One of the competitive edges inherent in additive manufacturing (AM) that giant global corporate operations seem most intrigued by is the potential to create distributed supply chains. At the same time, that will remain largely just a possibility, so long as the networking software capabilities in the AM sector lag behind the progress made in hardware.
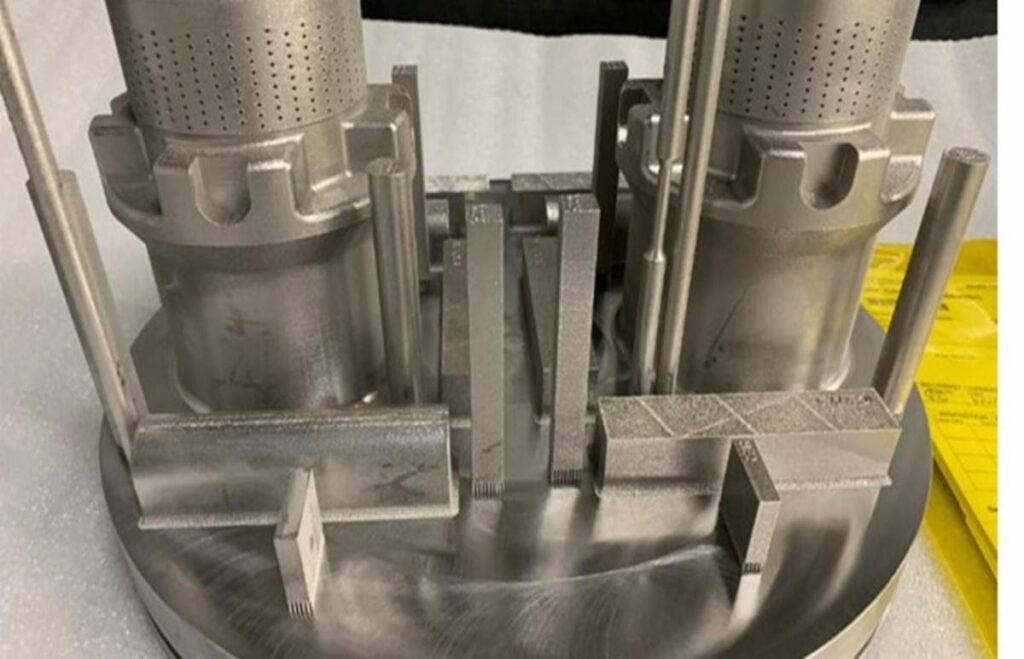
Given that much of the most significant progress in those networking capabilities has happened within the last couple of years, publicly available examples of companies using AM to achieve truly repeatable, distributed production are still somewhat scarce — especially regarding metal parts for heavy industry. However, Velo3D, the Silicon Valley-based original equipment manufacturer (OEM) of metal AM platforms, has just released a case study of its project to create a distributed supply chain for metal parts used in oil & gas.
Specifically, Velo3D worked with IMI Critical (a division of leading UK engineering firm IMI plc) to print a metal choke valve for a major North American oil & gas producer. Along with five contract manufacturers (CMs) — based in three different countries spanning North America, Europe, and Asia — Velo3D and IMI printed the same choke valve in all the different locations, about a year after the part was initially printed by Velo3D. Notably, the part conforms to the API20S specification of the American Petroleum Institute (API), meaning that the choke valve meets the industry standard.
In the case study about the distributed supply chain project, the director of new product development at IMI Critical, Steve Freitas, explained, “Now that we’re scaling up our retrofit business around the world, we recognize the value of having an end-to-end AM solution that allows for scaled production without compromising quality and repeatability. We find the Velo3D approach to be very attractive in that regard. We don’t have to reinvent the wheel each time because we have qualified build recipes and print file instructions that are locked. It also saves costs due to not having to repeat qualification. This maintains IP for the print instruction file, which is increasingly important as we deploy globally.”
The key to the whole project is referred to in the case study as the “Golden Print File”, which was created by Velo3D in 2021 and locked in IMI’s catalog, then sent to the five different CMs, as well as Velo3D headquarters, for the experiment. Two choke valves were printed at each location, all of which conformed to each other, to the original print, and to API standards.
The distribution of the Golden Print File sounds like it relied on industrial NFTs. I’m sure that other companies — and militaries — have already been using blockchain for distributed production of printed metal parts. The notable thing here is that metal AM is becoming universalized enough to the point where CMs across the planet could realistically achieve distributed supply chains of printed metal parts within years, not decades.
It would require significant capital investment on the parts of both governments and corporations. But until very recently, all the investment in the world in AM still wouldn’t have led to broad-sweeping distributed manufacturing becoming a reality. A multitude of diverse factors and events over the past ten years have made that reality seem far more feasible.