The United States Department of Defense (DoD)’s combat logistics support, the Defense Logistics Agency (DLA), has awarded a Phase two Small Business Innovation Research (SBIR) program to 6K, a leading developer of microwave plasma technology for advanced materials engineering, and its business division 6K Additive. The near $1 million award will support 6K’s development and commercialization of high-performance metal powders for additive manufacturing (AM) from scrap sources. Looking to reduce the extraction of raw metals by recycling material closer to its users, 6K is sustainably turning scrap metal, shavings, used parts, and even used powders into high-quality metal powder. The new materials will be applied towards additively manufacturing real-world, discrete printed parts that will demonstrate functionality in testbeds or systems.
Using 6K’s proprietary UniMelt microwave plasma platform, the program will demonstrate the company’s capability to source, process, and reclaim nickel superalloy scrap components, shop scrap, and used powders for conversion into aerospace-grade powders. The UniMelt production system is capable of converting high-value metal scrap of numerous forms into high-performance metal powders for AM, metal injection molding, and other powder metallurgy production techniques.
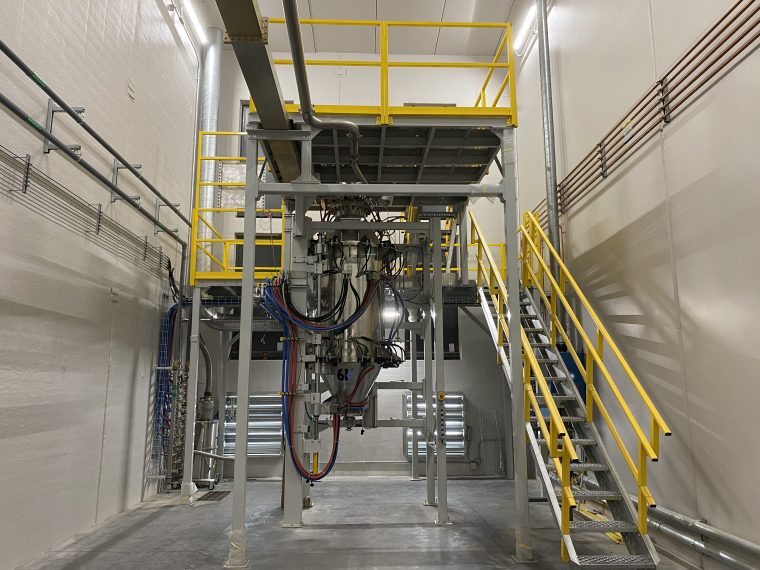
6K’s UniMelt microwave plasma recycles feedstock into premium AM-ready metal powder. Image courtesy of 6K.
The technology is critical because it provides access to a vast domestic supply of strategically important metals and alloys such as nickel and titanium from machine shops, boneyards, and sources of other used materials that are required by the DLA’s military personnel throughout the world. 6K intends to offer the US military a secure, traceable domestic supply of critical materials while eliminating unexpected performance anomalies due to questionable sourcing from foreign supply.
According to the company, its patented process cleans, prepares, and spheroidizes scrap alloys into high-quality powders with superior performance to metal atomization technologies. The 6K Additive team is already processing and selling over 500 tons of titanium alloy spherical powder Ti-64 per year into the aluminum alloying industry for aerospace, medical, and automotive production. The business’s ability to reclaim materials and process almost any type of metal, alloy, or ceramic feedstock into premium powders means it can even create new AM powders previously not possible.
“As a company, we are certainly pleased with the award, but more importantly, we’re proud as an organization to help our country create and control a domestic supply for alloys such as nickel used for emerging production methods like additive manufacturing,” described Aaron Bent, CEO of 6K. “The recent COVID-19 pandemic highlights the importance of controlling the supply chain and the renewed need for domestic production to avoid interruption of critical supplies.”
AM technology is already considered to be environmentally friendly when compared to conventional manufacturing processes. Metal AM in particular reduces the overall amount of metal materials consumed compared to traditional machining. Still, there is a growing demand for sustainable feedstock. As virgin metals become increasingly difficult to mine and carry associated environmental costs, leveraging technology to recycle scrap reduces pollution and waste, saves resources, and prevents the destruction of habitats from mining new ore. In the US alone, the recycling of scrap metal is a $32 billion business – according to the latest IBIS World report – that uses at least 50% less energy than mining new metal and contributes to the country’s circular economy.
In line with this, creating a closed-loop supply chain where certified scrap materials are turned into powder by 6K, which can then be additively manufactured, sounds like an ideal solution for the DoD. Especially since metal powder superalloys are used in critical propulsion and heat mitigation components in the hottest, most corrosive, most demanding components in aircraft and rocket engines, gas turbines, oil and gas equipment, and heat exchangers. Having a control system can enhance security and reduce the risk of dependence on foreign supply, even avoiding any unexpected performance anomalies due to questionable sourcing about the quality and consistency of foreign-sourced materials.
According to 6K, there is a constrained domestic availability of strategic metals such as superalloys, so utilizing materials from the nation’s boneyards and machine shops to convert into high-quality materials provides the US military with a secure domestic supply of critical metal. Moreover, there is a chance to recycle previously qualified DoD parts, shop scrap, and used powders that result in material quality that is known and traceable.
The Massachusetts-based company also revealed that it has worked with several members of Congress to gain support for the company’s efforts in utilizing defense scrap material as feedstock for the UniMelt process, in support of reducing the dependence on foreign supply. 6K considers that using already certified scrap as raw material dramatically reduces the material cost of goods for manufactured parts and ensures they meet the desired specification. Powders from scrap will leverage DoD investments by reducing the cost of end-system part production with a compelling rate of return.
“Southwestern Pennsylvania’s job creators, innovators, and hardworking employees are critical to our national defense and efforts to provide vital resources to our warfighters. I was proud to secure funding to reduce dependence on foreign titanium and utilize American ingenuity to protect our national security,” said Pennsylvania Congressman Guy Reschenthaler about 6K’s sustainable metal recycling efforts.
Furthermore, in early September 2020, the representative introduced a bill to amend the Internal Revenue Code of 1986 to permanently allow a tax deduction for investments in property used for mining, reclaiming, or recycling of critical minerals and metals from deposits in the United States. If the bill passes, companies like 6K will certainly benefit from a tax deduction for sustainably recycling metal scrap. Particularly, since 6K has recently commissioned the first two commercial UniMelt systems for its new 40,000 square foot state-of-the-art metal powder production facility on the company’s 45-acre site at Burgettstown, Pennsylvania. The new facility, which is said to be near 100% completion, is expected to develop, commercialize and begin shipping traditional powder products in the fall of 2020.
Both the UniMelt process and high-quality materials are expected to help the DoD develop and adopt advanced AM, metal injection molding, and powder forging processes more quickly, creating parts with totally novel functionality, reducing engineering cycles, and accelerating “make-to-fly” cycles. Creating a circular economy to turn manufacturing scrap into usable metal powder for AM, can reduce virgin metal production by recycling existing material closer to its source, decreasing the environmental footprint.
Subscribe to Our Email Newsletter
Stay up-to-date on all the latest news from the 3D printing industry and receive information and offers from third party vendors.
Print Services
Upload your 3D Models and get them printed quickly and efficiently.
You May Also Like
Nikon SLM Solutions Sells SLM 500 to Primary Weapon Systems to Expand Suppressor Production
Primary Weapons Systems (PWS) is a Boise, Idaho-based manufacturer of suppressors, firearms, and related components. A subsidiary of Vigilant Gear and a sister company to aftermarket Glock slide manufacturer Lone...
3DPOD 261: Tooling and Cooling for AM with Jason Murphy, NXC MFG
Jason Murphy´s NXC MFG (Next Chapter Manufacturing) is not a generalist service; instead, the company specializes in making tooling. Using LPBF and binder jet, the company produces some of the...
HP and Firestorm Labs Form Partnership to Use Multi Jet Fusion 3D Printers in Deployable Factories
HP Inc., maker of a range of additive manufacturing (AM) solutions including the Multi Jet Fusion (MJF) ecosystem, has announced a partnership with Firestorm Labs, a developer of containerized, deployable...
3D Printing News Briefs, July 2, 2025: Copper Alloys, Defense Manufacturing, & More
We’re starting off with metals in today’s 3D Printing News Briefs, as Farsoon has unveiled a large-scale AM solution for copper alloys, and Meltio used its wire-laser metal solution to...