Based in Austin, Texas, ICON is among the pioneers in additive construction. Alongside firms like COBOD and WinSun, the company has achieved some of the most significant progress in 3D printing complete structures. The startup is able to pull this off with its large, gantry-style concrete 3D printer, Vulcan. Now, the company has announced that it has upgraded its flagship system to be bigger and faster, unveiling the first in a new series of homes that it hopes will redefine how we look at architecture and construction.
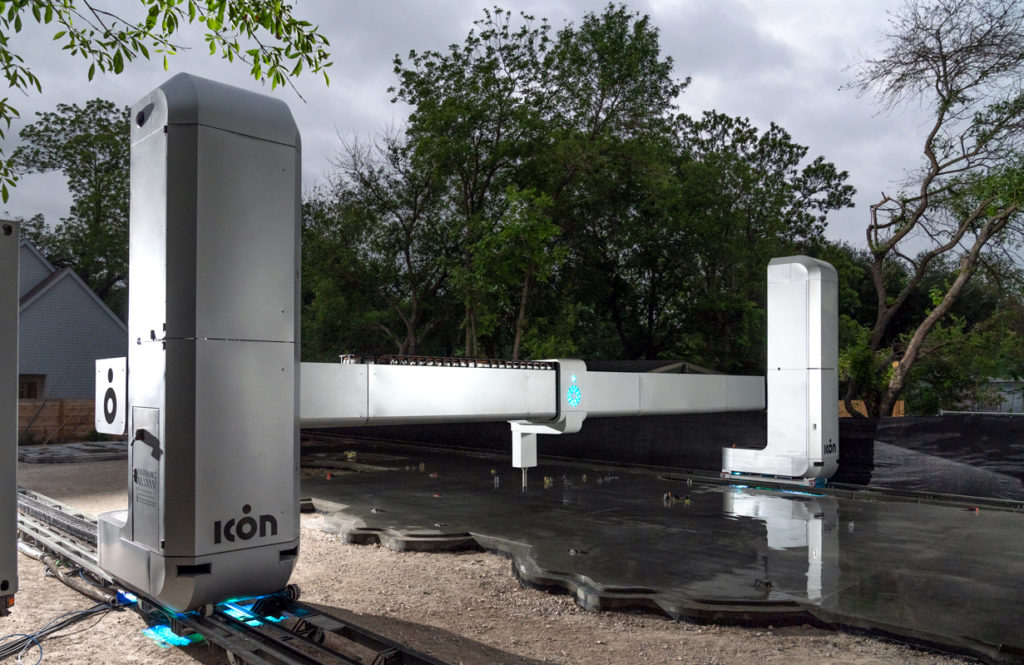
The new machine is called the Next-gen Vulcan, “engineered from the ground up for mass production of 3D-printed homes with precision and speed.” ICON claims that it is 1.5 times larger and two-times faster than its predecessor, able to fabricate structures over 3,000 square feet in size. Operated via mobile app, the system weighs a massive 9,500 pounds and features an automated control system.
To showcase the capabilities of Vulcan, ICON is launching what it calls the Exploration Series of homes, in which it will collaborate with architects and designers to “develop new design languages and architectural vernaculars with world-class architects based on the opportunities created by construction scale 3D printing.” The first home in the series, “House Zero”, was designed by Lake|Flato Architects.
“House Zero will be the most incredible 3D-printed home in the world, because it was optimized and designed specifically to be 3D printed,” said Jason Ballard, co-founder and CEO, ICON. “This is the moment when people around the world will see more of the architectural design freedom and benefits of a 3D-printed house and believe that they too would want to live in a 3D-printed house.”
With construction already beginning in East Austin, the three-bedroom, three-bathroom home will measure over 2,000 square feet with an additional one-bedroom, one-bathroom accessory dwelling unit (ADU). The structure is described as combining the aesthetics of a mid-century ranch-style home with the organic possibilities of additive construction. ICON claims that House Zero is optimized for 3D printing, saying that the home will be designed with only the resiliency and sustainability possible with 3D printing.
“If people fall in love with what we’re doing here, it turns out the Vulcan is the only construction system in the world capable of delivering this home and others like it. We are hopeful this catalyzes widespread enthusiasm and excitement for the future of construction and architecture. We’re getting ready to stand up manufacturing in our new facilities and begin larger scale projects in anticipation of such a response,” Ballard added.
So far, ICON has 3D printed 24 homes in the U.S. and Mexico. The firm claims this number to be the most completed by “any construction tech company”, but, if you compare them in terms of size to the projects completed by WinSun in China, one wonders just how true that claim would be. WinSun’s additive construction technology has been difficult to validate in the past but is said to produce concrete panels and elements in a climate-controlled environment before shipping those pieces to the construction site for assembly, essential a form of modular, additive construction. With this technique, it has produced a three-story villa, 1100-square meter luxury cottage, and a six-story apartment building.
That said, it has been difficult to fully understand WinSun’s process. Unlike WinSun, ICON 3D prints buildings on-site and in a non-modular fashion. How this changes the equation in terms of energy usage, transportation and more, I’m not sure. One thing that was demonstrated by Apis Corp when it 3D printed a structure in Dubai was that on-site additive construction is tricky business, given the equipment and material’s exposure to the elements.
ICON is additionally selling 3D printed homes in the U.S. via developer 3Strands, while also attempting to pursue social housing, disaster relief housing, and even technology for additive construction on the Moon and Mars. Though many additive construction firms have claimed that 3D printed homes will have a massive impact on the housing crisis, that may be an overblown claim. While the co-director of the Council of Community Housing Organizations, Peter Cohen, believes that this technology might be better suited for ADUs and other niche housing, 3DPrint.com Executive Editor sees a stronger and more immediate future for specific concrete elements and formwork.
Regardless of where this technology goes, the competition is heating up as a number of startups business and attention. In addition to those already mentioned, there’s Mighty Buildings and CyBe, all of whom who will have to contend with more established players in the market, such as Saint-Gobain and the PERI Group (backers of COBOD). The technology is certainly an exciting one and it is evolving much more quickly than I previously anticipated.