Conflux Technology and GKN Additive have announced that they will collaborate on the development and production of 3D printed heat exchangers. One of the most indispensable industrial components for a multitude of critical sectors, heat exchangers are necessary to more or less any process involving heating and cooling. 3D printing’s unique ability to create geometrically complex parts, which in this case can help optimize ventilation systems while also achieving reduced weights and faster lead times, has led to increasing interest in 3D printed metal heat exchangers in recent years.
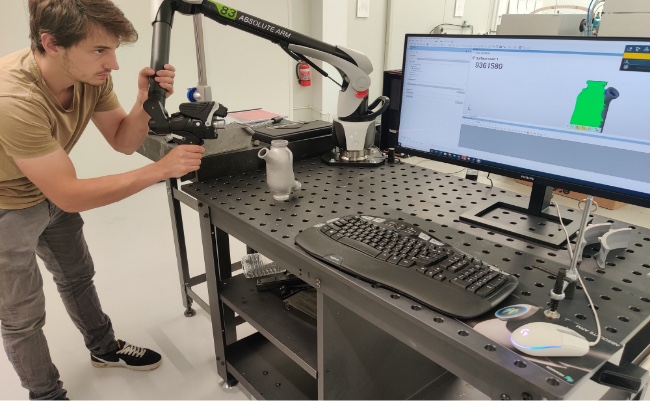
Conflux’s CEO and founder, Michael Fuller, founded the company in 2015 after a 15-year career as an engineer in F1 auto racing. Based in Australia, the firm is one of the pioneers in the field, having achieved its first patent for a heat exchanger produced with metal additive manufacturing (AM), the Conflux Core, in 2017. Also in 2017, German AM leader EOS — which makes the M 290 and the Aluminum AlSi10Mg used to print the Core — invested in Conflux via EOS’s investment arm, AM Ventures. Along with Australian VC fund Acorn Capital, AM Ventures invested another $6.3 million dollars in Conflux last fall.
In a press release announcing the partnership, Fuller commented, “We’re excited to be able to offer our customers access to GKN Additive’s manufacturing services. Its capability to manufacture large volume orders in Europe is a perfect fit for our EU customers looking for serial production near point of use. Being able to provide our technology to their vast array of top tier and technologically advanced customers is already proving fruitful.”
One such GKN customer is BMW, who just announced that the Industrialization and Digitalization for Additive Manufacturing (IDAM) resulted in two AM plants being set up and ready for business. Aside from the BMW AM Campus in Germany, the other plant is operated by GKN in Switzerland. It will be interesting to see if one of the components GKN ends up producing for BMW is a Conflux heat exchanger. In any case, the strong automotive experience of both companies clearly makes the partnership a logical fit.
Partners like GKN, which are parts of larger conglomerates, are going to be increasingly integral to the scaling up of AM sector startups like Conflux. And scale is probably the main thing the automotive industry brings to the table as a customer for the AM sector, which is what the automotive sector has always brought to the table on a macroeconomic level. This doesn’t just mean the number of parts that are initially able to be 3D printed. Even more significantly, at what is still such an early phase in the industry’s history, it means the size of the supply chains that AM is integrated into: the larger the overall market it gets a foothold in, the more long-term potential there is for the technology to grow into eventual use for mass production.
About 100 million automotive heat exchangers are produced each year, so, if even a small percentage of that market is replaced by 3D printing long-term, that would still constitute mass production for AM. Producing at that scale in this sector would reliably continue to lower costs and increase revenues for metal AM as a whole into the next decade, which is the type of development that will be needed for the industry in general to continue expanding into others areas that capitalize on the technology’s potential.
Images courtesy of Conflux Technology