US Navy’s Humble 3D Printed TruClip Design Sent to the International Space Station During Maker Faire
With such a vast amount of money saved, it’s no wonder that the humble little clip has been generating so much excitement, and not just in the Navy. When the Tru-Clip was created, the Navy agreed to share the design with the International Space Station, and this week they officially delivered it, transferring the files as part of a Technical Data Package (TDP) sent from the National Maker Faire in Washington, D.C. to the ISS. (The files had first been digitally sent to D.C. from the ship.)
Quite a bit of ceremony was involved, with members of Congress and high-ranking military officials in attendance along with representatives from Applied Systems and Technology Transfer (AST2) and Made In Space. If it seems like a lot of to-do for such a small part, consider the implications: this little six-cent clip is a perfect example of why so much effort has been put into establishing 3D printers on the ISS and on ships. Even the smallest replacement parts involve tremendous amounts of money, time and resources to deliver to such remote locations, so something as simple as a broken radio clasp throws a major cog into the wheels of important missions. Being able to print replacement parts easily and cheaply on-site is an accomplishment that has been years in the making, and the fact that those parts can be digitally sent from the middle of the ocean to outer space is even more remarkable.
“Even though these are small steps, it’s kind of a giant leap for everyone,” said Vice Admiral Phil Cullom, Deputy Chief of Naval Operations Readiness and Logistics.
Navy officials were also present at the Maker Faire to discuss the benefits of Fab Labs with attendees. The Tru-Clip was designed and printed in the Truman’s onboard Fab Lab, which was one of the first Fab Labs established by the Navy. The Truman’s lab has also been used to 3D print parts such as oil funnels, switch covers, and deck drains, as well as tubes used by the ship’s anesthesiologist.
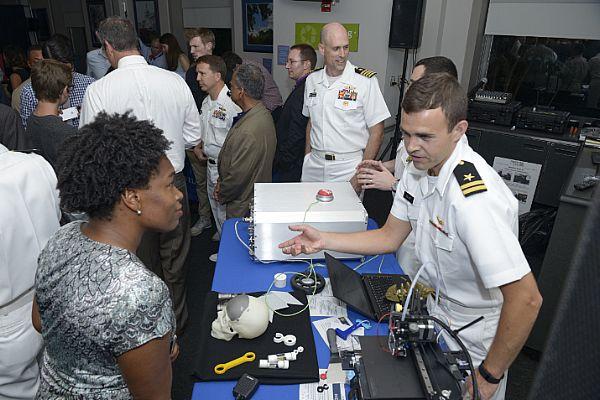
Lt. Gregory Dejute, 3d project officer for Mid-Atlantic Regional Maintenance Center, discusses Fab Labs with a Maker Faire attendee. [Image: Mass Communication Specialist 2nd Class Cyrus Roson]
“The idea behind a FAB LAB is innovation for the Sailors,” said Gas Turbine Systems Technician (Electrical) 1st Class Rebecca Zickuhr, senior facilitator at MARMAC FAB LAB. “It’s to take the technology we have and put it in their hands so that problems they see every day on the ship and the fleet they can come up with more cost-effective solutions for.”
The TDP containing the TruClip files is one of the first files to be sent to the ISS for 3D printing in space. According to Lt. Casey Staidl, the Truman’s IM-4 division officer and one of the designers of the TruClip, it’s all a bit surreal.
“It’s an incredible feeling,” he said. “This recognition isn’t something you’d expect when you start searching for a simple solution to a common problem on board. It’s a surprise, but a good one.”
Discuss further in the 3D Printed TruClip Design Goes to the ISS forum over at 3DPB.com.
Subscribe to Our Email Newsletter
Stay up-to-date on all the latest news from the 3D printing industry and receive information and offers from third party vendors.
Print Services
Upload your 3D Models and get them printed quickly and efficiently.
You May Also Like
Heating Up: 3D Systems’ Scott Green Discusses 3D Printing’s Potential in the Data Center Industry
The relentless rise of NVIDIA, the steadily increasing pledges of major private and public investments in national infrastructure projects around the world, and the general cultural obsession with AI have...
3DPOD 260: John Hart on VulcanForms, MIT, Desktop Metal and More
John Hart is a Professor at MIT; he´s also the director of the Laboratory for Manufacturing and Productivity as well as the director of the Center for Advanced Production Technologies....
Etsy Design Rule Change Reduces Selection of 3D Printed Goods
Online marketplace Etsy has implemented a rule change requiring all 3D printed goods on the site to be original designs. The update to the site’s Creativity Standards states, ¨Items produced using...
E-Beam OEM Wayland Additive Partners with USC Racing to 3D Print Titanium Exhaust Collector
Every year, standards organization SAE International holds a competition called Formula SAE, in which students from both undergraduate and graduate programs design, build, and race small formula-style race cars. For...