Welding has been an integral part of manufacturing since the beginning of the 20th century. The development of technologies using electricity has made the most common arc welding methods—TIG, MIG, and stick welding—widespread in a variety of industries. All three of these arc welding methods rely on a consumable or non consumable electrode to join metals by either depositing melted metal or melting the target metals themselves. Arc welding is used in the automotive, construction, and aerospace industries.
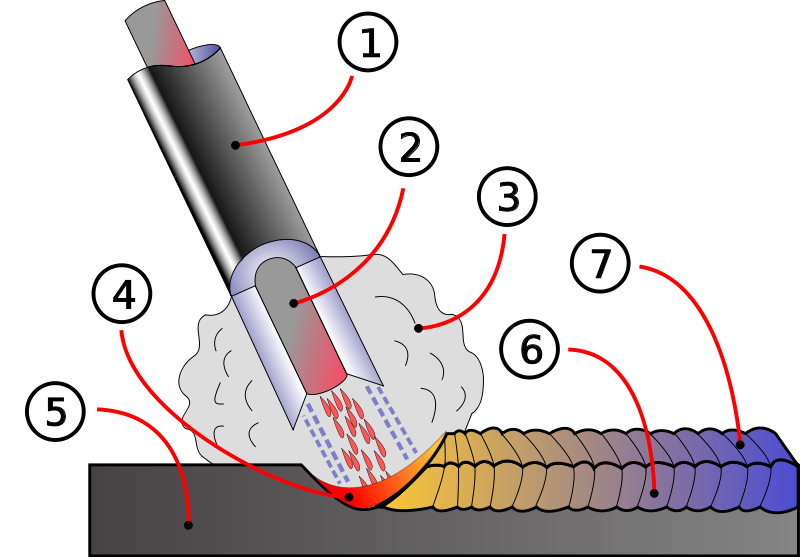
Figure 1. A stick welding diagram showing: 1. coating flow, 2. rod, 3. shield gas, 4. fusion, 5. base metal, 6. weld metal, and 7. solidified slag. Image available in the public domain.
Additive manufacturing (AM), however, is a much younger technology. Though early techniques were developed in the 1970s and 1980s, the potential of 3D printing was not fully realized until the 2010s. Initially, 3D printing was only used for making prototypes or low-fidelity models, but it has evolved to manufacture a variety of parts up to medical grade.
Welding and AM are thematically similar. MIG welding, in particular, is similar to 3D printing in that the metal electrode is deposited while welding. In fact, MIG welding has been used to additively manufacture metal objects by depositing metal layer-by-layer.
In this article, we will discuss how numerous techniques from welding can inform, improve, and innovate in the realm of 3D printing.
Controlling 3D Printing Microstructures
For welding, controlling the microstructure of the fusion zone is critical to creating a good weld. A badly formed microstructure can decrease mechanical resistance and/or result in unwanted anisotropy. There are several ways to tune the microstructure while welding, and some of these methods are transferable to 3D printing.
Welding microstructures can be controlled by heat source manipulation, chemical composition, and welding parameter calibration. Heat source manipulation is critical for both welding and 3D printing, since it directly affects how much material is deposited and/or melted. The heat source can be pulsed or continuous, and several different parameters can be controlled electronically; if pulsed, the magnitude, frequency, and duty cycle of the pulse can all be controlled.
These parameters directly transfer over to 3D printing. The nozzle depositing the plastic or metal is also controlled electronically, so the magnitude, frequency, and duty cycle can all be fine-tuned to achieve better material deposition. The movement speed of the heat source can also be tuned with greater precision in 3D printing than in manual welding, and the interplay of all of these parameters is critical for a good print.
In welding, the chemical composition of the electrode, gas, and filler are all critical. In fact, some reactive metals like aluminum and titanium cannot be welded using certain methods. Adjusting operating procedures also affects the end result; welding power, speed, and cooling must be orchestrated carefully. Each of these parameters affects how the microstructure of the fusion zone melts and solidifies.
Similarly for additive manufacturing, the choice of plastic or metal chemistry is vital; some polymers or alloys may not be printable, whereas others may be too soft to hold their structural integrity while printing. Additionally, the movement and heating of the nozzle must be adjusted for different materials, and these settings will affect the structural properties of the end product.
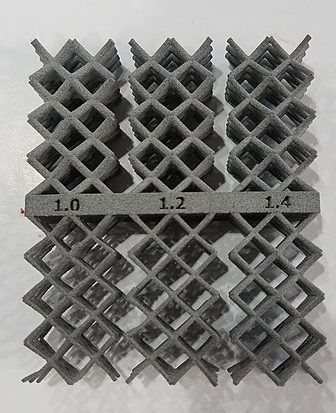
Figure 3. Varying a single 3D printing process parameter (lattice thickness) can result in significant property differences. Image courtesy of Wikimedia.
Parameter Optimization
The authors Oliveira et al. discuss a rigorous mathematical framework to determine AM parameters. In their paper, they hash out how to optimize process parameters such as power, movement speed, and hatch distance. There is no single value for each parameter that is the optimum, but rather there is an optimal parameter space where different combinations of parameters can yield the same defect-free result. For instance, simultaneously reducing power and movement speed would keep the heat input rate constant.
Oliveira et al. also discuss three different criteria to determine some critical quantities for 3D printing, namely hatch distance and melted radius. The hatch distance can be derived with a “geometric criterion” based on the melted radius, and the melted radius can be determined with either an energy or thermal criterion. They address their assumptions in deriving these criteria and provide diagrams and charts with experimental values.
Key Takeaways
Welding and AM are sister technologies. Welding is much older, so as it continues to be developed, we can transfer some of the lessons learned to 3D printing to avoid repeating the same mistakes. In particular, the microstructure at the weld/print site is of paramount importance to the end product, so care must be taken in tuning all relevant parameters like power, movement, and chemistry.
About the Author
Alex Saad-Falcon is a content writer for Do Supply Inc.. He is a published research engineer at an internationally acclaimed research institute, where he leads internal and sponsored projects. Alex has his MS in Electrical Engineering from Georgia Tech and is pursuing a PhD in machine learning.
Subscribe to Our Email Newsletter
Stay up-to-date on all the latest news from the 3D printing industry and receive information and offers from third party vendors.
Print Services
Upload your 3D Models and get them printed quickly and efficiently.
You May Also Like
Nikon SLM Solutions Sells SLM 500 to Primary Weapon Systems to Expand Suppressor Production
Primary Weapons Systems (PWS) is a Boise, Idaho-based manufacturer of suppressors, firearms, and related components. A subsidiary of Vigilant Gear and a sister company to aftermarket Glock slide manufacturer Lone...
3DPOD 261: Tooling and Cooling for AM with Jason Murphy, NXC MFG
Jason Murphy´s NXC MFG (Next Chapter Manufacturing) is not a generalist service; instead, the company specializes in making tooling. Using LPBF and binder jet, the company produces some of the...
HP and Firestorm Labs Form Partnership to Use Multi Jet Fusion 3D Printers in Deployable Factories
HP Inc., maker of a range of additive manufacturing (AM) solutions including the Multi Jet Fusion (MJF) ecosystem, has announced a partnership with Firestorm Labs, a developer of containerized, deployable...
3D Printing News Briefs, July 2, 2025: Copper Alloys, Defense Manufacturing, & More
We’re starting off with metals in today’s 3D Printing News Briefs, as Farsoon has unveiled a large-scale AM solution for copper alloys, and Meltio used its wire-laser metal solution to...