Since first introducing the system, Thermwood has been steadily adding to it, introducing new features such as the recently developed Universal print head and several new software features. One of Thermwood’s goals is to use the system to 3D print autoclave capable tooling from high-temperature, carbon fiber-filled thermoplastic materials, and they’re getting closer to that goal.
Recently, Thermwood engineers used the LSAM system to 3D print 50% carbon fiber-filled PPS panels that held vacuum to an industry acceptable level in independent testing. The testing was carried out by the Fleet Readiness Center East, and the results met FRC’s criterion that the bag not lose more than 2 in Hg over five minutes.
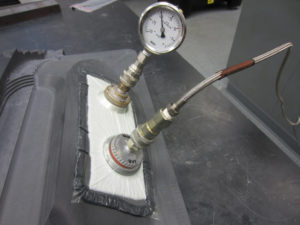
Other companies have tested tools 3D printed by Thermwood from 20% carbon fiber-filled ABS, and discovered that they held vacuum to an acceptable level without any sealer or coating. Unfortunately, the ABS material is not suitable for high-temperature applications. Nevertheless, several parts have been made using those tools under vacuum at room temperature or slightly elevated temperatures.
Thermwood also 3D printed a 50% carbon fiber-filled PPS mold that hasn’t been tested yet. The company’s ultimate goal is to create molds that can be used in a production autoclave, molding finished parts that can be used in end-use applications.
The recently 3D printed parts are an example of the effectiveness of Thermwood Corporation’s recently developed Universal print head, which uses a different approach from standard 3D printing techniques, many of which involve extruding layers of material onto a heated platform in a heated build chamber. With the Universal print head, no heat is required other than the heat in the print head itself. Each layer is 3D printed at a speed that allows it to cool to the proper temperature for the next layer to adhere, and the speed is controlled based on the rate of cooling. Thermwood calls it “an exercise in controlled cooling.”
According to Thermwood Corporation, this technique produces stronger, better parts, which are further improved by the company’s patent pending compression roller. The roller follows behind the print nozzle as it lays down material, and flattens each layer to press it tightly to the layer beneath it. This process creates parts that are more solid and void-free, and thus stronger.
We’re always interested to check in with Thermwood Corporation and see what they’re doing with their LSAM technology, and according to the company, they’re continuing to improve the system and its software. LSAM and its Print3D software operate within Mastercam and work with most CAD file formats, and the company maintains a consistent software development effort in order to keep it updated with new capabilities and features. Discuss in the LSAM forum at 3DPB.com.