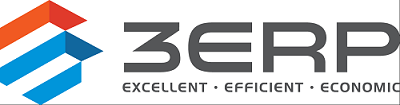
Injection molding is typically described as a cost-effective manufacturing process… when ordering large quantities of parts.
The reason for this is simple: with injection molding, the initial tooling costs are very high, while the actual plastic molding costs are very low, which means the effective cost-per-unit becomes lower when more units are required.
For example, imagine that a stainless steel mold for a toy car costs $5,000, and each plastic toy car made with the mold costs $0.50. In this scenario, ordering 1x unit of the toy car would cost $5,000.50, ordering 2x units would cost $5,001, and ordering 1,000x units would cost $5,500.
In all of the scenarios, the mold accounts for the bulk of the cost, so the total cost does not vary greatly.
However, in these three scenarios, the effective cost-per-unit does vary greatly:
Scenario in which mold costs $5,000 and each molded part costs $0.50 | ||
Units | Total cost ($) | Cost-per-unit ($) |
1 | 5,000.50 | 5,000.50 |
2 | 5,001.00 | 2,500.50 |
1,000 | 5,500.00 | 5.50 |
As you can see, there is a dramatic reduction in cost-per-unit when the unit quantity increases, since the extra units amortize the high cost of the mold.
Ordering more units of the toy car clearly represents better value for money. (In fact, ordering a single unit would appear to be a colossal waste of money.)
But just how “large” do we mean when we say that injection molding is suited to large quantities of parts? 100? 1,000? 10,000? A million? As a company deciding between multiple manufacturing processes for a medium-size order of prototypes or end-use parts, we want to know at what point injection molding becomes more cost-effective than the alternatives such as 3D printing.
And while there is no simple formula for determining the point at which injection molding becomes more cost-effective than 3D printing, there are certain factors we can take into account that will help us make the right decision.
3ERP, an expert in injection molding and other on-demand manufacturing services, here provides advice on choosing between injection molding 3D printing based on the required order size.
Injection molding vs 3D printing: First considerations
For companies looking to complete prototyping or production of plastic parts, both injection and 3D printing may seem like tempting options, and it may seem hard to weigh up the respective benefits of each.
However, before getting into any precise calculations, it’s worth pointing out some situations where one manufacturing process is clearly preferable to the other.
Let’s start with a scenario in which a company needs a very small number of prototypes (perhaps just one), and the material and aesthetic properties of the prototype(s) are of negligible importance. Perhaps the in-house R&D team simply wants to see, very loosely, how a yellow plastic casing looks on its new electronic device.
In such a scenario, 3D printing would be the obviously preferable choice: it would be significantly cheaper, and any technical deficiencies in the prototype would not matter.
Alternatively, imagine a scenario in which just a handful of prototypes (perhaps just one) are needed, but the company is looking to pitch its product to an investor, who needs to be convinced that the end-use part (to be made with injection molding during mass production) will function properly for its intended purpose.
In such a scenario, while 3D printing the prototype may be cheaper, it might still be worthwhile for the company to create an injection molded prototype in order to demonstrate the viability of its end-use product.
Key economic differences between injection molding & 3D printing
It is difficult to compare the costs of injection molding and 3D printing because the processes are fundamentally different — not just in terms of how they work, but in how their respective costs are determined.
In general terms, injection molding is a process with high startup costs: metal molds are expensive to make, and that preliminary step can be an insurmountable hurdle for some small businesses. However, once a mold has been fabricated, the cost of each injected “shot” of plastic is very low.
3D printing is different because, unlike injection molding, it is a one-step process. No tooling is needed, and the finished part comes straight out of the printer. This means there are no obstructive startup costs.
That being said, the cost of a single plastic 3D printed part is generally higher than a shot of injected plastic. This is because 3D printing filament (for FDM printers) is more expensive than plastic pellets, and because the sheer slowness of 3D printers means that service providers must charge more for their operation.
With that in mind, the most importance difference between the two processes is that the cost-per-unit of injection molding is dynamic: it decreases as the number of units increases. With 3D printing, on the other hand, the cost-per-unit is static: parts will usually cost the same amount whether you order one or 1,000 of them.
This means that 3D printing in small quantities is cheaper than injection molding, while injection molding in large quantities is cheaper than 3D printing. That also means, logically, that there is some specific quantity at which the “best value” option switches from 3D printing to injection molding.
Finding that quantity depends on several factors.
How many parts to be cost-effective: Factors to consider
The mold
When evaluating the potential costs of injection molding and 3D printing, it is worth starting with potentially the most expensive part of the project: the mold.
Molds can cost thousands of dollars, since they are machined from metal and need to last a long time — potentially hundreds of thousands of plastic shots. However, it is possible to drastically reduce the cost of molds through rapid tooling, the creation of prototype-grade molds with CNC machines or metal 3D printers.
The cost of molds can also be reduced by using aluminum instead of steel. Aluminum is less durable than tool steel, but is still capable of producing high-quality molded parts from non-corrosive materials.
If the cost of the mold can be reduced, the number of molded parts required to be cost-effective decreases.
As an example, imagine that a steel mold for a toy car costs $5,000, that an aluminum mold costs $1,000, and that the cost per plastic shot with either mold is $0.50. Imagine, also, that a 3D printed version of the toy car costs $20.
In this example, the potential costs of the project would be as follows:
Steel mold IM | Aluminum mold IM | 3D printing | ||||
Units | Total cost ($) | Cost-per-unit ($) | Total cost ($) | Cost-per-unit ($) | Total cost ($) | Cost-per-unit ($) |
1 | 5,000.50 | 5,000.50 | 1,000.50 | 1,000.50 | 20 | 20 |
2 | 5,001.00 | 2,500.50 | 1,001 | 500.50 | 40 | 20 |
50 | 5,025.00 | 100.50 | 1,025 | 20.50 | 1,000 | 20 |
60 | 5,030.00 | 83.83 | 1,030 | 17.17 | 1,200 | 20 |
300 | 5,150.00 | 17.17 | 1,150 | 3.83 | 6,000 | 20 |
In this scenario, a 50-unit order is cheaper with 3D printing, but a 60-unit order is cheaper using injection molding with an aluminum mold. (Meanwhile, the more expensive steel mold becomes more cost-effective than 3D printing just above the 250-unit mark.)
Plastics
Another consideration that will affect the calculation is the plastic used to make the part, and there are several variables to consider here.
One factor to consider is that not all 3D printable plastics are moldable, and vice versa. Another is that 3D printing filament is by and large, more expensive than the plastic pellets used for injection molding, since it must be precisely shaped by the material manufacturer.
Importantly, the cost of plastics may not be consistent between pellet and filament formats: materials like Nylon and Polycarbonate, for example, remain relatively premium products in the 3D printing filament market, so a relatively small number of Nylon parts would be required to make injection molding more cost-effective than 3D printing. (A common 3D printing material like ABS, however, would require a much larger number.)
The type of plastic used to make the parts may therefore determine which manufacturing process is more economical for a given order volume.
Part shape and size
The design of the part may also affect its potential cost for injection molding and 3D printing. A part with overhangs, for example, may be significantly cheaper to 3D print, since injection molded parts with overhangs require more complex tooling.
In other words, if your part design is not suited to injection molding, you’ll probably need to order more parts to make injection molding cost-effective.
Manufacturing process
FDM remains the most common 3D printing process, but alternative options include Stereolithography and Selective Laser Sintering. These other processes are more expensive than FDM, which naturally affects their affordability in comparison with injection molding.
For example, 200 FDM parts may be cheaper than 200 equivalent injection molded parts, but 200 SLS parts may be more expensive than 200 injection molded parts.
Conclusion
Since the cost-per-unit of plastic parts is dynamic for injection molding and static for 3D printing, it can be difficult to assess which option is the best value for money for a given order.
Numerous factors, including mold creation, part material and part shape can affect the cost of the order — and to different degrees depending on the manufacturing process.
With that in mind, the best solution to the dilemma may be simply requesting a quote for both processes.
3ERP has expertise in both injection molding and 3D printing, and can assess projects on a case-by-case basis to see which represents the best value for money.
Get in touch and we’ll get your project up and running.
Subscribe to Our Email Newsletter
Stay up-to-date on all the latest news from the 3D printing industry and receive information and offers from third party vendors.
Print Services
Upload your 3D Models and get them printed quickly and efficiently.
You May Also Like
Nikon SLM Solutions Sells SLM 500 to Primary Weapon Systems to Expand Suppressor Production
Primary Weapons Systems (PWS) is a Boise, Idaho-based manufacturer of suppressors, firearms, and related components. A subsidiary of Vigilant Gear and a sister company to aftermarket Glock slide manufacturer Lone...
3DPOD 261: Tooling and Cooling for AM with Jason Murphy, NXC MFG
Jason Murphy´s NXC MFG (Next Chapter Manufacturing) is not a generalist service; instead, the company specializes in making tooling. Using LPBF and binder jet, the company produces some of the...
HP and Firestorm Labs Form Partnership to Use Multi Jet Fusion 3D Printers in Deployable Factories
HP Inc., maker of a range of additive manufacturing (AM) solutions including the Multi Jet Fusion (MJF) ecosystem, has announced a partnership with Firestorm Labs, a developer of containerized, deployable...
3D Printing News Briefs, July 2, 2025: Copper Alloys, Defense Manufacturing, & More
We’re starting off with metals in today’s 3D Printing News Briefs, as Farsoon has unveiled a large-scale AM solution for copper alloys, and Meltio used its wire-laser metal solution to...