Essentium Inc., an Austin-based original equipment manufacturer (OEM) specializing in extrusion additive manufacturing (AM) platforms, announced that the Maine Air National Guard employs the company’s High Speed Extrusion (HSE) 180 ST system to produce training aids. Specifically, Maine’s 101st Air Refueling Wing (ARW) has printed replicas of outboard aileron balance tabs in Essentium PCTG filament, used for training guardsmen to repair those critical parts.
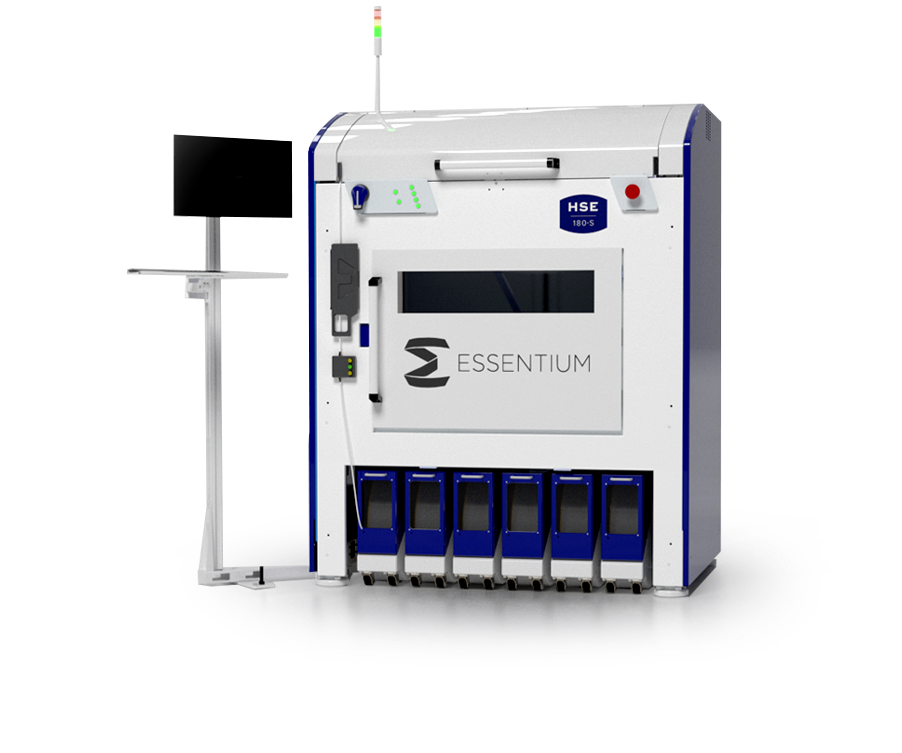
The outboard aileron balance tab is part of an aircraft’s flight control surface, which, as the name suggests, facilitates the aircraft’s ability to stay in balance while in flight. The parts are in frequent need of repair, making familiarity with the maintenance, repair, and overhaul (MRO) process on balance tabs especially crucial for aircraft mechanics and engineers. And, as with essentially all aircraft parts these days — in both the military and civilian aerospace markets — balance tabs are in short supply, meaning there is an even shorter supply of extra parts available to be used just for training exercises.
In a press release about the Maine Air National Guard’s use of the Essentium HSE 180 ST, the company’s CEO, Blake Teipel, commented, “This valuable tool has also caught the attention of other local military components, such as the Maine Army National Guard, who began requesting similar training aids for their rotary aircraft. We’re excited that the Essentium HSE is currently being used as a cross-functional force multiplier that can shape the future of readiness across the joint force.” Master Sgt. Jason Howes explained, “You can’t put a value on having proficiently trained guardsmen. The confidence they get from putting their hands on the product, understanding what the result will look like, and gaining muscle memory is simply invaluable.”
Additionally, as the press release notes, the likelihood of destroying aircraft parts with improper repair is another factor in favor of using realistic replicas. Thus, even if there is an unexpected reversal of the shortage in aircraft parts, the use of replicas would be a much less costly option for training purposes than real balance tabs, or any other mission critical element.
Finally, the particularly ingenious aspect to producing training tools with AM is that it simultaneously accomplishes the task of two different forms of training — the other form, of course, being the training of guardsmen to use the machines that print the training aids. This is obviously applicable outside of this one area of the military, as is implied by Essentium’s CEO in the above quote. It is also applicable to more or less any other field one can think of, where employees have to be trained to repair expensive parts.
Making training aids is not a new use of AM, by any means. However, these particular use-case examples will take on new significance the more that the AM sector faces labor shortages while it also tries to scale up. The fact that the military is at the forefront of this overlap between training exercises and advanced manufacturing, is just one of the many pieces of evidence suggesting that the future of the 3D printing labor pool, as a whole, is already largely being shaped by the armed forces.