Binder jetting company ExOne (NASDAQ: XONE) now has a commercial license to print with aluminum-infiltrated boron carbide (B4C). The printing process, developed at Oak Ridge National Laboratory (ORNL), will let the company print neutron shielding devices, making neutron imaging safer and easier.
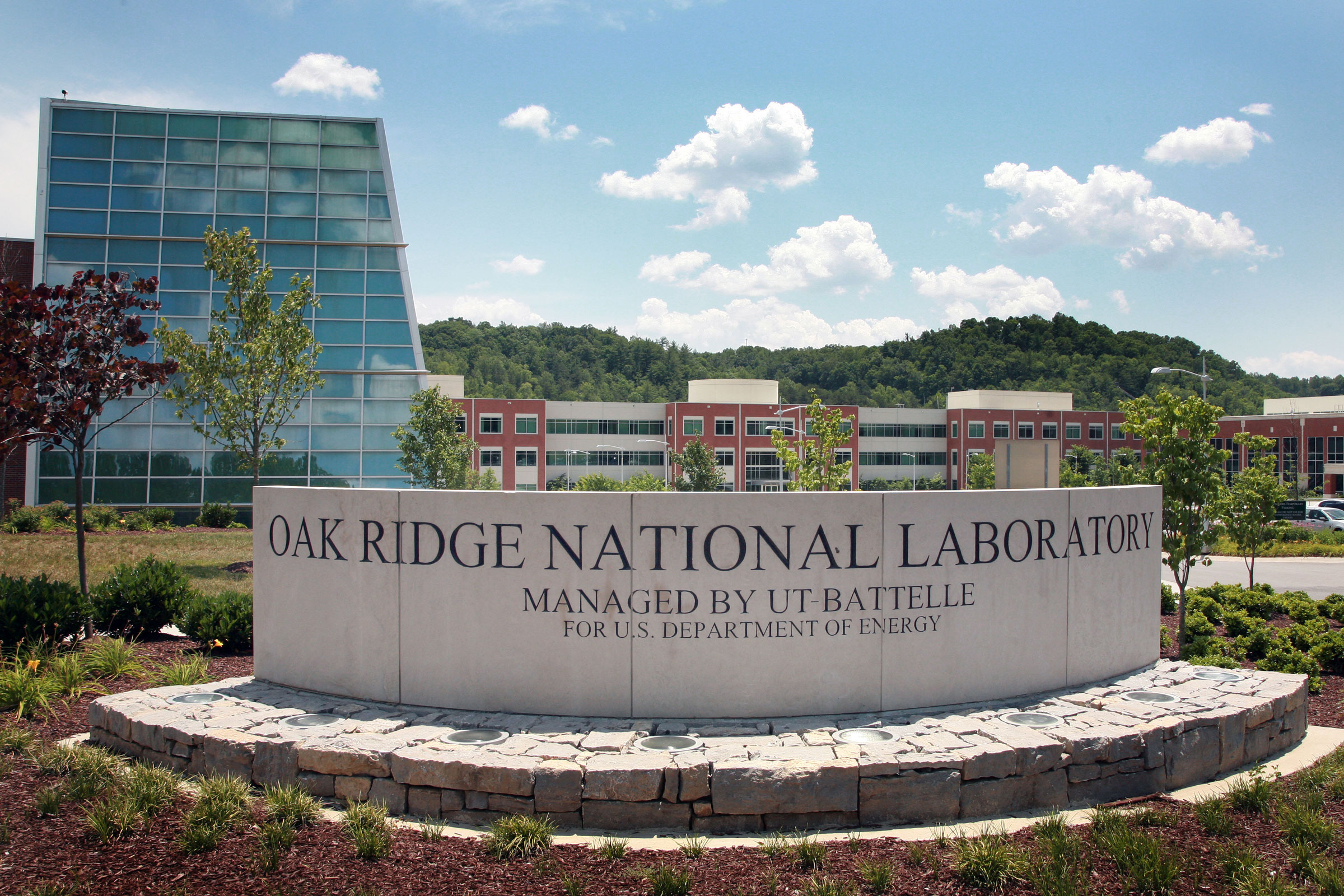
At the Oak Ridge National Laboratory, researchers focus on materials, neutron science, energy, computing, systems biology and nuclear sciences. The boron carbide material they have developed has important applications in imaging and nuclear safety (Image via UT Batelle).
Neutron scattering imaging allows researchers to look at materials at the atomic level – but not without side effects.
“It delivers results that X-Rays can’t,” said Dan Brunermer, Technical Fellow at ExOne. “Neutrons can detect light elements, like hydrogen or water, but they also penetrate through heavy elements like lead, which enables analysis of complex processes in-situ.”
But its usefulness is also its drawback; the fact that neutrons can go through heavy elements makes it harder to shield the process. Research teams across the globe have been testing boron carbide as a shield for neutron radiation. Boron carbide (B4C) is a boron-carbon ceramic, most notable as the world’s third-hardest material behind cubic boron nitrite and diamond. Its hardness, low density and good chemical resistance make it industrially useful. While the material is difficult to sinter, it makes a very effective neutron shield, prompting researchers to work with it as a binder-jetting powder.
Image 1: ORNL researchers Bianca Haberl and Amy Elliott hold their team’s 3D printed collimators (Image via Genevieve Martin/ORNL).
One team at Tennessee’s ORNL has been working with it for several years. The laboratory, funded by the U.S. National Department of Energy, has a material science department with a record of groundbreaking work in 3D printing. This time, a team led by researcher David C. Anderson developed a technique to print boron carbide into a shielding device called a collimator. The team used ExOne’s M-Flex binder jetting printer, capable of printing in sand, metal, ceramic, or composites, to print in boron carbide powder.
During the process, they combined the boron carbide with aluminum via infiltration, a process where a ceramic preform is “soaked” in molten metal in a pressurized environment until the ceramic takes in the metal. The ORNL team compared the process to “water [being absorbed] into a sponge.” The result was a metal-matrix composite that is both strong and lightweight.
While ExOne already had R&D rights to the printing technique, this new development gives them the commercial license. This means they can now start making boron carbide collimators, shielding equipment, and the basic components for neutron scattering research (which gives researchers a way to study atomic structure). They will also be working with ORNL on printing collimators for the laboratory’s own neutron scattering experiments.
“This research and the resulting license agreements demonstrate the value that the DOE Manufacturing Demonstration Facility at ORNL delivers to the manufacturing and science community at large,” said Brunermer.