Researchers are studying the use of new materials for greater strength in 3D printing, outlining their findings in the recently published ‘Zeolite-templated 3D printed carbon nanotube networks with enhanced mechanical properties.’ Greater knowledge in this area is especially critical for applications like aerospace and defense where high load-bearing architectures are often required, leading the authors to seek inspiration from nature, in the form of microporous minerals known as zeolite.
As materials science expands, so does the use of composites—additives used to enhance materials that may be otherwise limited for manufacturing certain projects. Scientists often draw from nature, whether from spider silk, wood, seashells, or a variety of other materials that can translate into other forms meant to improve manufacturing in numerous fascinating—and productive—ways.
“In spite of numerous successful biomimicry cases, its broad approach is difficult due to extreme structural complexity and the limitation imposed by material properties,” state the authors. “A simpler and desirable approach would be to combine easy processable but retaining structural complexity, especially for enhanced load-bearing applications.”

a) Front view of zeolite-templated molecular structures. b) Front view of 3D printed
zeolite-inspired structures. c) 3D view of zeolite-inspired molecular structures. d) 3D view of 3D printed zeolite-inspired structures.
The research team used an FDM 3D printer, with commercial-grade, solid PLA, to create zeolite-template carbon nanotube nets (CNTnets) structures as samples for the study. To create the CNTnets, however, the researchers first had to make junctions between the CNTs, completed as they placed two CNTs within nearly BEA channels, and then added non-bonded carbon atoms. Structures were printed using a Flashforge Adventurer 3, with the extruder heated to 210˚C and the heated bed set at 50˚C.

Specifications of the created molecular structures from MD simulations and the 3D printed corresponding ones.
Initial results suggested that porosity does play a role in deformation of parts. With less porosity, they found that elastic regimes were shorter, with greater stress required to create deformation—thus attaining the plastic ‘regime’ of the intended structure.
“… beyond the porosity of the structure, the relative tube orientation significantly affects the observed mechanical properties,” stated the researchers. “In general, we can see that the direction that is perpendicular to the nanotubes arrangements, which is the x-direction, presents the toughest and more elastic structures with decreasing porosity. Similar behavior was reported to other CNT nets, and the reasons are that is much more difficult to deform the tubes vertically than radially.”
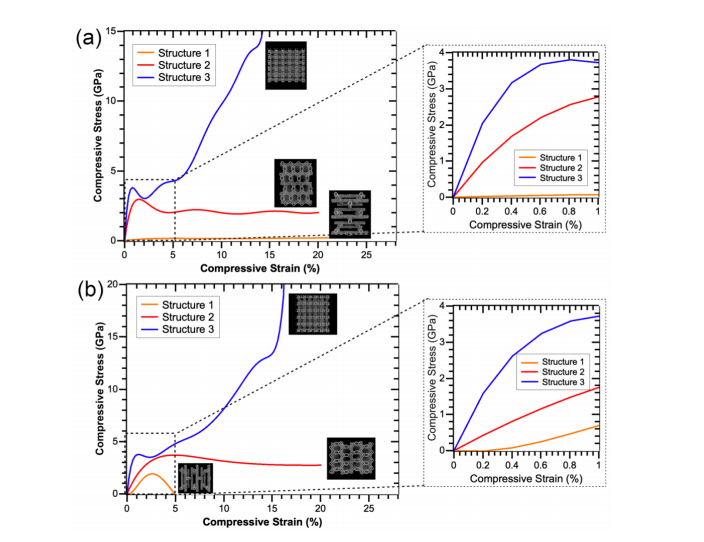
Stress-strain curves from MD simulations of structures 1, 2, and 3 for the compressive tests along (a) x-direction and (b) z-direction. The insets show the zoomed region of the initial compressive regimes.
Stress-strain curves exhibited good qualitative agreement, along with reflecting that mechanical properties are scale-dependent, determined by topology of the structure.

Experimental stress-strain curves for compressive tests of structures 1, 2, and 3 along (a) x-direction and (b) z-direction. The insets show the zoomed region of the initial compressive regimes.
Overall, results showed that the structures 3D printed by the researchers for this study were successfully fabricated as they were able to reach the intended goal of bearing the high compressive loads without giving into failure structurally.
“There is a good qualitative agreement for the mechanical behavior of the atomic models and the corresponding 3D printed macro-scale ones,” stated the researchers. “Some of the discrepancies are due to the intrinsic 3D printed layer-by-layer process.”
What do you think of this news? Let us know your thoughts! Join the discussion of this and other 3D printing topics at 3DPrintBoard.com.
[Source / Images: ‘Zeolite-templated 3D printed carbon nanotube networks with enhanced mechanical properties’]Subscribe to Our Email Newsletter
Stay up-to-date on all the latest news from the 3D printing industry and receive information and offers from third party vendors.
Print Services
Upload your 3D Models and get them printed quickly and efficiently.
You May Also Like
Consolidation in AM: How 2025 Is Shaping the Industry’s New Normal
The first half of 2025 has been marked by a clear shift in the additive manufacturing (AM) industry. Companies are no longer just focused on developing new tech by themselves....
Heating Up: 3D Systems’ Scott Green Discusses 3D Printing’s Potential in the Data Center Industry
The relentless rise of NVIDIA, the steadily increasing pledges of major private and public investments in national infrastructure projects around the world, and the general cultural obsession with AI have...
3DPOD 260: John Hart on VulcanForms, MIT, Desktop Metal and More
John Hart is a Professor at MIT; he´s also the director of the Laboratory for Manufacturing and Productivity as well as the director of the Center for Advanced Production Technologies....
Making Space: Stratasys Global Director of Aerospace & Defense Conrad Smith Discusses the Space Supply Chain Council
Of all the many verticals that have been significant additive manufacturing (AM) adopters, few have been more deeply influenced by the incorporation of AM into their workflows than the space...