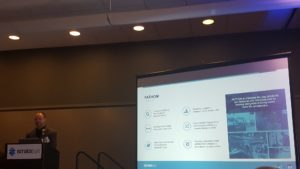
“It is really exciting to partner with Desktop Metal because we get the opportunity to connect a broader engineering and manufacturing market with a lower barrier-of-entry solution for metal additive technologies. What is possible with current metal 3D printing equipment is exciting but it is still cost prohibitive so the adoption of metal 3D printing is slow,” FATHOM’s Advanced Technology Manager Michael Duncan told 3DPrint.com. “We know that the market is more than ready for a system that is both office friendly and economically accessible. Now, more design and engineering teams will have the opportunity to explore what’s possible with metal 3D printing and many new application innovations will develop at a much faster rate.”
Ric Fulop, CEO and Co-Founder of Desktop Metal, said, “We are excited to be partnering with FATHOM both as a manufacturing service center and a sales partner as we look to broaden the adoption of our metal 3D printing systems. Rich Stump and Michelle Mihevc have built an incredible team who will be integral in expanding market opportunities and driving the growth of our customer base across diverse industries.”
Desktop Metal’s Studio system was 3D printing onstage at RAPID + TCT when Ric Fulop presented in a morning session [Photo: Sarah Goehrke]
Duncan told 3DPrint.com, “The Studio System allows for metal part design and refinement in a way that is familiar to designers and engineers today. Safe and easy to use like many FDM-based systems. The Production system will enable a better Direct Digital Manufacturing (DDM) experience. Part designs can be created with unique features or assembly options without the constraints of tooling requirements such as draft, wall thickness, lightweighting, or complex internal passages normally difficult if not impossible to realize using traditional technologies. All the advantages of metal 3D printing like speed and freedom of design can now be easily realized right in your office. Now, the only limitation really is your imagination! Also, we strongly feel that there is a huge opportunity to use this technology for accelerating tooling applications, such as injection molding, jigs, and fixtures.”
Desktop Metal and Rize were represented at the Caelynx booth at Science in the Age of Experience [Photo: Sarah Goehrke]
The cloud-connected furnace combines SIC high-powered microwaves and SIC heating elements to sinter the parts once the primary binder has been removed. It uniformly heats parts to a temperature just below their melting point, and can reach up to 1400°C. Aligned with the company’s goal of making metal 3D printing easier and more accessible to users, the system has web-based software and features fast material changes and hand-removal of supports. It’s also designed for prototyping, as it can produce near-net-shape metal parts.
“Prototyping small precision parts intended for volume powder metal production processes such as Metal Injection Molding (MIM) or Pressed Metal (PM) is difficult. Developing tooling and qualifying production methods can be a long iterative process. Desktop Metal 3D printing solutions provide more competitive options than traditional tooling resulting in accelerated part development. Users can much more easily build metal parts for evaluation, functional testing, and production use. It’s also exciting how many materials will be made available. Desktop Metal is planning for a variety of options, from steels and aluminum to superalloys and titanium,” Duncan told 3DPrint.com.
Laser-based processes weld parts to to the build plate, but the DM Production system creates parts that are surrounded by loose powder: software will arrange the parts in order to maximize the build area in all axes. This allows the full build envelope to be used, which means higher productivity per build. The technology is bi-directional, so two full-width print bars, with over 32,000 jets, work with powder spreaders to both spread powder and print in one pass over the build area. This jets millions of droplets per second, so that whenever there is movement in the printer, there is also printing.
“Current metal 3D printing technologies require support structure removal and second operations such as processing feature edges or roundness of holes, as well as removing trapped metal powder. Much of the cost, lead-time, and part accuracy result from these extra steps,” Duncan told 3DPrint.com. “I’m looking forward to the DM Production System that will be able to produce net shape parts in a variety of metals with minimal second operation process steps. There isn’t another system that can provide as much part design freedom for prototype and production metal parts that fast.”
Share your thoughts on this partnership in the FATHOM forum at 3DPB.com.