While AM has been dubbed as the 4th industrial revolution, it has made minimal in-roads into the arena of large part manufacturing. Among all the metal AM technologies, Directed Energy Deposition (DED)technologies are more easily scalable than others. Therefore, DED is well suited for manufacturing large parts. Surprisingly, the adoption of DED technologies has been much slower than other well-known 3d printing technologies, such as Powder Bed Fusion (PBF), Material Jetting (MJ) or Fused Deposition Modeling (FDM). However, this is changing. Aerospace and defense industries are leading the way in exploring and adapting large format metal printing.
DED has come a long way. Baker’s 1935 patent on ‘Method of Making Decorative Articles’ is arguably the first known patent using a directed energy technique. While the process was not digitally driven, it, nonetheless, demonstrated the potential of tool-less manufacturing using a layer wise approach. Today’s DED technologies are far more sophisticated and fully driven by digital manufacturing methodologies. However, there remains some significant barriers to its widespread adoption for large part manufacturing. Enhanced build rate, consistent build process, real time process monitoring and control, stress & distortion mitigation strategies are some of the essential requirements to reach the dream of producing large metal AM parts that can journey to outer space, fly in an aircraft around the earth, explore the deep seas or produce energy at a power station with 24/7 reliability.
Figure 1. Complex geometries printed using DMD technology. (a) A hollow elbow, (b) A hemisphere, (c) a rocket engine nozzle (courtesy NASA MSFC) and (d) Turbine engine part.
DM3D Technology LLC, a leading DED technology and service provider, has taken on the mission to make large-scale metal AM parts a reality. DM3D’s proprietary Direct Metal Deposition (DMDâ) is one of the DED technologies that uses high power laser as a heat source and metal powder/wire as feedstock to 3D print metal parts layer-by-layer directly from the CAD data (Fig. 1). We realize that developing large format AM technology is a task that we cannot realize alone. The process starts with identifying candidate parts, analyzing technical and commercial challenges, and laying out potential integrated solutions to these challenges to maximize our chances of being successful. For the past five years, our team has been working tirelessly with our customers and suppliers towards achieving this goal.
Figure 2. DMD Multi-nozzle system. Left top insert shows the dual nozzle technology for rapid 3D deposition.
Like in any product development, a key mantra to success is cheaper, better, and faster. Enhanced build rate is a must-have factor to make the cost of large parts affordable and to reduce lead time. Some DED processes have reached this target by using high energy input and large beam size. However, these advancements have come at a cost, such as a reduction in complex feature capability and process resolution while introducing very large distortions in the part. In order to overcome this challenge, our team at DM3D took a different approach. We designed, fabricated, and commissioned a new generation multi-nozzle DMD system (Figure 2). Some features of this Multi-nozzle DMD system are:
- Build envelope of 10ft diameter and 10ft height
- Doubled the throughput using two simultaneously operating process heads with capability to add two more process heads
- Patented closed-loop feedback control for the process stability and quality of the build
- Coaxial nozzle with local shielding of melt pool to provide high quality material
- A large rotary table with tiltable process heads (±45°) allow for printing overhang structures
- Large capacity high feed rate pre-heated powder hoppers
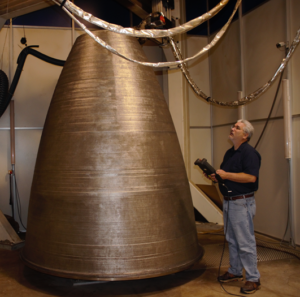
The next critical step in maturing a large part printing process is candidate part selection and build process optimization. We worked with NASA on the RS-25 engine nozzle liner (with 97in or base diameter and 111in height) as a candidate part. The build approach started with design of experiments (DOE) based process recipe optimization followed by a thermal, stress and distortion simulation of the build process using ANSYS software (Fig. 3) and subsequent compensation of the distortion to print geometry. This was followed by a successful build process (Fig. 4) and finally, a structured light geometric inspectional (from Hexagon) scan on completion of the build (Fig. 5). Replacing conventional manufacturing with AM for a RS-25 engine liner is estimated to result in 2X to 10X schedule reduction and a significant cost savings (up to 50%). There is significant technological and commercial benefit of printing such large parts using DED technology as indicated by Paul Gradl, a Principal Engineer at NASA MSFC and a world-renowned AM expert, “NASA has established these public-private partnerships with industry and academia to advance new approaches, process build volumes, novel alloys, and component demonstrations using additive manufacturing,” he said. “The goal is to increase the technology readiness level to allow infusion into future NASA missions and commercial space applications.”
We hope that this successful demonstration of printing large rocket engine parts will open doors for large-scale metal AM and directly benefit the fast-growing commercial space industry which is in constant need of large structures. Rapid manufacturing speed, along with the ability to incorporate new design changes with minimum effort, will be a perfect tool for current and future design & manufacturing engineers and accelerate innovation to a greater benefit of our society.
DM3D will be attending Additive Manufacturing Strategies, taking place in New York City from February 7-9, 2023. DM3D Technology President Bhaskar Dutta will be participating on “Panel 1: The Future of DED and WAAM” on February 7. Register for your ticket to attend here.