Twelve years ago I was at a conference and the only thing we could all agree on was that SLA was dead. Intrinsicly expensive, dangerous, and without options to automate post-processing, but with limitations in heat deflection and strength, this was a technology without a future. A few years later, when I heard from a friend that Fab@Home‘s brilliant Max Lobovsky was working on an SLA machine, my response was, “but, why?” My my how the world can change, it wasn’t a black but rather an orange swan. SLA/DLP and other similar vat polymerization technologies are expanding now, machines are getting cheaper and we’re in the midst of a stereolithography renaissance. But, who will be its king?
In the riotous hyper-competitive world of FDM (material extrusion, please stop saying FFF) there are many material suppliers. Most of the large polymer companies worldwide have joined the market, along with many compounders, startups and extrusion companies. This means that in the FDM world you are spoilt for choice. Prices have been reduced, while R&D work has lead to the development of many new and improved materials. Most readily extrudable thermoplastics are now available in filament form. For the home user, this has meant an expanded menu of options for you when contemplating your next project or print. On the industrial side, more polymers mean that more companies can use the materials that they are familiar with for prototypes and production. The open FDM world has made manufacturing in 3D printing more likely, especially since a lack of lock-in means less reliance on one supplier and more resilience in your supply chain. Lower prices and more selection are obviously going to lead to higher demand and yet much of our industry is still firmly locked in. Right now in FDM, from the depths of Ali Baba caverns, we’re actually ascending in price and quality towards a world of pricier but more dependable branded filaments from a large selection of suppliers.
The closed lock in FDM world is not completely forlorn or lost, however. In a prototyping arena having one material that is perfectly tied to one printer may actually be desirable. After all, you want your prints to work, and now you can select from a limited but always functional library of materials. Limited but “works every time” is in that case much more preferable to spending a few valuable days dialing in a material. But, if we move towards production, higher prices won’t withstand manufacturing level attention from procurement. It doesn’t help either that, for example. a car company does kind of already buy a lot of ABS, and not for $140 or $40 a kilo either. We can pull the wool over the muggles’ eyes if we’re a line item in R&D or a Design Center, but not if we want to bask in the red light glow of the factory floor. If we wish to transition from carpet to concrete, low cost and wide selection will be key.
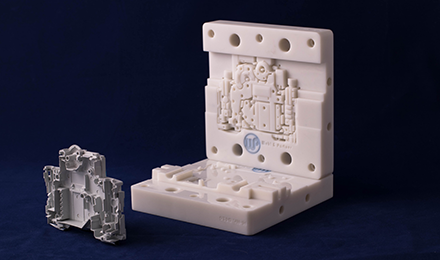
DSM Somos PerForm part
In the stereolithography and DLP world, we’ve of course always had DSM Somos and Arkema’s Sartomer that have sold materials to open SLA vendors across the world. Many machines are or have been open. Exotic chemistry has allowed much of the SLA world to remain quite closed, however. And yes, a lot of manufacturing has been occurring in SLA/DLP, with tens of millions of hearing aids, tens of millions of lost wax cast jewelry intermediates, millions of molds for Invisalign, and millions of more dental parts being made per year. Actually, in sheer numbers of parts, SLA/DLP if taken together probably accounts for more end-use parts than other technologies. Yet, liter prices for photopolymer resin still stay around the $99 to $800. This is 250% higher at least than it needs to be.
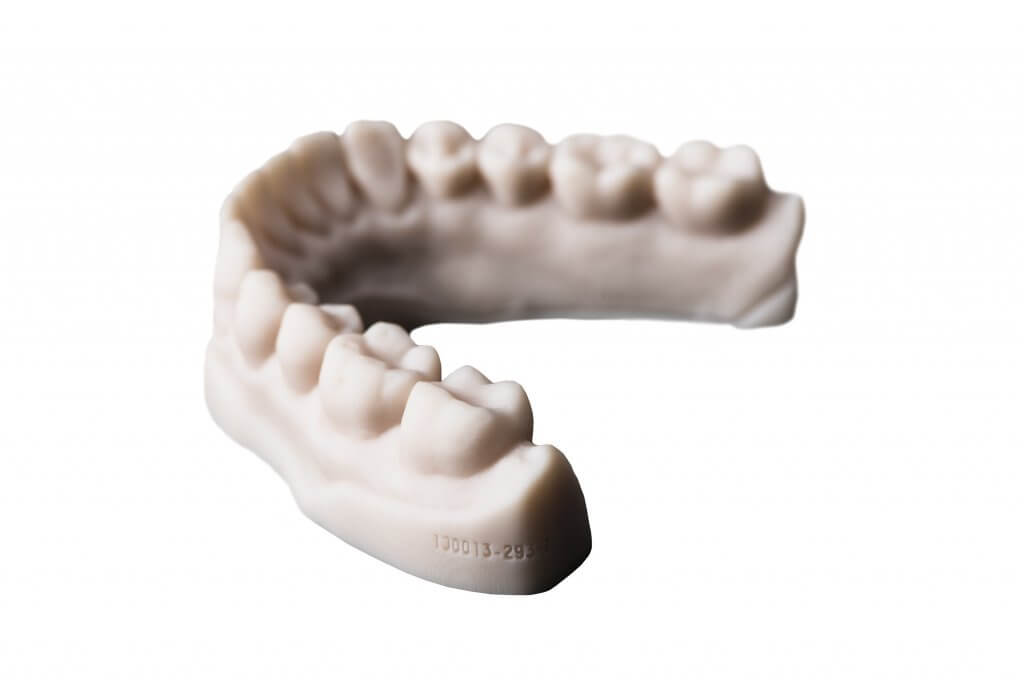
A Sartomer Carbon part
In highly regulated fields people don’t mind paying more for a material that is ensured to work and meet standards. Things like hearing aids and dental have their strict requirements and are typically also made by conservative as well as safety-conscious industries. Crucially the parts are very small as well. Hearing aid shells are tiny things that use only a few milliliters of material. If you can make 200 hearing aids from one liter, then it can be expensive per liter and you won’t even notice. This is especially the case if support removal by hand clouds the cost picture further by often being much more expensive than the part cost itself. The combination of high manual labor cost, small parts, and safety-conscious users has kept a vibrant industry for resins well fed. A focus on high-value applications also insulates photopolymer manufactures from the pressures of the wider market.
At the same time process limitations, have in certain cases kept SLA/DLP part sizes small. For some platforms and wavelengths random things such as the output strength and size of commercial projectors from companies such as Epson, have limited progress. It is still today rather hard to make orange sized parts on many orange vat polymerization machines. Research into LED and other light sources, as well as increased R&D efforts by many firms and researchers into SLA/DLP and mSLA, will advance these technologies, however. Carbon, Formlabs, and indeed before that, 3D Systems acquisitiveness and momentum have ensured that SLA has been supplied with cash and interest. Yet even though Formlabs lets you put in your resin of choice, most new startups are firmly closed, locking you into their materials. Indeed Formlabs even acquired its materials supplier Spectra, making the case for further vertical integration and coordination. Origin is open, as is Atum3D, but most investment activity is focused on the “razor plus blades” type firms.
In FDM we’ve got hundreds of materials suppliers, but in SLA/DLP we see very few. Quick, name a brand of desktop SLA resin? Name three? We’re seeing quite the light-based renaissance, but the materials world remains very vendor-specific. Mitsubishi has moved in with some activity and BASF now sells resins but overall, especially on the consumer front, activity has been minimal.
Meanwhile, there are hundreds of photopolymer companies selling resins, mostly in Asia. Catering to the jewelry market mostly. In their world regulation and safety are low priorities but they do a brisk business anyhow. Low safety Asian photopolymer sales are still one of my biggest worries in 3D printing. I believe this to be a near existential risk for SLA as a technology, I see many potential issues with cancers and skin sensitization when people make and sell resins without much care. Experience has thought us that from within that maelstrom we will get one or two credible safety-conscious firms who do want to reputably expand worldwide and go upmarket, however.
This likelihood of opportunity has been aided by the rapid expansion of lower-cost industrial SLA equipment from Chinese and Korean firms that has briskly expanded across the word’s manufacturing base. I missed this trend entirely until only a year ago a local 3D printing expert pointed it out to me. Sindoh, Carima, Graphy, Kings, who will expand globally? Thousands of new industrial SLA machines are being sold each year throughout the region. Largely unseen now, new giants are emerging that will challenge preexisting OEMs. At the same time, consumer SLA has been heating up. Creality now offers a $269 resin printer while Elgoo, Longer3D, and others all have low-cost offerings. Formlabs has expanded its premium product line while squarely in between those extremes, we can find Prusa3D with their $1600 open source SLA system.
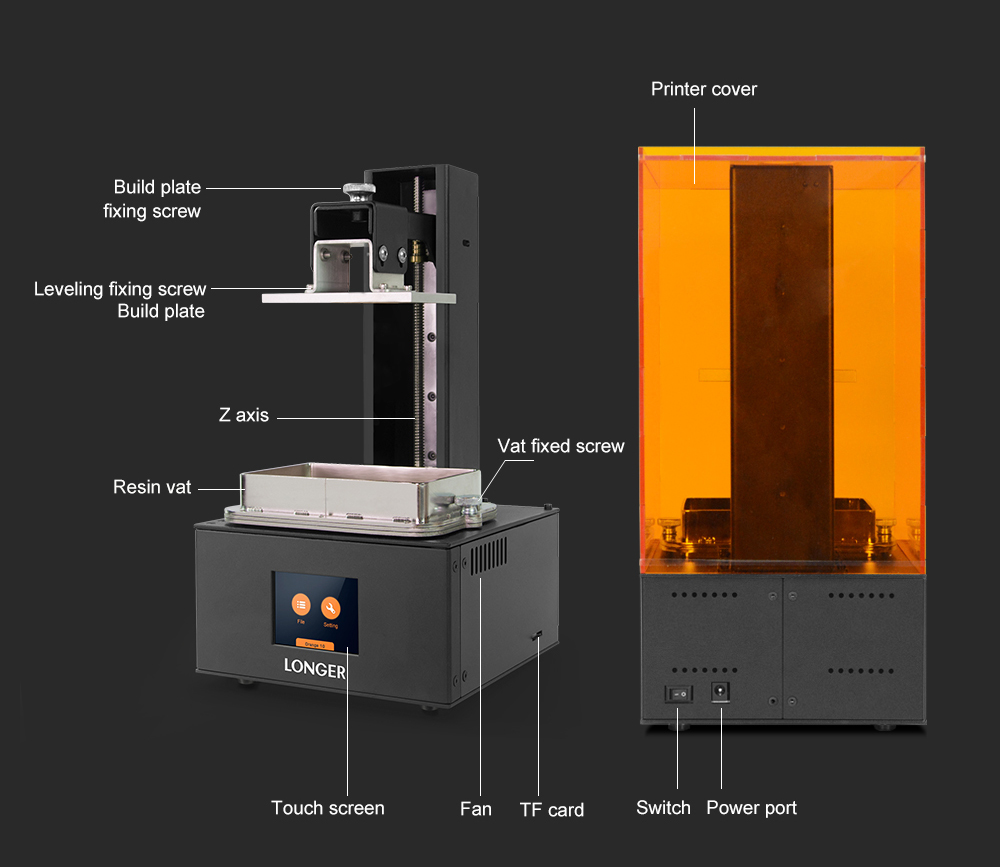
Count the parts.
Between the fleshing out of “at every price point” line of 3D printers and industrial expansion in SLA systems, there is a huge opportunity emerging in SLA materials. OEM competition will be incredibly fierce, this will be exacerbated by the fact that assembly costs are relatively low in SLA systems. Certain components (light source and Z motion stage) have to be expensive and high quality, but once you have those the rest of the system consists of relatively few parts, which are also relatively low cost. In high quality industrial and Pro, margins may remain because people will pay for service, brand, and uptime; but for those not squarely nestled in the Pro or high-end manufacturing segment, times will be tough. Generally, however, we would expect increased pressure on margins as well as competitiveness across all price points in SLA from within a growing installed base of SLA systems. There is, even with many new offerings, a huge gap in segments from Pro to $15,000 systems and then another huge gap between these systems and Perfactories with yet another gap between them and iPro’s. This is a market you could drive a 10,000 unit selling OEM through and no one would even know that they existed.
With SLA expanding quickly, we can see an established high-cost resin market in regulated industries that will to a certain extent remain insulated from pricing pressure. Other segments including manufacturing will face increased competitive forces. Meanwhile, it is clear that a significant opportunity is emerging, what’s more, this opportunity is largely unmet. We have low-cost resin (and this only to a certain extent) of dubious quality and high-cost high margin resin for the dental labs et al, but what of the rest of the market? There is currently no visible globally available branded photopolymer that is safe, known and affordable.
On the consumer market, there is hardly anyone with any brand recognition in resin what so ever. MakerJuice? Who else? Meanwhile, in industrial, there is no brand positioning equivalent of Volkswagen in the resin market, only Audi’s. The low-cost segment, the general industrial segment, and the consumer segments specifically are growing quickly but there is no brand to cater to these segments with an adequate value proposition. Recently Italian OEM DWS released OpenDWS which is its initiative in trying to sell resin to the broader market. Selling to a captive audience may seem like a good business but not if the other guy sells to his and your audience at the same time.
I don’t believe that there can be an OEM winner takes all situation. There are simply too many niches and technologies for one winner to happen. Similarly, in FDM materials, base polymer/monomer synthesis and the manufacturing of those materials mean that per polymer, some companies have cost advantages. Good luck trying to make cheaper ABS than Sabic for example. But, ABS will not work for everyone in all cases. Also, people will ask for and want a particular polymer whether you make it or not. Different go to market models have also meant that “winner takes all” is very unlikely at this point in FDM.
SLA/DLP material to me is a different matter. Here I can see that the level of branding, market penetration, and availability is so low as that there can still emerge one “winner takes all” in SLA materials. With one photopolymer manufacturing chain moreover, a lot of the market needs can be addressed with one or at least a few materials. All the photopolymers are exotic to manufacturers, so they don’t come to you with a need for a certain PC grade, a wish to use 12 different materials, or a desire to keep manufacturing in POM. You see in thermoplastic filaments the fit for purpose of the polymer to the application, or previous experience/regulatory is key, along with the cost of the material. You seek the right polymer for the application. In filaments, you have a puzzle and you seek the puzzle piece to complete it. With SLA you know you have the wrong material at the wrong price point from the get-go. Furthermore, you know you’ll never get the right material that will behave in the same way as you’re used to. With SLA you’ll always be puzzled.
But, what is the SLA/DLP materials market then? To me its a pure safety play. Anyone that has a more or less application fit solution that leads you to believe that they have the highest safety standards and safest material for your users and is marginally more cost-effective will prevail.
To me, this means that there is currently a huge opportunity for a materials supplier to become the default and by far the largest supplier of SLA materials. What’s more, they could leverage throughput, distribution, and brand to dominate the market. Scale, capacity/throughput on manufacturing, high fixed costs/investment to get safe materials, mean that it is clear that one player could dominate. Looking at SLA/DLP materials as some kind of raw materials/polymer or a “solutions” kind of market is in my mind, not the right perception. This isn’t a value-based pricing or features thing at all to me. To me, this market is like aero engines, seat belts, MRI scanners or sushi restaurants. Feel free to perform every time, fail only once. SLA materials seem most similar to orthopedic implants to me, a few careful big players with burdens to shoulder and some innovative minnows on their way to being lunch.
To me, this opportunity in SLA materials is wide open and is ill addressed at this moment. Who will meet the needs of OEMs, consumers, and manufacturers in this expanding materials space? What do you think, which company will become the largest supplier of SLA resins? Who will survive and thrive?
Subscribe to Our Email Newsletter
Stay up-to-date on all the latest news from the 3D printing industry and receive information and offers from third party vendors.
Print Services
Upload your 3D Models and get them printed quickly and efficiently.
You May Also Like
Nikon SLM Solutions Sells SLM 500 to Primary Weapon Systems to Expand Suppressor Production
Primary Weapons Systems (PWS) is a Boise, Idaho-based manufacturer of suppressors, firearms, and related components. A subsidiary of Vigilant Gear and a sister company to aftermarket Glock slide manufacturer Lone...
3DPOD 261: Tooling and Cooling for AM with Jason Murphy, NXC MFG
Jason Murphy´s NXC MFG (Next Chapter Manufacturing) is not a generalist service; instead, the company specializes in making tooling. Using LPBF and binder jet, the company produces some of the...
HP and Firestorm Labs Form Partnership to Use Multi Jet Fusion 3D Printers in Deployable Factories
HP Inc., maker of a range of additive manufacturing (AM) solutions including the Multi Jet Fusion (MJF) ecosystem, has announced a partnership with Firestorm Labs, a developer of containerized, deployable...
3D Printing News Briefs, July 2, 2025: Copper Alloys, Defense Manufacturing, & More
We’re starting off with metals in today’s 3D Printing News Briefs, as Farsoon has unveiled a large-scale AM solution for copper alloys, and Meltio used its wire-laser metal solution to...