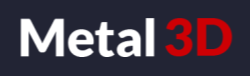
Metal 3D Co., Ltd., established in July 25, 2018, is a subsidiary of Winforsys, a metal 3D printing-based manufacturing company, and is composed of experts in each of the areas involved in the launch of its business activities. In October of the year immediately following its incorporation, it moved into the Ulsan Regional Headquarters as a partner company of Korea Institute of Industrial Technology (KITECH) and pursued joint research with Hyundai Heavy Industry for the optimization of metal 3D printing. As a result, the company completed registration as a cooperative company of Hyundai Construction Equipment in April 2019 and is currently manufacturing components used for heavy equipment under optimized procedural conditions.
In addition, the company conducts general education in metal 3D printing, including demand-linked programs as well as education customized for local industry at the Ulsan Korea Additive Manufacturing User Group (KAMUG), and has successfully held the Ulsan 3D Printing Skill Contest.
Metal 3D Co., Ltd. is planning to enhance its technological competitiveness by introducing medical titanium implant product s manufactured using Winforsys metal 3D printers. Metal 3D has a history of manufacturing implant packages for slipped disc patients in cooperation with KAMUG. The company is currently pursuing GMP approval and planning to expand aggressively into the medical device market by establishing a factory for metal 3D printing of medical implants.
In addition, Metal 3D Co., Ltd. has developed a mass production quality control system that enables optimization and quality control of the metal 3D printing process for mass production.
This product is a metal 3D printing package optimized for laminated products, and offers the advantage of an uploaded powder history management system, vacuum chamber technology, and process and quality control system, etc. to secure reliability and quality, which are the most critical elements of metal 3D printing.
Metal 3D printers use precision spherical power with high purity levels. However, given the characteristics of the process, it is possible that powder quality will degrade if recycling occurs more than 50 times. As such, there has been continuous demand for powder quality management in the industry.
In response, Metal 3D Co., Ltd. has enabled barcode-based history and storage quality management of the powder currently in use through its powder management system referred to as “Metalsys-Powder,” the first part of the company’s mass production quality control system.
Second, vacuum chamber technology has been applied to the metal 3D printer with the “Metalsys E Series” in SLM format, befitting its use in the manufacturing of medical equipment. It is therefore possible to process titanium in high-vacuum environments with this equipment while guaranteeing the safety of workers and the working environment through a built-in erroneous operation prevention module for the laser and application of an explosion prevention device for the chamber.
Third, although high quality control is essential for industrial and medical components given the characteristics of processed products, there are shortcomings with accurate quality control in the current X-Ray examination system due to issues of penetration and scattering during inspection of metal components. Accordingly, Metal 3D Co., Ltd. has developed “Metalsys-MPT (Melting Pool Tomography)”, which can guarantee the quality of the final product by inspecting the metal lamination process through continuous monitoring while the lamination-processed products are being manufactured.
Metal 3D
Address: Korea Institute of Industrial Technology (KITECH) 55 Jongga-ro, Jung-gu, Laboratory Building Room 307, Ulsan, Korea
Phone: 052-700-7730
Website : http://metal3d.co.kr
Subscribe to Our Email Newsletter
Stay up-to-date on all the latest news from the 3D printing industry and receive information and offers from third party vendors.
Print Services
Upload your 3D Models and get them printed quickly and efficiently.
You May Also Like
Consolidation in AM: How 2025 Is Shaping the Industry’s New Normal
The first half of 2025 has been marked by a clear shift in the additive manufacturing (AM) industry. Companies are no longer just focused on developing new tech by themselves....
Heating Up: 3D Systems’ Scott Green Discusses 3D Printing’s Potential in the Data Center Industry
The relentless rise of NVIDIA, the steadily increasing pledges of major private and public investments in national infrastructure projects around the world, and the general cultural obsession with AI have...
3DPOD 260: John Hart on VulcanForms, MIT, Desktop Metal and More
John Hart is a Professor at MIT; he´s also the director of the Laboratory for Manufacturing and Productivity as well as the director of the Center for Advanced Production Technologies....
Making Space: Stratasys Global Director of Aerospace & Defense Conrad Smith Discusses the Space Supply Chain Council
Of all the many verticals that have been significant additive manufacturing (AM) adopters, few have been more deeply influenced by the incorporation of AM into their workflows than the space...