Global risk management company DNV GL has partnered with Siemens Energy to advance metal AM beyond the existing piecemeal solutions for quality control and certification. Siemens Energy’s experts in Finspång, Sweden, have created an automated quality control platform dubbed AM Cockpit which is being coupled with DNV’s Independent Quality Monitor (IQM) quality assurance tool. Together the two products are able to perform automated and remote certification that printed parts can be checked against an approved master print.
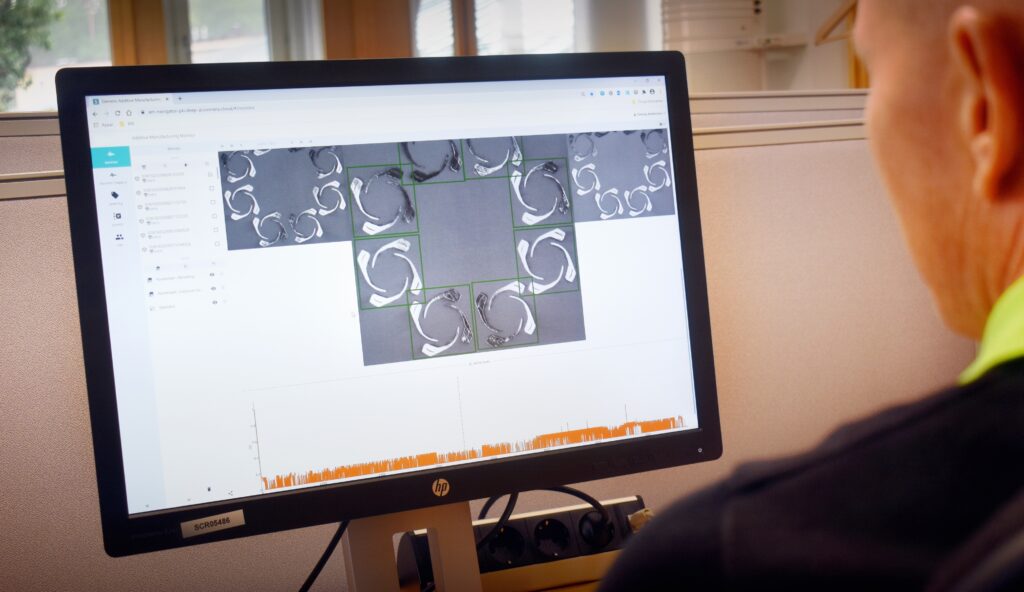
A screen shot from the AM monitor showing the printing in progress.
AM Cockpit collects sensor data streams and powder bed images from the manufacturing process in PBF systems, creating a digital summary of each printed part and highlighting problematic locations of a component. At the same time, IQM monitors data quality continuously via new algorithms and compliance logic. The IQM was developed within the EU-project InterQ project for zero-defect manufacturing.
Established Metal 3D Printing Track Records
As one of the earliest adopters of metal AM for industrial end-part production, Siemens has established itself as a leader in the space. Its newly separated Siemens Energy business went through the rigorous process of testing, qualifying, and achieving repeatability with metal laser powder bed fusion (LPBF) of gas turbine blades.
A 3D printed burner-front with about 8700 layers of high-temperature Nickel superalloy. The printing process takes about a week and is performed in a L-PBF machine with a quadruple laser system designed for serial manufacturing. The advanced geometrical shapes possible with 3D printing are particularly valuable for improved mixing of fuels and air, as well as for better cooling of the flame-exposed surfaces.
Now, it’s in the process of extrapolating that experience to the rest of the world. This included the launch of an industrial AM service network, MakerVerse, and the licensing of its data to Senvol. The latest move with DNV will see it participate in the inspection and certification of metal 3D printed parts. For its part, DNV has been leading the way in certification of 3D printed components, particularly for industries like oil and gas, as well as offshore and marine, having initiated its First-Class Approval program in 2014.
3D Printing in Decarbonization
The partnership gives both entities secure spots in not only the world of 3D printing, but in quality control for the energy 3D printing sector. As 3DPrint.com Macro Analyst Matt Kremenetsky explained in the first post in his AM Drilldown series, “The rise of AM is, above all, an energy issue, because the technology has the potential to affect humanity’s need to manage its energy consumption from both the demand and supply sides.”
Greater energy efficiency enabled through redesigned, 3D printed components will decrease energy usage and, as a result, greenhouse gas pollution (barring issues related to Jevons paradox). In turn, AM represents possibly the lowest-hanging fruit for decarbonization, explaining why so much government funding has been directed to the technology in the last year alone.
While DNV certifies these parts, Siemens Energy has focused on a key aspect of energy production that will is crucial for any number of energy generation techniques: gas turbines. Today, the majority of gas turbines rely on fossil fuels, but as hydrogen shifts to become a green technology, it will require the same improved efficiency that Siemens is applying to natural gas.
“Thanks to its design freedom, AM is the core technology that allows Siemens Energy to develop and modify gas turbines to run on green fuels, such as hydrogen,” said Hans Holmström, CEO of Siemens Energy in Sweden.
Images courtesy of DNV.