We can wax poetic all day long about how 3D printing is a faster, more cost-effective method of manufacturing, but the fact remains that errors can still occur during the design and printing processes, which then costs more time and money. Volume Graphics GmbH, which has been a part of global sensor, software, and autonomous solutions provider Hexagon since 2020, develops software for non-destructive testing based on industrial CT scans, and customers from around the world in the automotive, aerospace, defense, and electronics industries utilize this software for quality assurance in both product development and production. The Heidelberg-based company just released the latest version of its CT data analysis software, which includes some pretty big updates to help detect and fix manufacturability issues and design flaws.
Some of the enhancements of this software update include a more user-friendly nominal/actual comparison module, which offers a simpler visualization of deviations of any scanned objects from their reference data sets. The software’s advanced reporting is also more user-friendly now, and is fully integrated with viewing.
Overall, the company’s software technology interprets CT data from scans taken of “almost any material” in order to detect, analyze, and visualize some of those small structural issues that could affect the quality of your parts. But version 3.5 of Volume Graphics’ software suite, which includes VGSTUDIO MAX, VGSTUDIO, VGMETROLOGY, VGinLINE, and myVGL, offers manufacturers of all kinds improved capabilities in inspecting parts and improving designs. It’s not just meant for 3D printing, but for casting and injection molding as well, and the updates are said to improve features like analysis and geometry repair of parts, usability, speed, and non-destructive testing accuracy.

A new compensation mesh color overlay in Volume Graphics’ industrial CT software version 3.5 helps users clearly visualize, analyze, and annotate any displacements in the compensation mesh.
Engineers, especially in automotive, aerospace, and defense sectors, who investigate novel materials and methods of manufacturing are more likely than ever to use CT scanning for a more accurate, non-destructive way to see how their part is performing. So Version 3.5 of Volume Graphics’ software should be a helpful tool for them, as it offers improved automated design-geometry adjustment and repair tools for offsetting and/or correcting any issues that arise from manufacturing. But the software isn’t just good for engineers—casting shops, moldmakers, and 3D printing providers can also get a lot of use out of it in finding and visualizing any design and material distortions or defects, and then comparing values against nominal limits, correcting the initial CAD design, and making sure that the quality of the final part meets any industry standards it may be up against.
The module for mesh compensation has been improved, which makes it easier for those working in 3D printing and simulation to navigate and understand how various elements work together, which then leads to enhanced interpretation of part deformation, displacement, and warping. Volume Graphics says that it’s now ten times faster to update mesh, and that this module offers better results when scan and reference objects have vastly different sizes or other major deviations. For more accurate, granular results, there are more control points, and Version 3.5 automatically compensates designs in order to correct for any deviations from the actual manufacturing intent. The module’s uniform control-point placement function also allows for full design analysis of complex geometries, such as lattice structures, and this updated software is also able to run two sequential design-compensation results automatically in order to move an AM design closer to nominal before it prints, which definitely could speed up the 3D print testing process.
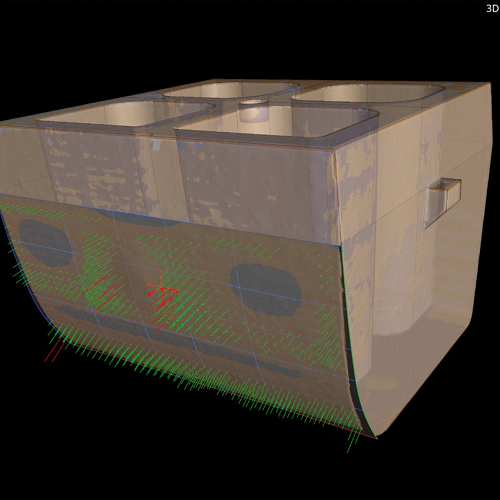
When compensating a geometry, a new filter option allows users to find fit points that cause inaccurate compensation results.
Another improvement is a totally reworked module for manufacturing geometry correction, which helps users working with molds. Volume Graphics says that CAD designers can improve manufacturability thanks to usability enhancements and quality feedback. Additionally, the software is supposedly able to filter out points that cause “erroneous compensation results,” which helps improve surface fitting and offer within-tolerance compensations, so users can quickly tell if their design changes will work with making molds.
Finally, one of the biggest features in Version 3.5 is new porosity and inclusion analysis of castings, as CT scans of cast parts can now be inspected for porosity, as well as compliance with Reference Sheet P 203 of the Federation of German Foundry Industry (BDG).
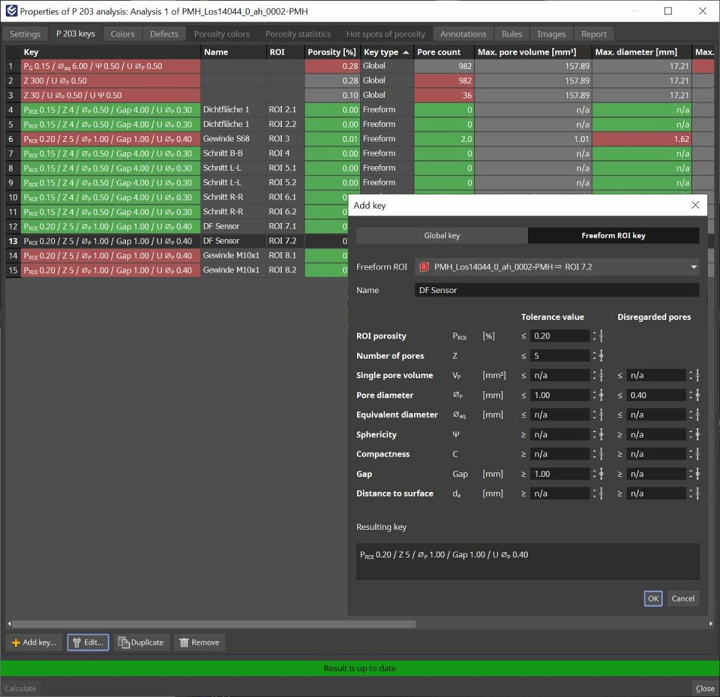
Usability improvements in the P 203 analysis include combining the generation and editing of global and freeform porosity keys in one dialog. A new BDG P 203 name field allows users to add a comment for each porosity key.
Using the new BDG P 203 porosity key, Volume Graphics says you can complete “a 3D evaluation of detected volume deficits” in freely defined sub-areas, like functional spaces with special qualities, as well as complete casting areas. Finally, Version 3.5 of the software makes it possible to analyze various regions of interest in a part in order to see if there are any post-machining issues and if porosity is within tolerances. Then, this data is ready for Q-DAS process control.
If you’re interested in an even deeper dive of the improvements and new features of Volume Graphics’ Version 3.5 software, the company is holding a demonstration webinar on Wednesday, May 26th. You can register for one of three time slots: 8 am CEST (2 am EST), 11 am CEST (5 am EST), or 5 pm CEST (11 am EST).
(Source/Images: Volume Graphics)
Subscribe to Our Email Newsletter
Stay up-to-date on all the latest news from the 3D printing industry and receive information and offers from third party vendors.
Print Services
Upload your 3D Models and get them printed quickly and efficiently.
You May Also Like
Nikon SLM Solutions Sells SLM 500 to Primary Weapon Systems to Expand Suppressor Production
Primary Weapons Systems (PWS) is a Boise, Idaho-based manufacturer of suppressors, firearms, and related components. A subsidiary of Vigilant Gear and a sister company to aftermarket Glock slide manufacturer Lone...
3DPOD 261: Tooling and Cooling for AM with Jason Murphy, NXC MFG
Jason Murphy´s NXC MFG (Next Chapter Manufacturing) is not a generalist service; instead, the company specializes in making tooling. Using LPBF and binder jet, the company produces some of the...
HP and Firestorm Labs Form Partnership to Use Multi Jet Fusion 3D Printers in Deployable Factories
HP Inc., maker of a range of additive manufacturing (AM) solutions including the Multi Jet Fusion (MJF) ecosystem, has announced a partnership with Firestorm Labs, a developer of containerized, deployable...
3D Printing News Briefs, July 2, 2025: Copper Alloys, Defense Manufacturing, & More
We’re starting off with metals in today’s 3D Printing News Briefs, as Farsoon has unveiled a large-scale AM solution for copper alloys, and Meltio used its wire-laser metal solution to...