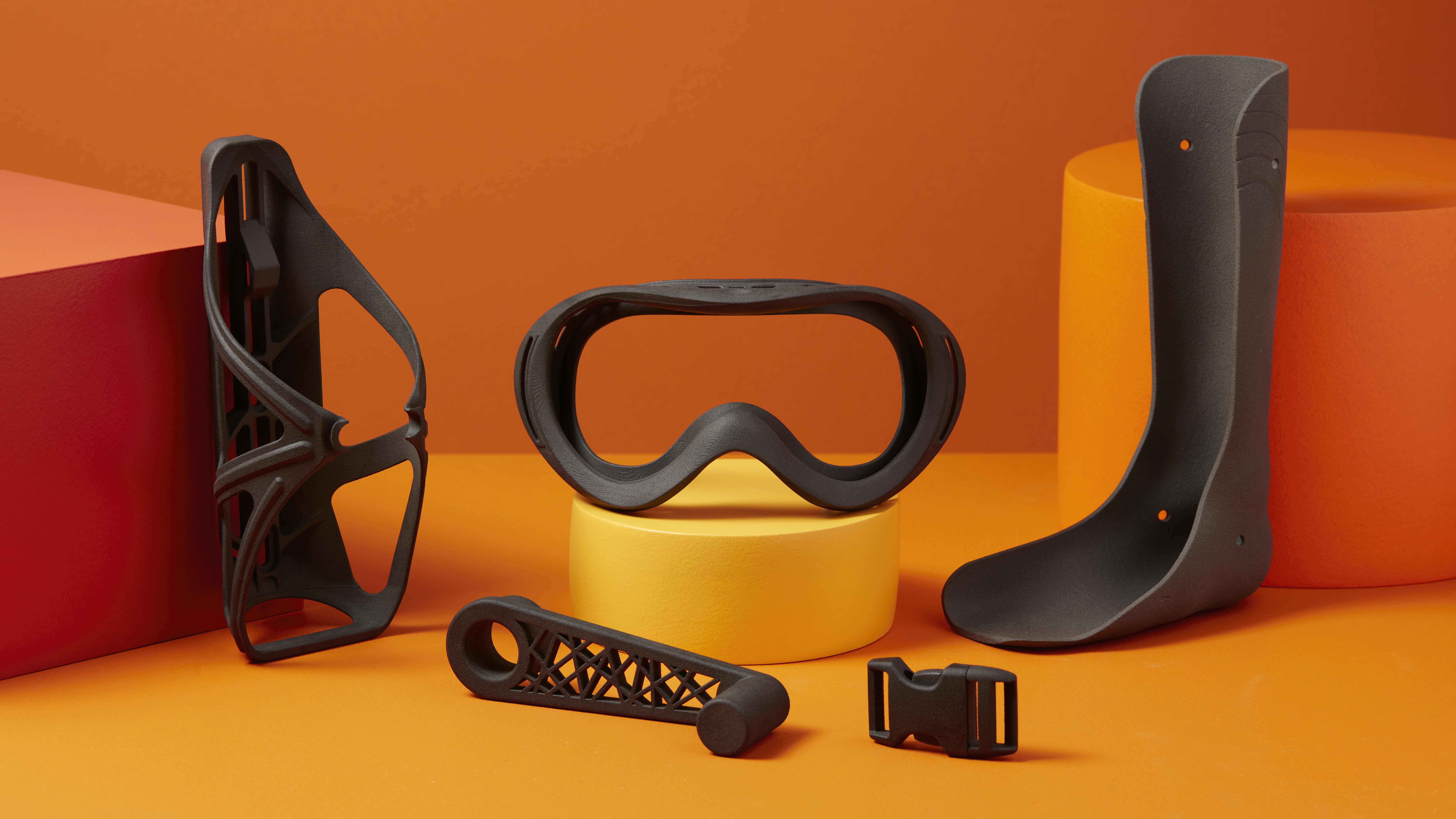
Formlabs’ new Nylon 11 powder for Fuse 1 SLS printer ideal for functional prototyping and small batch production. Image courtesy of Formlabs.
Ideal for creating end-use parts and functional prototypes like sports equipment, impact-resistant prototypes, thin-walled ducts and enclosures, robust jigs and fixtures, replacement parts, or prosthetics, the material promises ductile and strong qualities where durability and performance are essential. Seeking to expand the versatility of powder-based materials, the Nylon 11 Powder is one of many materials that Formlabs plans to launch for the Fuse 1, expecting to position it as the complete solution for end-use 3D printing. Now a multi-billion dollar company, Formlabs will use the funds, partnerships, and new product developments to continue growing and expanding its current portfolio to enable mass production and customization.
Subscribe to Our Email Newsletter
Stay up-to-date on all the latest news from the 3D printing industry and receive information and offers from third party vendors.
Print Services
Upload your 3D Models and get them printed quickly and efficiently.
You May Also Like
Nikon SLM Solutions Sells SLM 500 to Primary Weapon Systems to Expand Suppressor Production
Primary Weapons Systems (PWS) is a Boise, Idaho-based manufacturer of suppressors, firearms, and related components. A subsidiary of Vigilant Gear and a sister company to aftermarket Glock slide manufacturer Lone...
3DPOD 261: Tooling and Cooling for AM with Jason Murphy, NXC MFG
Jason Murphy´s NXC MFG (Next Chapter Manufacturing) is not a generalist service; instead, the company specializes in making tooling. Using LPBF and binder jet, the company produces some of the...
HP and Firestorm Labs Form Partnership to Use Multi Jet Fusion 3D Printers in Deployable Factories
HP Inc., maker of a range of additive manufacturing (AM) solutions including the Multi Jet Fusion (MJF) ecosystem, has announced a partnership with Firestorm Labs, a developer of containerized, deployable...
3D Printing News Briefs, July 2, 2025: Copper Alloys, Defense Manufacturing, & More
We’re starting off with metals in today’s 3D Printing News Briefs, as Farsoon has unveiled a large-scale AM solution for copper alloys, and Meltio used its wire-laser metal solution to...